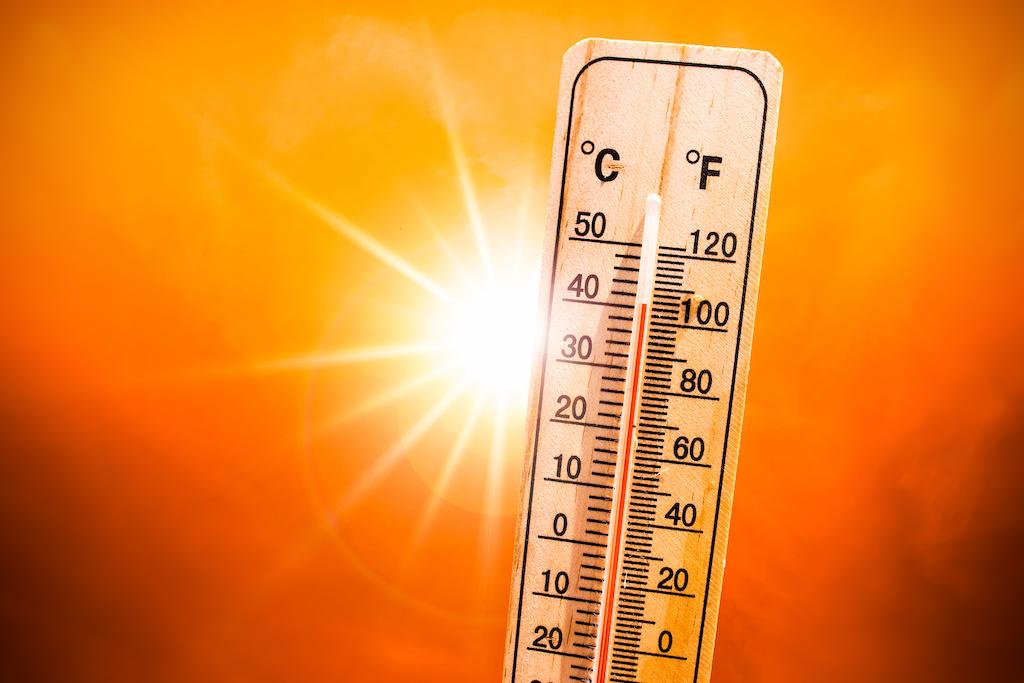
Tires are designed to withstand a wide range of operating conditions. Not only will your landing distances be longer when landing under “hot and high” conditions due to the higher true airspeed, the energy dissipated by the wheel assembly during hot-and-high conditions is much larger. If your normal Vref is 120 KIAS, but you are landing at Telluride Regional Airport (KTEX) on a warm, sunny day (85F), your actual true airspeed is 145 kt. The kinetic energy of the aircraft landing in KTEX is 46% higher than at sea level, thus the brakes and wheel assembly will heat up more. The centrifugal stress on the tire will also be 46% higher than at sea level. Heat plus higher stress increases the possibility of tread loss.
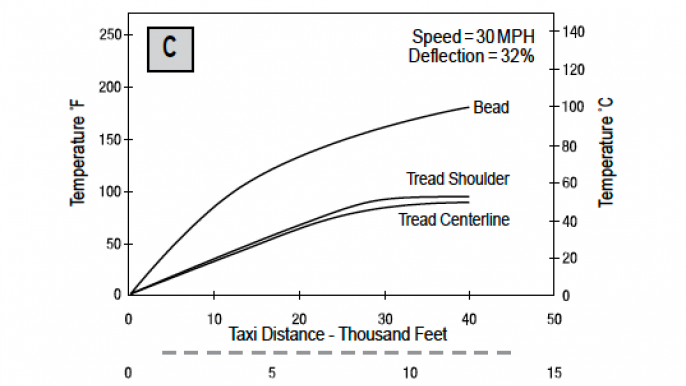
Additionally, since the landing distance is longer, the tires will rotate through many more rotations. Each rotation of a tire creates additional heat within the tire’s internal structure. The net effect is that the wheel assembly will be much hotter when the aircraft pulls into the ramp. These heat-soaked components will not cool off sufficiently while sitting on a hot aircraft ramp. When possible, utilize brake fans (if equipped) and release the parking brake once the aircraft has been chocked to assist with brake cooling.
If your wheel assemblies don’t have sufficient time to cool down, which is a problem particularly applicable during “quick turns,” the aircraft will begin its next taxi with warmer-than-normal brakes and tires. This can jeopardize the aircraft’s condition for the subsequent takeoff. The brakes may not be cool enough to provide sufficient brake energy to conduct a high-speed rejected takeoff. “Hot and high” conditions can also put an aircraft close to its maximum tire speed.
Conditions that will deteriorate the capabilities of your brakes and tires include a combination of the following:
* Dispatched at close to tire-speed-limit weight.
* High density altitude.
* Slower-than-normal rotation rate, or late rotation.
* Tailwinds.
* Long taxi distances.
* High-speed taxi.
* Heavy weights.
* Hot ambient conditions.
* Braking.
* Quick turnarounds.
Ramps Are Hotter Than ATIS
Airport ramps are a natural “heat island.” As solar radiation (i.e., sunlight) strikes the ramp, molecules in the concrete or asphalt absorb the radiation and vibrate more, in essence emitting their own radiation back into the atmosphere. The amount of solar radiation absorbed by the ramp depends on various factors, such as the angle of the sun with respect to the ramp (the noontime sun directly overhead bombards the ramp with the highest ratio of sunshine), clear-vs.-cloudy days, etc. Dark surfaces such as asphalt absorb more radiation than lighter colored surfaces, which tend to reflect some of the radiant energy. It takes a lot of incoming radiation to “heat up” concrete, but once it does reach a warm temperature, it tends to retain that heat for quite some time.
Heat radiating off the ramp can be considerable. How hot can ramp temperatures get? Much hotter than the temperature reported on the ATIS. On a hot August 2012 day at Lincoln Airport (KLNK), Nebraska, with the ATIS reporting 108F, mechanics showed me their recently acquired infrared temperature detector. Their “temperature shot” from the cement showed a temperature of 127F. The blacktop was even worse. It showed 143F.
A colleague who flies business jets for a living but prefers to race cars off-duty to fulfill his need for speed, posed an interesting question. He noted that the racing industry understands the vital importance of micro-tuning an engine for the exact air temperature conditions over the racetrack to optimize performance. They realize that the heat absorbed by pavement along the track would create much higher localized temperatures than the temperature recorded by an off-track thermometer. His insightful correlation pondered why we compute aircraft performance based on the ATIS temperature when in fact the runway environment is likely much hotter. I’ve tried looking through engineering studies that would answer this, but since radiative heat transfer isn’t within my specialty, I haven’t found a good answer. If/when I do find authoritative information on this, I will pass it along. With that said, this is a proactive “I am sorry” if this happens to open Pandora’s box.
Heated Surfaces Are Stressed Too
During extreme heat, pavement surfaces can crack due to thermal expansion. On an exceptionally hot day, the crack can expand and ultimately buckle the pavement if there is not enough room for expansion.
Be wary of the ability of excessively hot ramp and taxiway surfaces to bear the weight of your aircraft, especially near the edges of these surfaces. They lose their strength during abnormally hot temperatures and incidents have occurred in which aircraft tires have sunk into asphalt surfaces.
Increased Cooling Requirements
Perhaps you remember the first time you lowered the canopy on the T-37 in the middle of that hot July sun in Columbus, Mississippi, and thought, “I think my brains are cooking inside of this helmet.” Or maybe you were learning how to hover in that “greenhouse” canopy of the TH-55 at Fort Rucker, Alabama, and after the flight your green Nomex flight suit was completely drenched in sweat. Back then we were young, healthy and eager to show we were “can do,” and no one wanted to appear to be “the weak link” by complaining about “a bit of heat.”
For those who shrug and think that heat is a mere physiological discomfort in the aviation world that is “just part of the job”--don’t! Its first manifestation is on our cognitive functioning, with a subtle but significant increase in our error rates. The lack of recognition of heat as a significant detractor to human performance needs to be corrected.
Solar radiant heat can be significant in an aircraft cockpit. The large expanses of glass or Plexiglas produce a greenhouse effect. The temperatures in cockpits of aircraft parked on airfield ramps have been measured at 50F to 60F higher than those in hangars because of the radiation of solar heating through transparent surfaces. This radiation, in turn, heats the interior objects of the cockpit.
Keeping an aircraft’s interior tolerable on hot ramps can be difficult, if not impossible. This is even more problematic for aircraft not equipped with an APU, without shade protection from the sun, or without ground cooling equipment. When possible, utilize ground cooling equipment, ensure that window shades are closed during ground stops, and consider opening doors or latches that will allow heat to escape.
Mitigation
Pilots can take several steps to mitigate the effects of “hot and high” conditions. It’s no secret that summer afternoon departures from high elevation airports like Aspen are significantly challenged. Planning departures for the coolest time of the day (generally the morning) are wise. Just be aware that “down canyon” breezes in the morning caused by cooler air at higher altitudes may cause undesirable tailwind conditions at airports with “one way in, one way out” flight patterns. A good example of this daily diurnal wind pattern is at Sun Valley.
Use the runway that provides for the best aircraft performance. This may or may not coincide with the longest runway. Since the climb gradient is often a more limiting parameter, carefully consider the runway with the shallowest climb gradient.
The maximum takeoff weight will be limited to meet runway and/or climb gradient requirements. It is often necessary to download the fuel in order to meet climb gradient requirements out of airports like Aspen, especially during summer temperatures. Many of you have probably flown out of Aspen with sufficient fuel to proceed to an airport along the Colorado Front Range, whereupon enough fuel was uploaded so that the flight could proceed to the East Coast.
A subscription to one of the “airport analysis” services that provide specific engine-out procedures to avoid obstacles as well as an easier-to-understand format for determining the maximum weight to assure compliance with all of the takeoff and climb performance parameters is a worthy investment. These custom-designed engine-out flight paths assure that you can take off at the maximum possible weight much heavier than if you were attempting to comply with the normal IFR departure procedure.
Comments
I would imagine that, on a calm day, the temperature of the air immediately above an asphalt runway surface would be significantly higher than the "ambient" temperature reported by the ATIS. Because of this, an aircraft would be rotating and lifting off at a density altitude greater than that normally used in takeoff performance calculations. Of course, almost immediately after liftoff, the aircraft would encounter temperatures cited in the ATIS, so maybe these theoretical temperatures would not have a significant effect on takeoff performance. I believe the temperature difference would be somewhat mitigated by a decent crosswind component.