Structural Integrity Factors Can Cause Premature Failure, Part 3
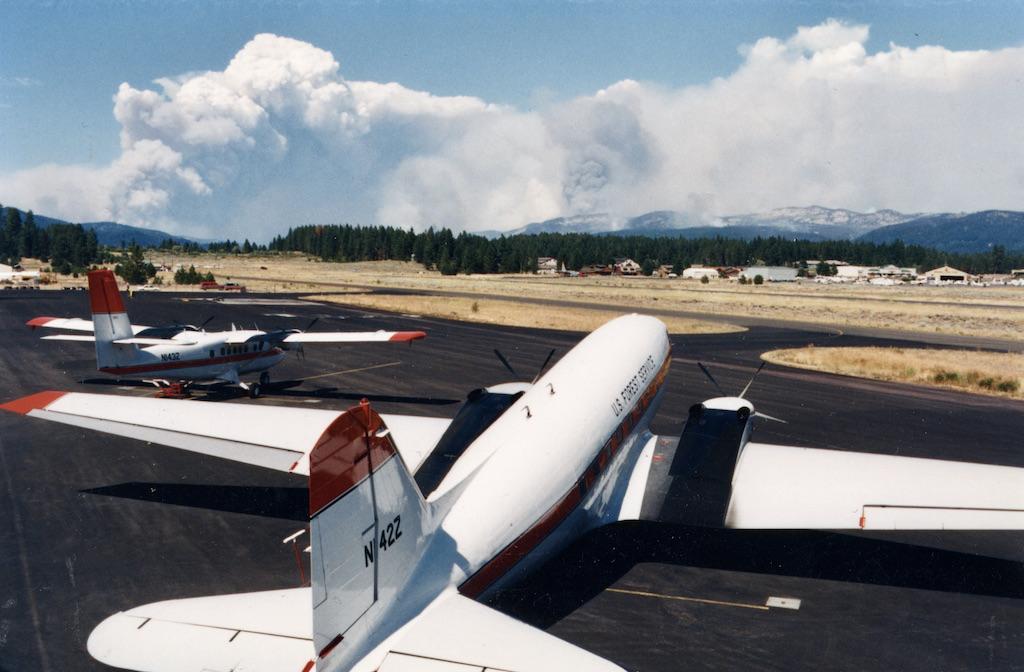
The turbulent air above a wildfire is punishing to aircraft structures. The excessive and frequent loads place an inordinate number of loading cycles on an aircraft, leading to accelerated crack growth and possible structural failure.
The T-34/A-45 wing failures we discussed earlier are not isolated examples of the structural compromises caused by asymmetric loading, nor by usage outside of an aircraft’s original loading spectrum.
Flying in the aerial firefighting environment is full of sharp-edged up-and-down gusts from the fire plumes. It is a brutal environment that induces multitudes of cyclic loads on an airframe in just one pass over a fire location. The structural design characteristics of aircraft have never included being exposed to such a punishing environment.
The FAA’s Office of Aviation Research and Development contracted with Celeris Aerospace Canada (which ceased operations in 2021) to examine inflight accelerometer data from aerial firefighting aircraft in the aftermath of two catastrophic wing failures of air tankers. The lengthy engineering study published in October 2005 examined vertical acceleration flight data gathered from air tankers and lead planes operating in the low-altitude firefighting mission.
The Beechcraft Be-58P Baron was commonly used as a lead plane aircraft by the U.S. Forest Service during that time. The mission of the lead plane was complex and much of it was performed during low-altitude maneuvering close to wildfires.
In addition to evaluating the overall fire environment, the lead-plane pilot must also evaluate the surrounding terrain to determine the best approach and exit routes from which the heavily-laden and less-maneuverable air tankers can drop retardant. Lead planes often precede an air tanker into the drop zone to indicate exactly where a drop should be made. After the retardant drop, it is common for a lead-plane pilot to subsequently evaluate the accuracy and effectiveness of each drop.
The training to become a fully qualified lead-plane pilot often took several seasons, especially for pilots who had limited backgrounds and experience in wildfire suppression. I distinctly recall hearing the instructors ask friends who were in the training process to become lead-plane pilots, saying: “Have you got your spurs on today? We’re going to teach you to fly like a cowboy! You’d better bring a sick sack because we’re going to be yanking and banking.”
Onboard accelerometers revealed substantial negative effects on the lead-plane’s structure when lead-plane pilots regularly banked 90 deg. and reversed their previous direction to observe the placement and effectiveness of each air tanker drop. The data discovered numerous exceedances of the airplane maximum-G operating limitations due to pilot-commanded maneuvering. Furthermore, maintenance reports indicated wing-skin cracking, pressure bulkhead cracking and cracking in both the vertical and horizontal stabilizers. Structural specialists were concerned that these service difficulty reports were merely “the tip of the iceberg.”
Even though the original FAA Approved Airplane Flight Manual specified a structural life limit of 10,000 hr. time-in-service (TIS), the FAA subsequently determined that if flight operations continued beyond 4,500 hr. TIS, then the cumulative fatigue damage on these airplanes would reach a point at which catastrophic fatigue cracking might occur. Failure of the airframe (wing, fuselage, empennage or associated structure) could lead to a loss of control of the airplane. Fortunately, an in-depth engineering analysis by structural integrity specialists found these deficiencies proactively prior to a catastrophic failure.
Structural Integrity Is Complex
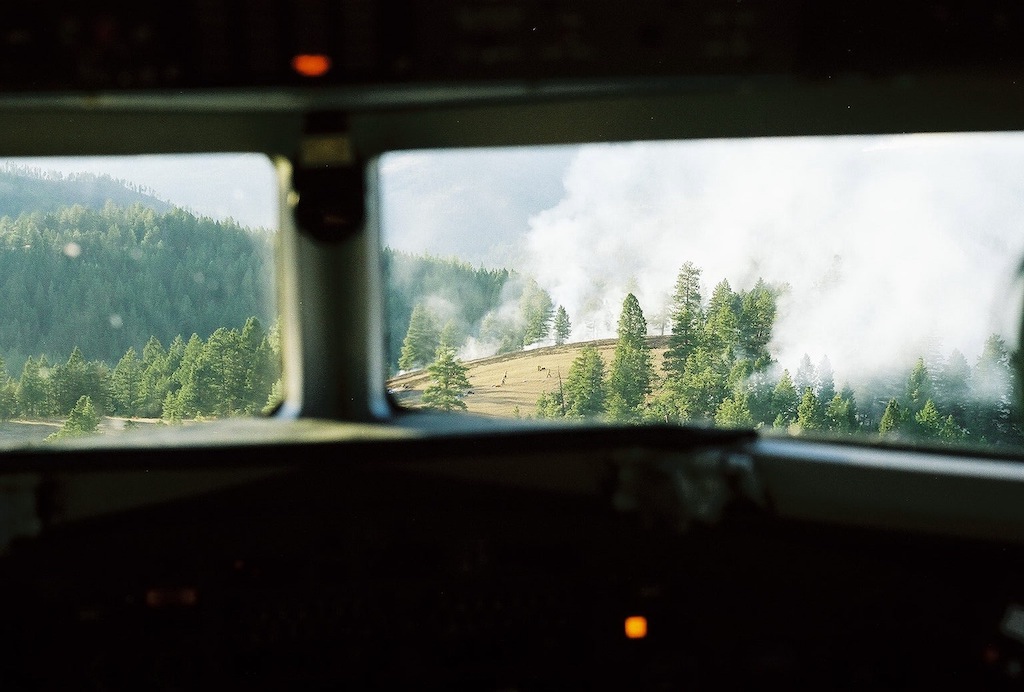
The structural integrity of an aircraft is a complex issue. An entire specialty within advanced engineering is devoted to this topic. These are specialties that fall far outside of the normal scope of knowledge for aviators.
The examples in this article are not unique incidents. There are a troubling number of cases in which upset recovery programs have designed recovery techniques without an in-depth understanding of aircraft structural limitations and the flight dynamics of transport airplanes. This issue was also woefully misunderstood by a multitude of airline training instructors, safety inspectors and auditors who were involved in the design and application of the advanced maneuvers programs.
All of the examples involved pilot instructors who had extensive flight experience with advanced ratings. In fact, many of these operators had given “safety seminars” at industry gatherings. And yet, the subsequent investigations determined that these aircraft were operated in a manner in which the control inputs directly compromised the aircraft’s structural integrity.
During testimony before the U.S. House Transportation and Infrastructure Committee on FAA reauthorization, NTSB Chair Jennifer Homendy in February expressed particular concern about the safety of various passenger-carrying operations that are conducted under Part 91. Her examples included combat training/extreme aerobatic experience flights.
Homendy pointed out that these operations are not held to the same maintenance, airworthiness and operational standards as air carrier, commuter and on-demand operations. People who pay to participate in these activities may not be aware that the operator is held to less stringent safety requirements than other commercial aircraft operations.
NTSB recommendations include the mandatory implementation of safety management systems (SMS) at these operations. A proper SMS would highlight the special attention required for assuring structural integrity by true subject-matter experts in this field. But until such expertise is required, passengers and trainees are left to the woefully inadequate warning of “Buyer Beware.”
Structural Integrity Factors Can Cause Premature Failure, Part 1: https://aviationweek.com/business-aviation/safety-ops-regulation/struct…
Structural Integrity Factors Can Cause Premature Failure, Part 2: https://aviationweek.com/business-aviation/safety-ops-regulation/struct…