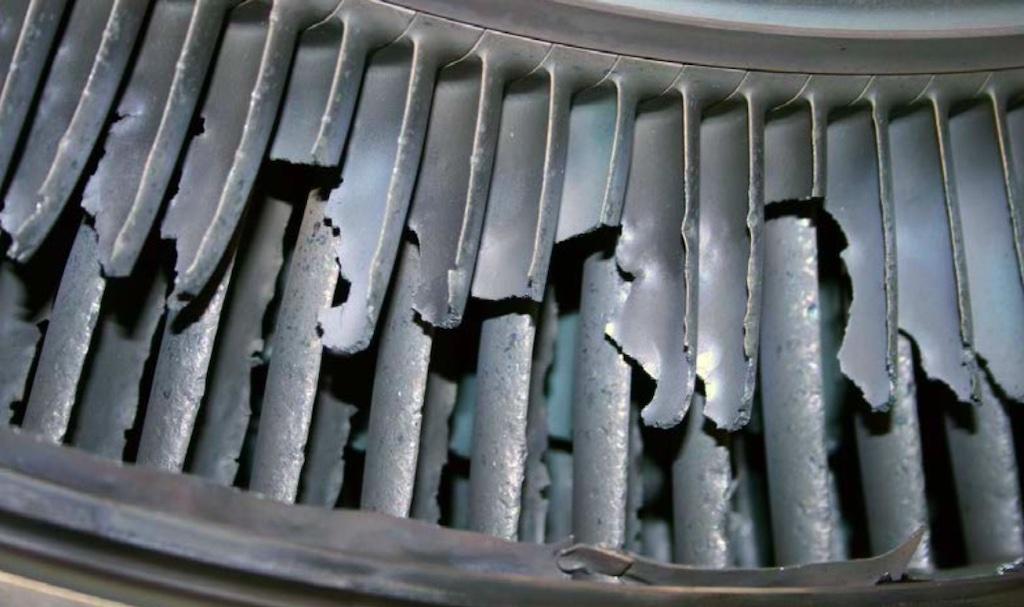
As turbine blades experience high temperatures they can begin to elongate and rub up against the engine’s case wall.
Modern turbine engines are reliable when properly maintained and operated within limits. Engine limits are boundaries which, if exceeded, will cause irreversible internal damage to an engine that can be manifested during a critical phase of flight.
This occurred to a 67-year-old pilot with 25,000 hr. total flying time operating a Hiller UH-12E light helicopter for Part 137 aerial application work near Susanville, California, on Oct. 13, 2019. The topography was steeply logged forest when the helicopter experienced two loud compressor stalls. The pilot decreased engine power and turned the helicopter downslope to allow the engine to recover. Compressor stalls grew continuous and the engine rpm decayed. The pilot attempted to recover engine speed by turning downhill, but this was unsuccessful. With no options left over the foreboding terrain, the pilot turned uphill moments before impact and applied collective pitch to cushion the landing. The main rotor blades struck terrain and the helicopter rolled onto its left side. The pilot sustained minor injuries.
The 250-C20B turboshaft engine was removed and shipped to a Rolls Royce facility for further examination. Disassembly of the engine revealed extensive thermal damage. This damage was consistent with an over temperature event during startup operation.
The NTSB determined the probable cause of the accident to be a partial loss of engine power due to multiple overtemperature events and a hot start event, which resulted in thermally damaged internal components of the engine. Contributing to the accident was the lack of suitable terrain on which to perform the forced landing.
Excessive Temperatures
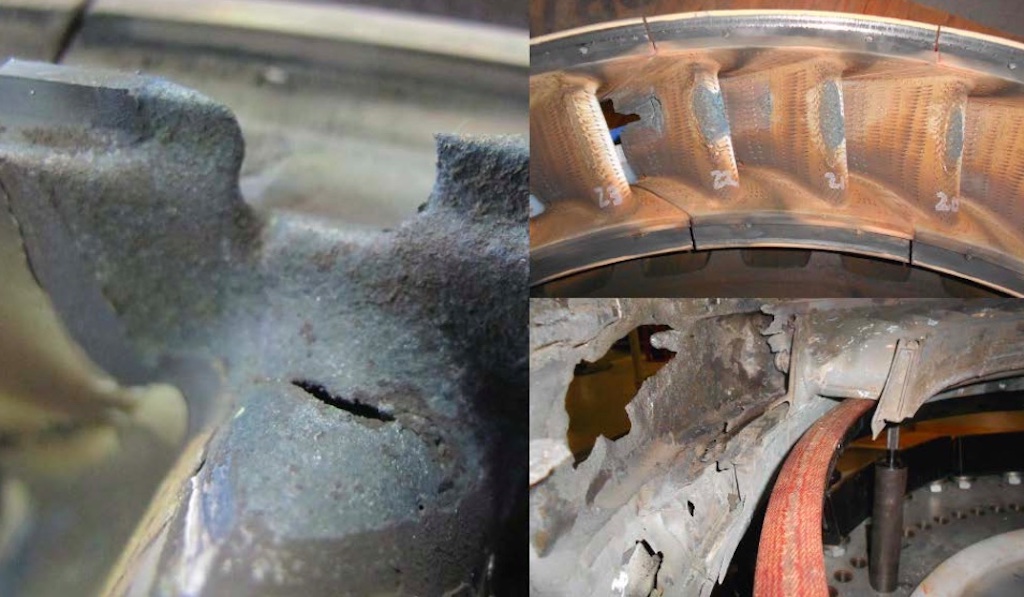
Exceeding an engine’s temperature limitations can cause significant damage, and as this accident aptly illustrated, multiple overtemperature instances caused widespread damage to critical components of the engine.
Hot temperatures during start can be caused by a weak battery with insufficient power to rotate the turbine at a sufficient speed to provide enough cooling air in the combustion section. It can also be caused by an early starter cut-out, fuel mis-scheduling or strong tailwinds.
An aircraft’s flight manual will stipulate the limitations for the engine during the start process as well as the procedures to follow if an engine’s temperature appears to rise rapidly during start. This is usually a combination of shutting off the fuel flow while continuing to motor the engine for a specific period of time to provide cooling air. Prudent flight crews will ask for a “start cart” to provide sufficient electrical power to spin their engine for start, and in some cases it may be necessary to have the aircraft repositioned into the wind to eliminate the adverse effects of a tailwind.
There is a long-term effect on an engine’s blades when exposed to higher-than-optimal temperatures. In order to achieve the best possible performance in terms of power production at the least fuel flow, the design and manufacture of high-performance turbine engines requires blade tip clearances between the rotors in the compressor and turbine sections against their respective boundary walls. However, as turbine blades experience high temperatures they can begin to elongate. This is termed “creep” by engineers.
If the blades elongate too much, they will begin to rub against the boundary walls. Blade rub will slow a turbine’s rotation rate, leading to a higher fuel flow and thus higher hot-section temperatures to create rated thrust. When blade rub grows worse it can cause high amplitude shaft vibrations and severe blade/seal wear, leading to catastrophic failure of the whole engine if left undetected.
The performance of a turbine engine also degrades over time due to wear. This occurs due to eroded compressor foils, worn seals, and the increased clearance between blade tips in the compressor and turbine sections due to erosion.
Engine trend monitoring is an important modern tool to help proactively detect the effects of blade rub. This will allow for maintenance or removal of an engine before the performance degrades too much.
There are several operational considerations to help lessen the chances of excessive temperatures on turbine engines. “Hot and high” takeoffs place a premium on engine thrust. For each 1 deg C there is an exhaust gas temperature (EGT) increase of approximately 3 deg C to produce the same takeoff thrust. Operators that have multiple aircraft in their fleet should try to avoid dispatching aircraft with performance-limited engines to airports with hot weather or high altitude runways.
It has often been a fuel-saving technique to taxi with a single engine, waiting until takeoff is imminent to start the remaining engine. Inevitably, a circumstance arises in which an aircraft is cleared for takeoff when the engine hasn’t been given sufficient time to warm up, and this is likely to result in an excessive engine temperature. It is important to give an engine sufficient time to warm up. Airbus recommends in their guidelines titled “Prevention of EGT Overlimit Events” to allow a warm-up time between 2-5 min.
The utilization of reduced takeoff thrust is commonly used by large fleet operators to reduce the long-term effects of high engine temperatures. A reduced thrust takeoff allows an engine to have an increased margin to the EGT redline. This proven method helps to extend engine life and save on maintenance costs.
In Part 2 of this article, we describe bleed air effects on engines.