
GE’s TBCC work builds on experience gained on earlier hypersonic designs such as the GE57.
Rotating detonation technology is a growing element of GE Aerospace’s accelerating push to play a key role in propulsion systems for future high-speed missiles, reusable hypersonic vehicles and other uncrewed applications.
Based on more than two decades of pressure-gain combustion research at its GE Research (formerly GE Global Research) facility in Niskayuna, New York, the company’s focus switched from pulse detonation engines to rotating detonation engines (RDE) in the 2010s as a result of work under the U.S. Air Force Research Laboratory’s Advanced Turbine Technologies for Affordable Mission-Capability pressure-gain propulsion program.
- RDE tested in turbine-based combined cycle demonstrator
- Short combustor outlined in high-speed patent
In June, GE revealed it was testing RDE technology within a turbine-based combined cycle (TBCC) propulsion system demonstrator for high-Mach applications as part of efforts supported by DARPA, AFRL and the Missile Defense Agency. GE is currently focused on testing the transition mode at high-supersonic speed from an RDE-equipped turbine to a dual-mode ramjet/scramjet, says Amy Gowder, CEO of GE Aerospace Military Systems.
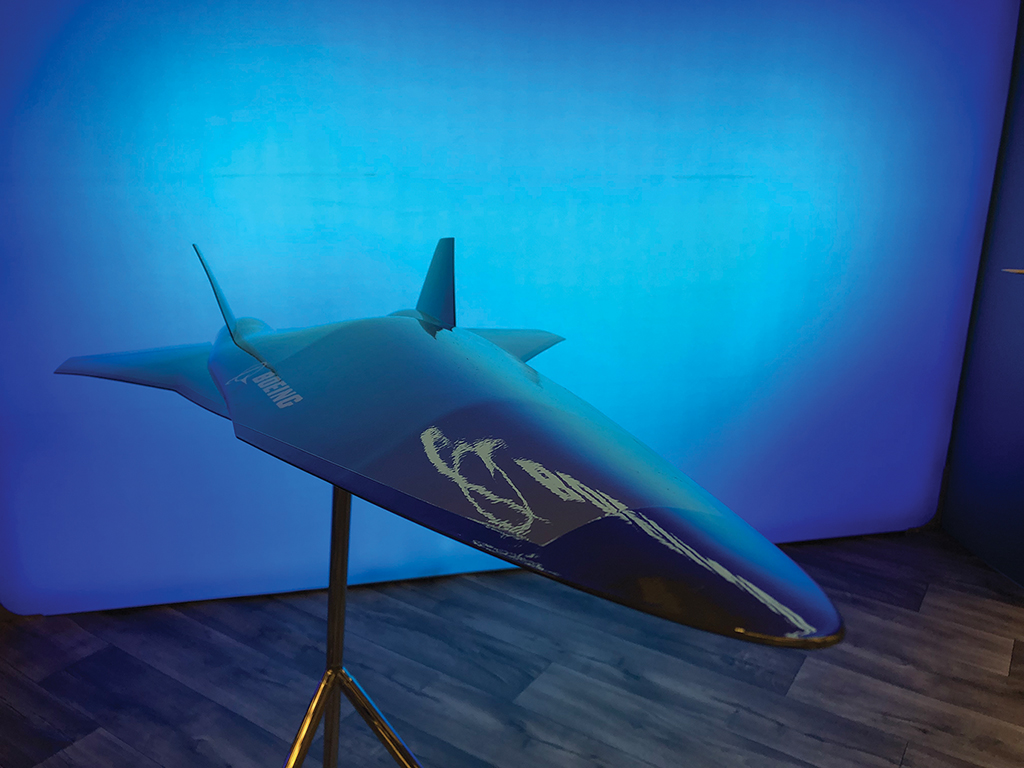
Other than acknowledging the advantage of the RDE’s compactness for reducing the overall length of the propulsion system, GE has offered few specifics about the device or its place within the TBCC configuration in general. Some clues may be gained, however, from a broad-ranging 2020 company patent for high-speed aircraft flight technologies that outlines, among other features, the use of an RDE in an afterburner.
Rather than using the RDE in place of the primary core combustor downstream of the high-pressure compressor, the GE concept outlines using the device to boost the pressure, temperature and speed of a secondary inlet airflow ducted into the afterburner via a bypass system. Other advanced features show a major focus on thermal management using an inlet pre-cooler, bypass intercoolers, porous flowpath liner walls to interact with cooling fluids, fuel-air heat exchangers and fluid-based cooling concepts for fan blades.
Some architectural elements of the hypersonic concept also appear to be based on the variable-cycle GE57 engine design, also known as the Revolutionary Turbine Accelerator (RTA), developed by the company in the early 2000s for a proposed Mach 4 TBCC ground demonstration. Intended as part of NASA’s Next-Generation Launch Technology Program at the time, the RTA was to demonstrate mode transition from an augmented turbofan to a ramjet, as well as the Mach 4 thrust level required to accelerate an X-vehicle—specifically the X-43B, a proposed follow-on to the subscale X-43A Waverider—to scramjet takeover speed.
Leveraging adaptive bypass injector features from GE’s YF120, a variable-cycle engine developed for the Advanced Tactical Fighter contest of the 1980-1990s, the key new feature of the J58 was the augmentor design that was dubbed the hyperburner. Although acting as a conventional afterburner to transition from takeoff to supersonic flight, the device was designed to kick in at higher Mach numbers and transition to a ramjet to accelerate the vehicle to Mach 4.
It is possible that—in combination with more advanced adaptive features developed over recent decades for the F136 and XA100, respectively—GE is therefore considering RDEs as part of an updated hyperburner design within a new TBCC demonstrator, as well as a future alternative to the conventional combustor at the heart of the high-pressure core.
GE’s acknowledgment of its TBCC progress comes as work continues under a 2021 NASA Hypersonic Technology Project (HTP) contract to support materials technology development for high-speed aircraft structures as well as air-breathing engine technologies.
The materials research involves the development of high-temperature-resistant, lightweight ceramic composites made from silicon carbide/silicon carbide (Sic/Sic) and carbon/silicon carbide (C/Sic). The Sic/Sic material is targeted at advanced turbines for high-speed environments, while the C/Sic is aimed primarily at thermally resistant structures for high-speed hypersonic and space access vehicles.
Under the same effort, GE has been assessing the viability of a modified F101 Mach 2-plus turbine engine to operate in a TBCC propulsion system for a hypersonic concept vehicle dubbed Aether, which has been developed under NASA’s HTP effort. The F101 is the only powerplant of its type with a fan bypass ratio of 2-to-1, which would allow most of the flow to bypass the core when it is throttled down to avoid exceeding the temperature limits of the core’s compressor and turbine.