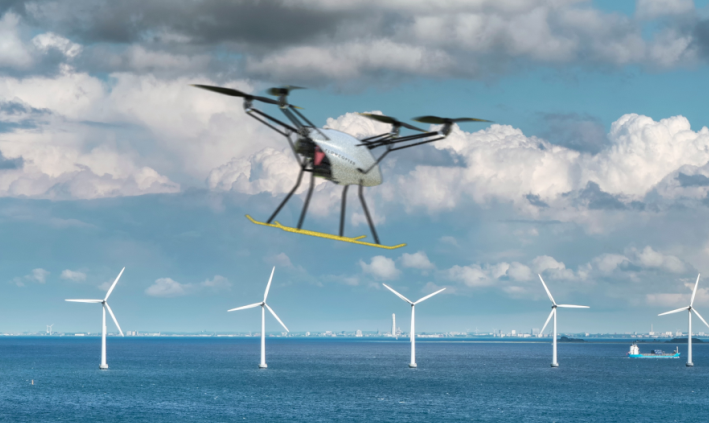
Flowcopter plans to use its patented hydraulic transmission system for heavy-lift drone applications.
The aerospace industry has coalesced around distributed electric propulsion as the key technological enabler for small drones and electric- vertical-takeoff-and-landing (eVTOL) aircraft, despite well-known limitations related to battery power, performance and weight.
Hydrogen has been proposed as an alternative, although that introduces further questions related to technological maturity, storage and distribution, among other technical challenges.
Recognizing those shortcomings, a group of engineers based in Scotland have formed a startup called Flowcopter that is aiming to bring to market a multicopter cargo UAV powered by a hybrid hydraulic transmission system, which the company’s Managing Director Peter McCurry explains offers greater efficiency, better power density and lower cost and weight compared to battery-electric systems.
“Hydraulics is thought of mainly as something of a sunset industry, or something you might find in your grandfather’s tractor,” McCurry tells the AAM Report. “But hydraulics also has very unique properties–low cost, robust, high-power density–which is why every single control surface you find on a commercial aircraft today is actuated by hydraulics: landing gear, flaps, ailerons, rudder—and pretty much all actuation surfaces.”
Despite its standard application in commercial aircraft, however, McCurry observes that two main shortcomings of hydraulic technology–poor control response and relatively low efficiency–have limited its use in aviation to date to controlling actuation surfaces, rather than power transmission.
Flowcopter gets around those challenges through a patented hydraulic pump system called the Digital Displacement Hydraulic Transmission, which the company says is significantly lighter, lower cost and more robust than an equivalent electric transmission.
“A digital displacement pump is a radial piston-style pump that’s actuated by a whole load of valves sitting around the outside of the pump in a fairly similar fashion to something like a common rail diesel engine from an ECU-actuated valve point of view,” McCurry explains.
“It’s got a very, very fast control response, and by the core architecture of enabling or disabling valves, you’ve got an extremely high efficiency and very, very low idle losses,” he adds. “Nobody’s ever thought about using hydraulic transmission in aerospace before because nobody ever had a fast enough and efficient enough control response to be able to drive the transmission properly.”
McCurry formerly worked as part of a team in Artemis Intelligent Power to develop the Digital Displacement Pump®. Artemis was acquired in early 2021 by Danish multinational Danfoss. Following the acquisition, Danfoss agreed to allow McCurry and some of his colleagues to acquire the intellectual property for the hydraulic pump system’s use in aerospace, paving the way for the creation of Flowcopter.
For the company’s first application, the Digital Displacement Hydraulic Transmission system is being used to power Flowcopter’s first product, an in-development heavy-lift quadcopter cargo drone that is being designed to carry up to around 300 kg (661 lb.) of payload for missions of around 100 km (62 mi.) out and back.
“There’s a huge gap in the market today between small battery-electric, possibly carrying five kilos or so, and a helicopter that might be carrying a ton-plus of cargo,” McCurry observes. “The minute you’ve got something in the 100, 200, 300-kilo range, there’s really nothing out there that’s cost-effective.”
Recognizing the novel nature of the hydraulic transmission system, McCurry said that Flowcopter is pursuing a lower-hurdle certification pathway by aiming its drone initially for operations in remote areas and developing nations, with crop spraying, tree planting, firefighting and malaria eradication identified as potential launch applications.
Flowcopter has a series of high-profile demonstrations planned over the next six months to spread awareness about its hydraulic propulsion system. As it prepares for those test flights, the company has also begun reaching out to potential launch customers and is preparing to raise additional funds from investors before year’s end.
Ultimately, McCurry believes that hydraulic propulsion will offer an opportunity to scale up to increasingly larger platforms, observing that efficiency gains will accelerate as size grows larger.
“Hydraulics is very, very scalable. As you scale up, it gets far more effective than electric systems,” McCurry says. “Digital displacement systems have been scaled up to megawatt-scale before. So, this is extremely scalable technology for the wider field of distributed aerospace propulsion.
“One of the big limitations that everyone has identified about distributed electric propulsion today is that it costs too much and weighs too much, and we have a solution to those problems,” he adds. “We’re proving it out at the 100-kw scale already on technology that is inherently scalable. So, we’re very keen to scale up for far bigger systems.”