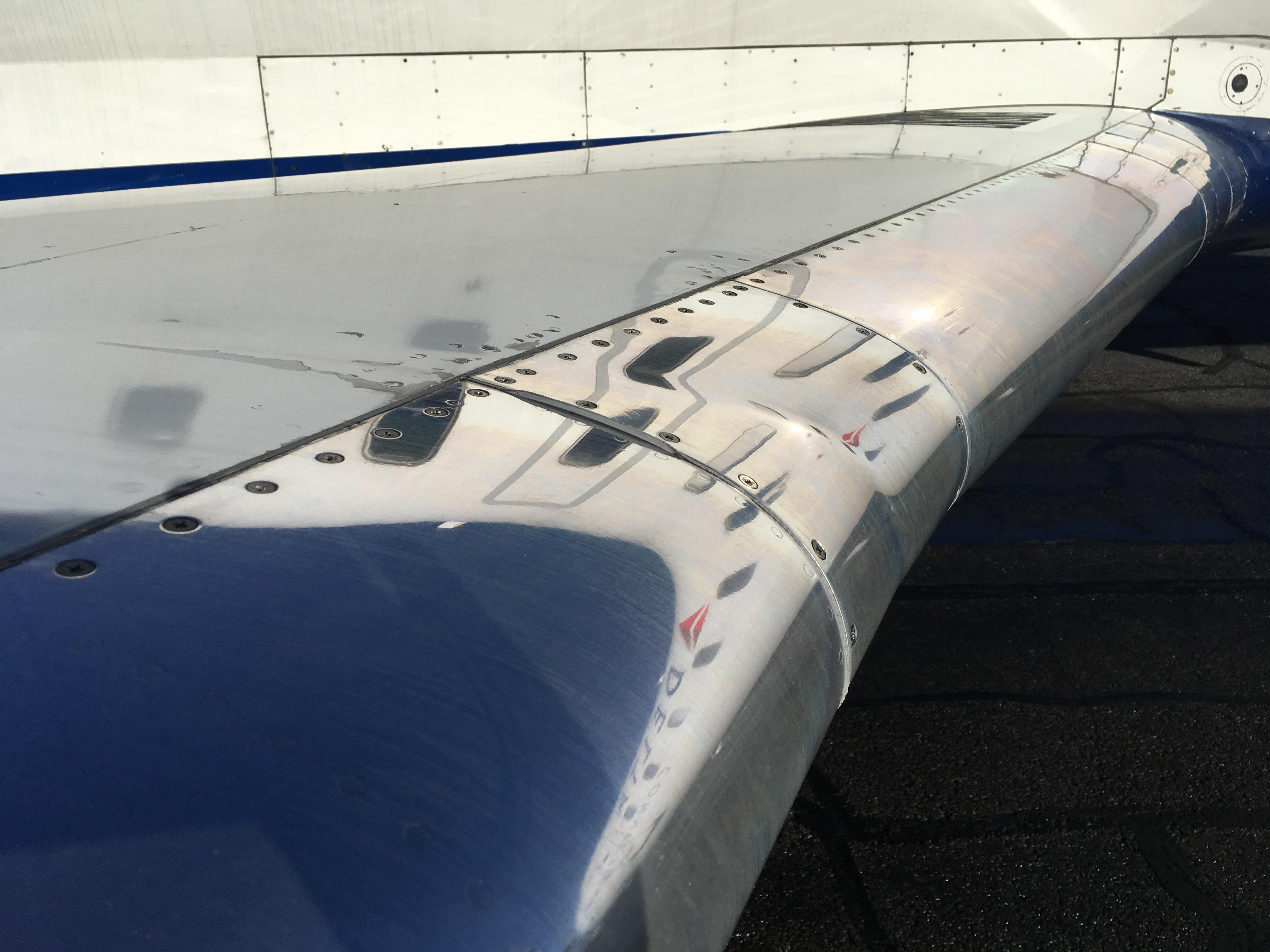
From our very first flight lessons we were taught to check for “full and free correct movement” of flight controls. Every preflight, whether it is for a normal flight or a post-maintenance test flight, must ensure that the flight controls exhibit full and free correct movement without any possibility of binding. This isn’t rocket science, and yet the NTSB files contain events in which this simple concept wasn’t followed.
A Messerschmitt-Bolkow-Blohm BO 105LS A-3 was conducting a maintenance test flight on April 13, 2006, in Green Bay, Wisconsin. Following takeoff, the helicopter began spinning around its vertical axis to a height of approximately 200-300 ft. and descended without directional control, impacting terrain. The rotorcraft was substantially damaged and one fatality resulted. The copilot's anti-torque control pedals were found in their full forward position with a safety wire installation that was contrary to specifications cited in the field approval for the pedal cover. The NTSB determined the probable cause was the pilot's inadequate preflight check of the flight controls prior to takeoff and the directional control not possible by the pilot. Additional causes were the improper installation of the anti-torque pedal cover by company personnel, which blocked the flight control system.
Any possible restriction to a flight control’s full and free correct movement must be corrected prior to flight. A pilot and a mechanic were flying a second maintenance flight check of a Eurocopter AS 350-B2 on July 1, 2005, at Scottsdale, Arizona, to check the rotor tracking. During a previous maintenance test flight they encountered a restriction in the collective’s movement when the collective down lock inadvertently engaged. They entered a descent at approximately 1,200 ft. AGL and prepared to level off at approximately 700 ft. AGL. When the pilot tried to pull up on the collective, it would not move and was observed to be latched by the collective down lock. They tried to unlatch the collective from the down lock but did not have enough time before the pilot had to flare the helicopter for landing. With the collective stuck in flat pitch, they landed hard and with forward speed. The flight crew evacuated the AS 350 once it came to rest. An ensuing post-accident fire destroyed the helicopter.
The investigation noted that a new avionics control panel had been installed and the collective down lock, which is secured to the panel, was adjusted prior to the flight. This was the second known accident where the collective lock had inadvertently engaged in flight with this particular aftermarket avionics panel installed. The NTSB determined the probable cause was inadvertent inflight engagement of the collective down lock, which resulted in an uncontrolled descent and ground impact. The collective down-lock engagement was caused by the improper installation and/or adjustment of the collective locking system, which reduced the clearance between the locking plate and the collective control.
Know ‘Normal’ Movement
The NTSB Safety Alert titled “Pilots: Perform Advanced Preflight After Maintenance” recommends that pilots become familiar with the normal movement of the aircraft’s flight controls and trim surfaces before it undergoes maintenance. It is easier to recognize abnormal movement if you already are familiar with what normal looks like. I would add “feel” and “hear” to this statement. During a preflight on a cable-and-pulley flight control system, as you move the flight controls and trim surfaces to their full deflection, not only are you checking for the correct direction of movement (on larger aircraft it will be necessary to have someone outside the aircraft directly communicating with you), but you should feel for any restriction as well as carefully listen for any hint that the control cables are possibly rubbing against other surfaces or falling off pulleys.
This saved my bacon during a preflight for a maintenance test flight when the yoke didn’t seem to move normally. The amount of force required to move it seemed slightly abnormal. There was some small but definite binding in the movement. Additionally, I could hear a faint but abnormal “rubbing” noise as I moved the yoke. The maintenance controller uttered a long sigh when I described this over the phone. Troubleshooting required ripping up the flooring to examine the flight control cables. A few days later I received feedback that the cables had become displaced from a pulley and were actually moving in between the pulley and its mounting bracket. Not only were the cables becoming frayed, but it was possible that they could have become completely jammed.
When a cable-and-pulley flight control is reinstalled it is necessary to properly tension the control cables. During the 10 years in which I was a non-routine flight operations captain at a fractional operator, I performed many post-maintenance flights checking the flight controls. It wasn’t until liftoff during one of those flights that we discovered the difference in flight control movement when the cables didn’t meet the required tension. The co-captain rotated for takeoff and the aircraft uncharacteristically begun a significant roll to the right. The co-captain was using every bit of his upper body strength to try keeping the aircraft upright. I distinctly remember his strained words, “Paaaaaaat, I caaaan baaaarely hold it.” The two of us had a hard time keeping the wings level and I had just enough mental reserve to quickly tell ATC that we had an emergency with a flight control problem and needed some airspace to work out the problem and formulate a recovery plan. ATC was great. It was a handful, no pun intended, to fly an aircraft that wasn’t handling in a normal manner. We landed, with considerable difficulty but without further incident, and pulled into the company ramp thanking ATC and the fire department for its escort. During the post-flight I re-checked the ailerons to see if I could feel any difference in the amount of force to manually deflect them up and down. I was not able to discern any noticeable difference from “normal.” Nor was it possible during our post-flight investigation to feel a difference when moving the yoke. The difference became noticeable only when there was an aerodynamic load on the flight control.
Flight Control ‘Free Play’
A destructive form of fatigue called limit cycle oscillation (LCO) is caused by excessive free play within the flight control surfaces and associated components. This condition generally becomes worse at higher speeds and altitudes. An example of this affected some Hawker 800XP and 850XP aircraft that experienced wing/aileron oscillations at altitudes above 33,000 ft. and speeds over Mach 0.73. When the speed was reduced and the airplane was at an altitude below 30,000 ft., the oscillations ceased. Investigation of the incidents revealed missing aileron bushings, low cable tensions and improperly installed brackets. If the aileron system, including cable tension, is not properly maintained, wing oscillations could develop into divergent flutter, thereby causing severe damage to the structure. When corrective maintenance brought the aircraft into compliance with the type design configuration, the oscillations did not recur.
The FAA issued Special Airworthiness Information Bulletin NM-14-05, dated Nov. 27, 2013, recommending a one-time maintenance check to verify all the bushings in the aileron and aileron tab assemblies are correctly installed, that the free play is within limits, and to ensure that the hinge brackets are properly installed and the cable tensions correct.
This type of oversight mistake has happened to other business aircraft as well. On March 19, 2004, the flight crew of a BAe 1000 had to declare an emergency to return to Palm Beach International Airport (KPBI) due to a control problem after experiencing severe longitudinal oscillations. The yoke oscillated left and right rapidly and the wings were flexing 4-6 in. Following inspection by a technician, a maintenance check flight was conducted from KPBI to Tampa International Airport (KTPA) on March 21, 2004, during which similar symptoms were exhibited. Re-inspection of the aircraft found that three aileron hinge bushings had not been installed at the previous maintenance.
During a preflight of cable-driven flight controls, pilots should check the free play by gently moving the flight control. The exact amount of free play (i.e., the amount you can jiggle the flight control without restriction) should be stipulated in the aircraft maintenance manual. If excessive free play is found during a preflight, the proper action is to note the discrepancy in the aircraft logbook and not fly the aircraft until the condition is corrected by maintenance technicians.
A pilot conducting a post-maintenance test flight should be attentive to the maintenance corrections made as well as know that subtle vibrations at relatively low altitudes will likely be exacerbated at high altitudes where true airspeeds increase. Clearly some knowledge of aeroelasticity is necessary for flight crews who conduct post-maintenance test flights, especially of flight control systems. Troubleshooting vibrations will often require changes of airspeed, changes of throttles and configuration, and possibly changes of altitude to get a trend. It will be important to observe whether the vibrations were high frequency or low frequency. For example, the flight crew of a business aircraft experienced divergent flutter at approximately 2,000-3,000 ft. accelerating through 170 KIAS. The flight crew decreased to 150 KIAS, whereupon the flutter went away. They declared an emergency and landed uneventfully. They subsequently discovered the port side trim disconnected from the control arm that was recently out of maintenance at the FBO (ASRS 700868, June 2006).