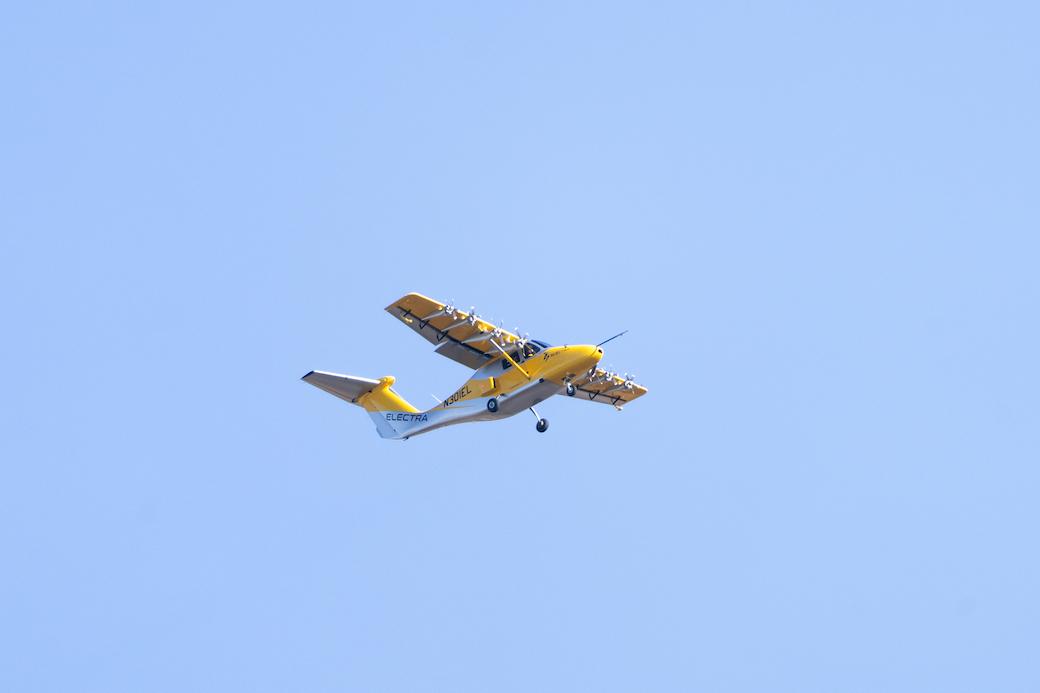
Electra is developing an aircraft that can take off from an area the size of a soccer field with a 150-ft. ground roll.
U.S. startup Electra.aero has completed its first pair of piloted test flights with its full-scale hybrid-electric short-takeoff-and-landing (eSTOL) technology demonstrator, including those in both all-electric and hybrid-electric configurations.
The EL-2 Goldfinch first flew on Nov. 11 in an all-electric flight from Manassas Regional Airport in Virginia, with test pilot Cody Allee. The hybrid-electric flight, also piloted by Alee from Manassas, took place on Nov. 17, and saw the aircraft reach an altitude of 3,200 ft., while covering around 30 mi. during its 23-min. flight.
Successful completion of the piloted test flights was described as a “major milestone” by Electra General Manager J.P. Stewart, who highlighted the importance of proving out the aircraft’s unique blown-lift architecture—as well as the all-electric and hybrid propulsion configurations—while using a full-scale, piloted demonstrator.
According to Stewart, the flights were intended to generate information on a number of operational choices: controlling the turbogenerator; determining when to use the battery versus the turbine; understanding different failure cases; validating the handling qualities and performance of the aircraft in slow-flight and STOL configurations, and other topics.
“This airplane is helping us take those core technologies from being an abstract concept into a reality,” Stewart tells the AAM Report. “Like every test program, you build up gradually to explore from the known into the unknown aspects of the airplane, and you do that in a very methodical process that mitigates risk along the way.”
Electra is developing an aircraft that can take off from an area the size of a soccer field with a 150-ft. ground roll and carry nine passengers or 2,500 lb. of cargo up to 500 mi. The EL-2 operations will include flight tests of its blown-lift technology, which uses distributed electric propulsion.
With a gross weight of 3,100 lb., the demonstrator houses a turbogenerator in the nose, battery packs under the floor, a two-person cockpit and a large T-tail to counteract the pitching moment generated by blowing the wing.
As the flight-test program advances, Stewart says the company plans to continue expanding the demonstrator’s flight envelope.
“We’re going to fly faster and we’re going to fly slower. And as we start flying slowly, in particular, we’re really looking to validate the models that we have built for performance and stability and control.” he explains. “Where on the wing does the air flow separate? What is the slowest possible flight? How does the expected power compare to the actual power? Those are examples of questions we want to answer through these tests.”
A key aspect of Electra’s aircraft is the blown-lift concept, in which the propeller slipstream interacts with the wing to increase lift, enabling the aircraft to take off using less energy at lower speeds.
“We have an airplane that takes off at 30-35 kt., compared to 70-90 kt. for the typical plane of this class,” Stewart says. “Doubling the speed results in four times the kinetic energy, and that extra energy requires a lot of extra distance to accelerate or decelerate on takeoff and landing. That’s really what this boils down to—flying slowly under control allows you to fly in and out of smaller spaces.”
The data generated from the flight-test campaign, as well as from concurrent wind-tunnel testing, will be fed into models the company will use to develop and validate the performance of its next aircraft, a full-scale prototype that Electra expects to make its first flight in 2026.
Following this nonconforming prototype, the company plans to build a certification test aircraft, aiming for service entry in 2028.