
Multisensor pods will be mounted under the Caravan’s wing.
Xwing Partners With NASA on Automation
Xwing has signed a three-year partnership with NASA to study performance, procedures and risks for flight automation.
The San Francisco-based startup initially plans to study hazards, performance and safety benefits of its vision-based autoland system. Data and lessons learned will be shared with NASA.
Researchers at NASA will use the information to validate and evaluate safety management systems and algorithms, as well as provide risk analyses and prognostics.
“Emerging aviation relies heavily on advanced automation to ensure safety,” says Misty Davies, NASA system-wide safety project manager. “This partnership will help NASA understand the real-world challenges that industry is facing.”
Xwing plans to retrofit an undetermined number of its Part 135 commercial cargo fleet of Cessna Caravans with electro-optical and infrared cameras in underwing pods. Computer vision software will use the imagery to identify the runway, centerline, threshold markings and other cues to line up an aircraft for final approach and landing. The sensors will also be used for automated taxiing and detect-and-avoid capabilities.
“It’s about supplementing GPS/inertial-based navigation with a separate independent system to validate the position of the aircraft, especially on final [approach],” says Xwing CEO Marc Piette.
Xwing is working to obtain a supplemental type certification (STC) for the sensor pods, which is “in the final phases,” he says. Flights with the pods would begin once the STC is obtained.
“This first STC is not going to be integrating with the flight control system, but it acts as a data collection mechanism that we could deploy in the 14 states that we currently fly to today,” Piette says. The pods also house radar and lidar sensors.
Data collected from the Part 135 fleet will be used to validate and improve Xwing’s algorithms and will supplement and refine work done using Xwing’s modified Caravan technology testbed. That aircraft demonstrated autonomous gate-to-gate flight and taxiing last year.
Xwing is competing against startups such as Reliable Robotics and Merlin Labs to automate aircraft flights, including cargo operations. Removing a pilot from cargo flights would significantly reduce costs.
In 2021, Xwing signed a joint development technology agreement with Caravan manufacturer Textron Aviation to accelerate the integration of autoflight technologies into existing and future aircraft.
As part of UPS’ regional air cargo network, Xwing flies 35 Caravans about 400 flights a week to 57 locations across the U.S. to gather hands-on operations experience.
“If you think about deploying this autonomy at scale, it’s not just about flying the airplane,” says Jesse Kallman, Xwing’s vice president of commercialization and strategy. “A lot of it is ground taxi operations, loading and unloading,”
Programming aircraft to deal with uncertainties also needs to be figured out. That’s especially the case with some of the small, nontowered airports Xwing’s pilots fly into today, says Piette, who likens the uncontrolled airspace to the “Wild West.”
“You’ve got crop dusters without radios flying around. You’ve got skydivers that are jumping close to the pattern. Student pilots are flying around. You’ve got people landing in both directions on the same runway,” he says. “You’ve got to coordinate all of this.
“People really like to focus on automation of the aircraft and the fact that the aircraft can do a takeoff and landing on its own,” Piette says. “That’s not where the challenge is. It’s being able to handle all of these curveballs that can be thrown at the system and do it gracefully.”
—Garrett Reim in Los Angeles
New Interfaces Critical to Space Servicing
Standardized mechanical interfaces for grappling and connecting spacecraft are critical to enabling the growth of the in-space servicing, assembly and manufacturing industries.
A lack of standardization is holding back growth for the nascent sectors, a panel of industry players told the Satellite Innovation conference in Mountain View, California, on Oct. 11. Interfaces are needed to grab satellites for servicing, connect fuel nozzles, and manipulate prefabricated pieces for spacecraft or space station assembly.
“If we’re going to grow, we need to set up standard interfaces, as well as work with the government to create standards from a regulation standpoint,” said Robert Hauge, president of Northrop Grumman company SpaceLogistics.
In 2020, SpaceLogistics’ Mission Extension Vehicle-1 (MEV-1) docked to communications satellite Intelsat IS-901. The vehicle is using its own thrusters and fuel to extend the life span of that client satellite.
Connecting to any satellite in geostationary orbit is difficult because they were not designed for docking or servicing, Hauge said. Northrop created a workaround, connecting the MEV-1 by grabbing IS-901’s liquid apogee engine nozzle.

“We extend the lance in through that engine nozzle. We go through the narrow portion, open a set of fingers and pull the two spacecraft together. That’s essentially all it takes,” he said. “It’s taken us 10 years of maturing that technology.”
SpaceLogistics plans to launch in 2024 a next-generation servicing spacecraft, called the Mission Robotic Vehicle, that would use a robotic arm to install mission extension pods onto client satellites. It would be easier if satellites had a standard docking interface, Hauge said.
“We absolutely want to have a more universal docking capability,” he said. “But the issue is this industry needs to have standards. We’re working with groups like Confers [the Consortium for Execution of Rendezvous and Servicing Operations].”
There are two important characteristics companies need to focus on, said Rob Schwarz, chief technology officer of Momentus, a company that is developing in-space services including refueling, repositioning, repairing and deorbiting.
“Having an interface that’s an open standard, so that other people can copy it and reuse it, and being first I think are the keys,” he said. “It’ll be the de facto ‘Easy Button’ for other people to press if it’s close enough to meeting their technical requirements.”
There are likely to be several standards for spacecraft interfaces. “There’s not going to be a single standard that everyone follows because [there are] going to be docking interfaces that require humans to pass through them and docking interfaces for microsatellite constellations,” Schwarz said.
In the near term, before standards are established, the satellite industry is likely to work through a transition period, said Andrew Rush, president and chief operating officer of Redwire.
“We have to field things that are a little more general; that can interact with assets that don’t have gas caps [or] that can interact with assets that are of many different shapes and sizes, which is why low-cost modular robotics is really critical for us to be able to do that in a cost-effective way,” he told attendees at the conference.
—Garrett Reim in Los Angeles
Aura Details ERA Electric Regional
French startup Aura Aero is looking to acquire a small carbon-fiber specialist as it intends to use the material for the wing of its planned 19-seat Electric Regional Aircraft (ERA).
The fuselage of the hybrid-electric ERA will be aluminum, but the high-aspect-ratio wing will be carbon fiber for performance reasons, Jeremy Caussade, co-founder, CEO and chief engineer of the Toulouse-based startup, told the European Regions Airline Association general assembly in Portugal on Oct. 12.
Founded in 2018 to first develop a family of two-seat aerobatic training aircraft as a precursor to a small electric regional airliner, Aura is planning to fly the ERA prototype by the end of 2024 or early 2025. And the company expects to be on the market by late 2027 or early 2028, Caussade said.
The startup has announced letters of intent for more than 330 aircraft from a lessor and nine airlines. The ERA is designed to carry 19 passengers or 2,500 kg (5,500 lb.) of cargo for 215 nm at 300 kt. (345 mph) on all-electric propulsion, with a 45-min. reserve, increasing to 1,000 nm with hybrid-electric power.
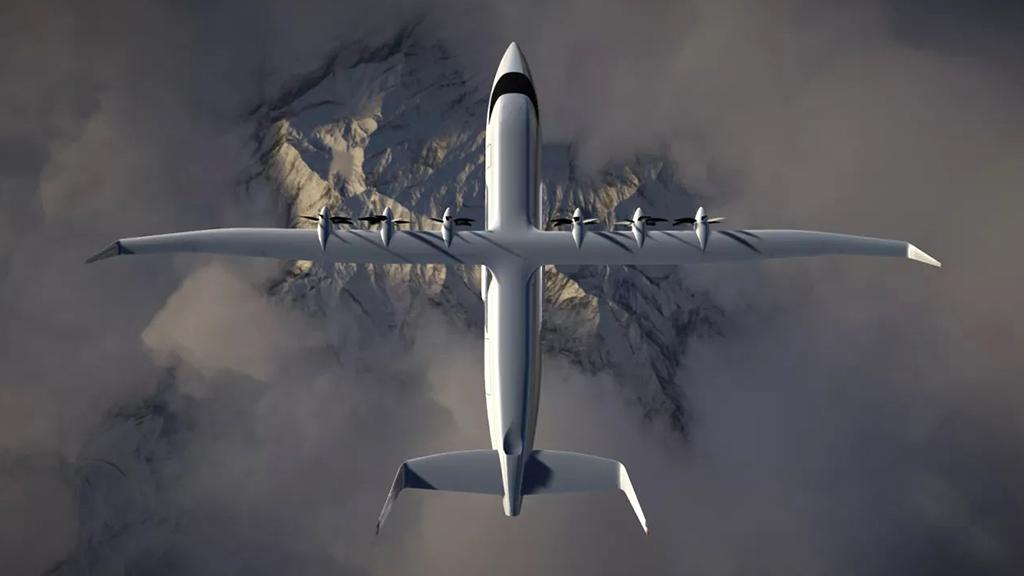
Aura is working with Safran on the 800-volt electrical distribution and protection system and electric engines, as well as discussing the turbogenerator for hybrid propulsion, Caussade said. The startup also plans to outsource design and manufacture of the aluminum pressurized fuselage.
“We are working with big OEMs on all the critical parts,” he said. “The only one we decided to do internally is the fly-by-wire system, because in Toulouse we have all the competencies.” Aura also believes a new regional aircraft with large-airliner safety needs a system architecture and centralized computing function with a design assurance level that requires internal development.
Aura also wants to keep design, and potentially initial production, of the wing in-house because the aircraft’s battery will be integrated into its structure. “We are focusing on the carbon-fiber wing because we have the battery inside,” he said. “This is quite new, so we need to master overall what we are doing.”
The startup also wants to be able to minimize the amount of carbon fiber to reduce cost and recycling, but also as part of a push to cut the amount of fossil-based materials used in the aircraft. This includes plans to use materials such as basalt and flax/linen fiber composites in the cabin and galley of the ERA.
—Victoria Moores in Vilamoura, Portugal
USAF Defines First eVTOL Missions
Flying personnel or equipment around U.S. Air Force test ranges has been identified as a likely early application for electric vertical-take-off-and-landing vehicles. But such lower-risk missions are seen as a precursor to flying VIPs on the military equivalent of air taxis.
The missions are identified in a request for information (RFI) published on Oct. 6 by the Air Force Life Cycle Management Center’s Mobility and Training Aircraft Directorate. Responses to the RFI are intended to help the Air Force understand the cost benefit of electric vertical-takeoff-and-landing (eVTOL) vehicles versus conventional rotorcraft.
The Air Force’s Agility Prime program was launched in 2020 with the objectives of accelerating the domestic eVTOL industry, by providing access to Air Force airworthiness expertise and test resources as well as identifying early procurement opportunities within the Defense Department.
Agility Prime is widely judged as a success in supporting testing by eVTOL developers, but the program cannot procure aircraft itself. So, it must find a major command that can take the next step and begin buying eVTOLs. The RFI appears to be a step in that direction.
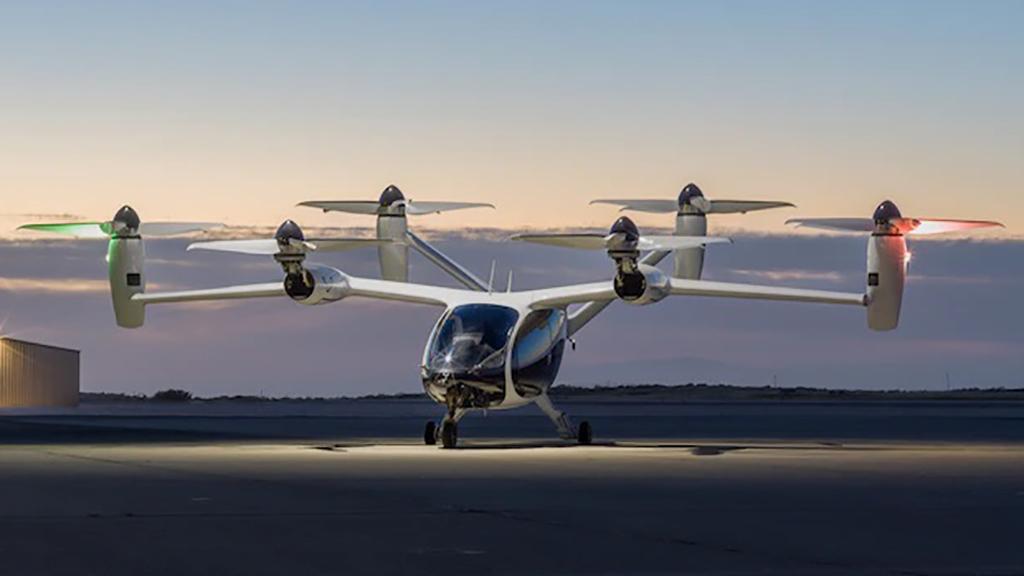
In an August report to Congress on progress with Agility Prime, the Air Force said it budgeted $86 million for the program in fiscal 2023. Of that, $74 million is for research, development, test and evaluation. The funding will continue risk-reduction ground and flight testing with multiple aircraft manufacturers.
Flight tests of prototype aircraft will be performed in realistic operating environments and scenarios to provide data to support fielding of the vehicles, the report said. Both Beta Technologies and Joby Aviation, working under Agility Prime contracts, have said they expect to demonstrate logistics missions on military bases in 2023 using their eVTOL aircraft.
An accomplishment of the Agility Prime program has been to obtain initial military flight release for several eVTOL prototypes well ahead of the vehicles achieving FAA type certification. This is key to enabling early use of the vehicles for military logistics missions before they are approved to enter commercial air taxi operations.
The RFI states that current aircraft maturity suggests eVTOL vehicles can perform the test range logistics support mission in the late 2023 time frame. This is supported by the Air Force’s ability to independently evaluate airworthiness risk, reduce residual risk to an acceptable level and provide well-defined flight authority within restricted airspace, the RFI states.
The test range mission is defined in the RFI as flying two personnel or up to 500 lb. of equipment a maximum distance of 75 nm, which is within the capability of eVTOLs such as Beta’s Alia and Joby’s S4. Aircraft would operate from one main site to up to three spoke locations, flying 5-30 hr. a month.
Successful execution of the range logistics missions would be a key milestone for moving the aircraft into the more demanding distinguished visitor (DV) transport mission. This is defined as transporting three to six passengers with up to 200 lb. of baggage each over a maximum desired range of 115 nm, which is at or beyond the limit of most current eVTOL capabilities.
The DV mission is analogous to the commercial air taxi model, the RFI notes. The Air Force operates DV missions at multiple locations around the world, and it wants to explore whether commercial operators are interested in aligning their initial service locations with these Air Force squadrons so the government can use their aircraft for DV missions when they are not being flown commercially.