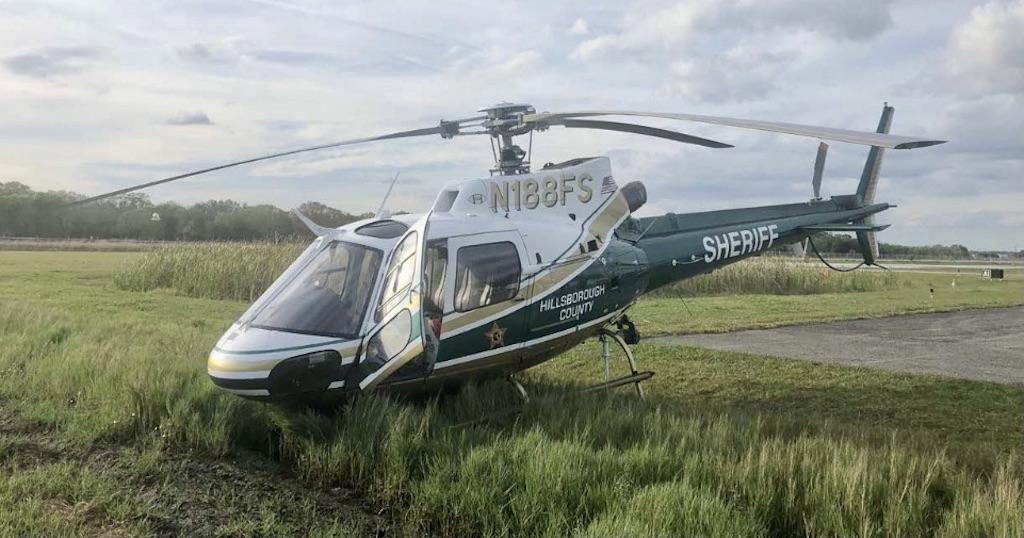
An instructor inadvertently moved the throttle lever from idle aft toward the 'off' position, which resulted in a total loss of engine power. The instructor took the controls, conducted a power-off autorotation, and landed the helicopter on the taxiway. It skidded about 180 ft, departed the taxiway onto adjacent grass, and came to rest in a drainage ditch.
How do we provide sufficient training to pilots to make certain they are proficient in the complex emergency procedures in a rotorcraft under a variety of real-world conditions?
Even though modern, properly maintained powerplants are reliable, a helicopter pilot must always be prepared to properly execute an autorotation. The U.S. Joint Helicopter Safety Analysis Team (JHSAT) “Compendium Report” (2000, 2001 and 2006) determined that autorotations, both actual emergencies and during training, occurred in 32% of the 523 accidents during that three-year period.
An autorotation is a complex perceptual motor skill. Unrecoverable consequences can quickly occur if the pilot’s inputs are incorrect, insufficient, excessive, or poorly timed. The only way to remain proficient is to practice this critical maneuver frequently. Ironically, the safety margins are so thin that sometimes the practice maneuver terminates in an accident. The JHSAT’s report noted that 68 of the 523 accidents, or 13%, occurred during autorotation training.
There is no debate within the industry on the importance and necessity of autorotation training. Industry and government working groups have issued numerous advisories to correct some of the common deficiencies. These include recommendations on safety briefings, throttle usage, prudent selection of practice areas, and the necessity to rapidly place the rotor tip-path-plane into a proper orientation for the autorotation.
Have these recommendations been effective? Perhaps. The following is a review of autorotation accident data from a recent four-year period to provide a comparison against trends from 15 years ago.
A total of 73 helicopter accident investigation final reports involving an autorotation were reviewed in the NTSB’s accident database; they occurred from the 2019 through 2022. Seven accidents resulted in 11 fatal injuries. All other accidents involved non-fatal injuries. Thirty of the 73 occurred during autorotation training.
An actual loss of power occurred in eight of the 30 autorotation training accidents. Thirty-eight of the 73 accidents involved turbine-powered helicopters. The rest occurred in piston-powered helicopters. Now let’s dig deeper into the data for important trends.
Insufficient Speed-Altitude Combination
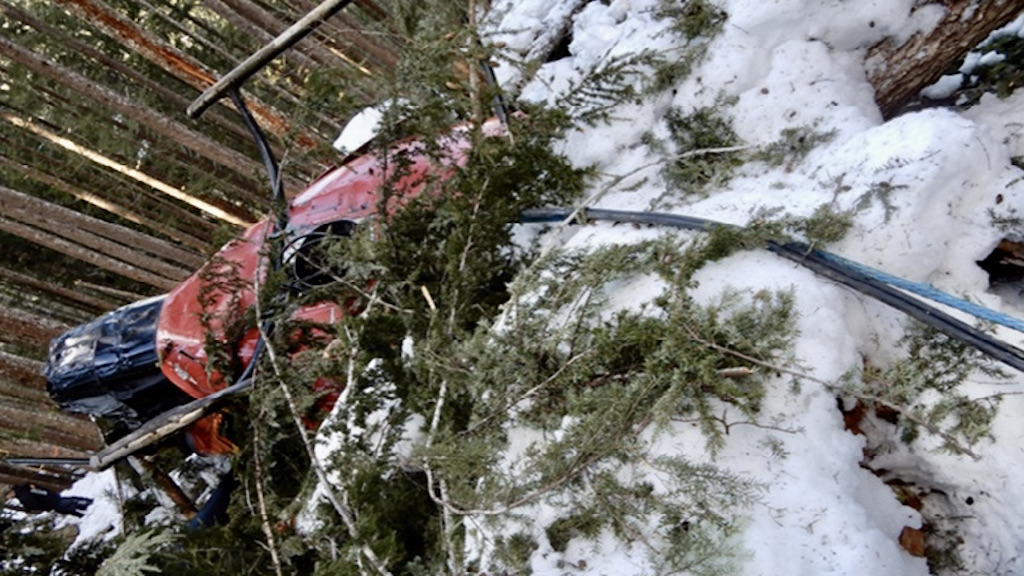
Many important helicopter missions are conducted relatively close to the ground and at slow speeds. This is a necessity for the aerial firefighting pilot trying to drop a bucket of water precisely on a smoldering snag, as well as for the pilot hovering mere inches from high-voltage cables as a technician conducts electrical line maintenance. Unfortunately, 22 of the accidents reviewed for this report occurred at an insufficient altitude to adequately establish a steady state autorotation to avoid impact with terrain.
This happened to the pilot of a Bell UH-1B who was conducting helilogging operations on March 8, 2019, near Forks, Washington. Shortly after his first external-load lift of the day, company employees heard the pilot call mayday. The helicopter was found inverted in the designated logging area with the cargo line still attached along with a log. The pilot was fatally injured.
According to the NTSB accident report, the helicopter operator had not kept accurate documentation of engine cycles. The helicopter’s electronic cycle counter revealed that the sealing disk had exceeded its published life limit of 6,900 cycles. The cycle counter had recorded 12,023 cycles.
The NTSB determined the probable cause to be the total loss of engine power due to the failure of the gas generator sealing disk, a result of the operator’s exceedance of the sealing disk’s life limits at too low an altitude for the pilot to accomplish a successful autorotation that resulted in the collision with terrain.
There are combinations of initial altitudes and airspeeds from which a safe autorotational landing will be extremely difficult to perform if an engine fails during this precarious phase of flight. The boundaries of these combinations define the height-velocity diagram. The H-V diagram depicts two areas to be avoided: the low-airspeed/high-hover altitude (low flight altitude) region and the high-airspeed/low-altitude region. From these combinations it is almost impossible to demonstrate safe autorotative landings at a vertical touchdown speed within the design limits of the landing gear.
Many helicopter missions require extensive periods of time spent precariously close to the margins of the H-V diagram, so from a practical standpoint it isn’t realistic to tell pilots to always avoid flight within the shaded areas on the H-V diagram.
In addition, some helicopter missions are conducted in an airborne environment that is hazardous to turbine engine operations. Five prominent parameters in the wildfire airborne environment place abnormal stresses on turbine engines. First, while the “average” air temperature around wildfire incidents tends to be excessively hot, localized plumes of super-heated air rise from the flames. Additionally, radiant heat from the flames elevates air temperatures near the flame front, far above the “ambient” temperatures.
Secondly, the air from burning wildland fuel is a complex mixture of gases and aerosols. Thirdly, wildfires also emit large amounts of fine and course particulate matter (PM). Fourth, the air adjacent to the flame front is turbulent. Turbulent air flow through the engine inlet increases the chances of compressor stall and/or engine surges. Fifth, common flight maneuvers necessary for firefighting near the flame front increase the chances of hot gas ingestion into the engine inlet. All five of these conditions exist simultaneously and directly compromise the safety margins of turbine engines.
The historical record illustrates razor-thin safety margins in this environment. A Flight Safety Foundation study of helicopter accidents involved in aerial firefighting examined U.S. accident reports from 1974-98 involving helicopters engaged in aerial firefighting.
Thirty-four of the 97 accidents were caused by powerplant malfunctions and failures. Thirty-one of the 34 accidents resulted in severe injuries or worse to the occupants due in combination to an engine malfunction near the margins of the H-V envelope as well as the inhospitable terrain underneath the aircraft.
Observing operating limits, following a manufacturer’s maintenance schedule, utilizing the manufacturer’s guidelines for normal and all-weather operations, and engine trend monitoring are important elements to maximizing engine reliability, all of which are vital when the consequences of an engine failure don’t allow a safe autorotative landing.
In Part 2 of this article, we consider autorotational flares and hard landings.