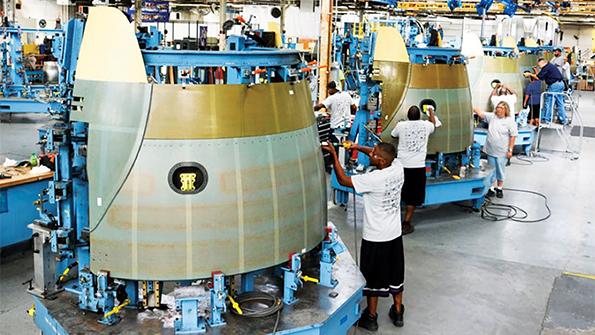
Ask the Editors: The Aviation Week Network invites our readers to submit questions to our editors and analysts. We’ll answer them, and if we can’t we’ll reach out to our wide network of experts for advice.
What will happen to the aerospace industry when 100,000 jobs are lost in the next two years?
Senior Business Editor Michael Bruno responds:
Workers will be fortunate if it is only 100,000 jobs lost. We know already that tens of thousands of layoffs—not furloughs but permanent workforce reductions—have been set in motion. More are expected in the coming months. From GE Aviation and TransDigm Group cutting 25% of their workforces to Boeing letting go 10% to Bombardier and Triumph Group cutting thousands of workers, the manufacturing side of aerospace is fighting to preserve capital, and cutting headcount is a common maneuver.
Separately, airlines may be in even worse shape; their employees are dreading the end of September, when federal aid stipulations are set to expire. You know things are bad when self-help memos propagate on LinkedIn that aim to help mainline pilots transition to other careers—an unthinkable prospect after years of hand-wringing about pilot shortages.
According to the Aerospace Industries Association, the aerospace and defense (A&D) industry supported roughly 2.5 million jobs in 2018, the last full year of data. That included 881,000 direct jobs and another 1.6 million in the supply chain, which often serves multiple industries. A&D accounted for 20% of U.S. manufacturing employment at the time, and the average wage and benefits of an A&D worker was $92,742. This was significantly higher than the average American worker’s salary of $49,389.
But 2018 could serve as the high-water mark. Long before the COVID-19 pandemic and even before the Boeing 737 MAX was grounded and production halted, industry was consolidating with increasing speed. Last fall saw Raytheon and United Technologies Corp. announce their merger, following that of L3 Technologies and Harris Corp. The supply chain experienced similar combinations after TransDigm bought Esterline Technologies. “Likely the most discussed trend, evidenced by both the quantity and deal value of mergers announced in 2019, is the race for scale throughout the supply chain,” mergers and acquisitions advisor Mesirow Financial said in March. “And 2019 more than doubled 2018’s announced deal value.”
But each deal brings further workforce reductions. Managers look to take cost out, starting with back-office functions and then deciding which business segments to cleave off as leaders focus on their core business portfolios. Although temporarily frozen because of the novel coronavirus, dealmaking is expected to pick up with a vengeance later this year as more distressed assets come onto the market, according to several consultants.
Worse yet for workers, industry is expected to adopt digitalization aggressively as it refashions itself post-pandemic. That means more robotics, automation and artificial intelligence to streamline operations and guarantee production and services while moving away from humans. This was already a trend as, ironically, industry struggled to hire enough workers in the late 2010s and feared a retirement wave of experienced baby boomers. “I think the new normal is going to be different, and I think automation is going to be a big factor,” says Hawk Carlisle, CEO and president of the National Defense Industrial Association.
Not every corner of A&D will be made redundant—niches such as aircraft maintenance, data scientists, digital-design engineers, classified work requiring security clearances and some upper-management levels could still struggle to fill their open positions. But as a whole, A&D could be home to fewer workers for years to come.