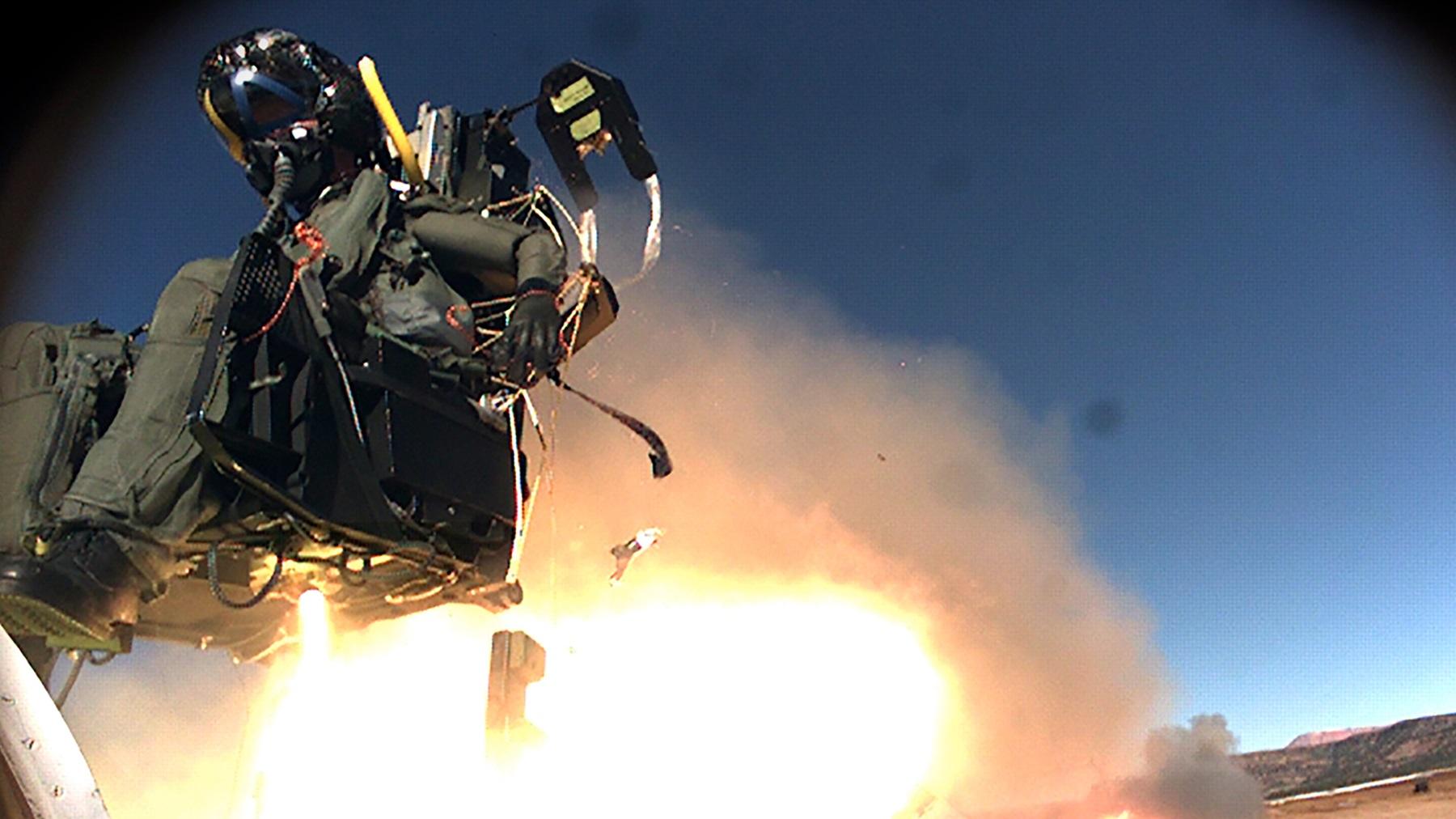
A newly developed ACES 5 ejection seat for the T-7A has been sled-tested to validate its new safety features.
A convergence of new aircraft programs and retrofit plans are expected to drive a rare boom in ejection seat production in a few years, and deliveries of U.S.-built seats are set to increase sharply over current levels.
The surge also stems from significant new advances in the carefully choreographed set of technologies that propel a human out and away from a doomed combat aircraft as safely as possible—even as the size range for pilots significantly expands on both ends of the weight spectrum.
- NGES, T-7 programs spur growth
- B-21, NGAD opportunities also lie ahead
In advance of the surge, the sole U.S. ejection seat supplier—RTX-owned Collins Aerospace—has formally launched an industrial expansion in Colorado Springs and, for the first time, is building a separate facility from the company’s airline seat manufacturing plant.
“Our rate is roughly 100 seats per year, and in the future, we are looking at a fairly high ramp-up of up to five, six or eight times that in the next six to seven years,” says Chris Alberts, operations site lead for ejection seating.
The preparations come after a decades-long period of declining production capacity for Collins’ ejection seats.
Following Lockheed Martin’s selection of the UK’s Martin-Baker US16 seat, U.S. production dwindled to mainly supporting the Advanced Concept Ejection Seat (ACES) II installed on the Fairchild Republic A-10, Boeing F-15, Lockheed F-16, Lockheed F-22, Rockwell B-1 and Northrop Grumman B-2.
In 2016, the U.S. Air Force took the first step to revitalize domestic ejection seat manufacturing. The Air Force Program Executive Office for Agile Combat Support decided to adopt a nondevelopmental system for the Next Generation Ejection Seat (NGES) program. The decision guaranteed that a series of upgrades to the ACES II seat previously funded by the B-2 program to address long-standing safety concerns would be selected for the NGES contract.
Although Martin-Baker publicly lobbied for a competition, the Air Force bypassed a competitive bidding process. A new version of the ACES ejection seat family offered several key new technologies, including pop-up pitot tubes to measure the seat’s speed and altitude after an ejection, passive head and neck restraints as well as arm and leg restraint systems.
Three years later, the Air Force formally selected the redesignated ACES 5 seat as the sole source supplier for the NGES requirement, which would replace the ACES II inventory across the Air Force. Collins received a contract worth as much as $700 million in 2020 to deliver up to 3,018 ejection seats through 2030 to retrofit the A-10, F-15, F-16, F-22, B-1 and B-2 fleets.
Hundreds of additional ACES 5 seats will be ordered for the Boeing T-7A fleet, which is scheduled to enter service in 2027. The new U.S.-built seat also becomes a contender for new military aircraft, such as the Northrop B-21 program, which has not yet announced an ejection seat supplier. During a tour of the Collins factory, a shroud covered a pair of ejection seats being prepared for delivery to an undisclosed customer. Collins officials said the seats are designated as P-102, denoting a proprietary seat for a customer whose identity is sealed by a nondisclosure agreement.
To prepare for the ramp-up, the company has expanded manufacturing space at its new Colorado Springs facility, the final phase of which was marked by an Aug. 10 ribbon-cutting ceremony.
Production is currently underway on eight seat variants of the company’s two main seat models— the ACES II and ACES 5. The company also continues to support the legacy S-III-S seat for such aircraft as the McDonnell Douglas AV-8B Harrier.
“We moved only in January of last year for the production side,” Alberts says. “We had an incomplete area that was still under construction until June of this year, and the facility is now fully open.” Although the final expansion has just been completed, Collins hit its full production rate in 2022 and already has begun to accelerate this through early 2023. “Last quarter was a record output for us in this building,” he adds.
The modernized site incorporates an updated receiving and inspection area, computer-controlled vertical lift modules for retrieving parts from inventory and a specialized inspection gauge table for closely checking the final build tolerances on the ACES II seat.
The production flow also includes a horseshoe-shape cell painting booth and a mechanical electrical assembly area where the functional items are attached except for the energetics that initiate the ejection sequence and the parachutes. “These include cables, linkages, decals, the oxygen bottle system, the inertia reels—all the parts that move on the seat,” Alberts says. Seats then pass through the pyrotechnics area to be fitted with initiation devices; each seat contains between 12 and 20 energetic devices, depending on model. The larger-scale solid rockets that propel the seat from the aircraft are produced separately in Collins’ Fairfield, California, facility and are combined to arm the seat upon delivery to the operator.
The pyrotechnic installation area differs from the one in Collins’ previous facility—a site that was shared with the company’s adjacent commercial and military aircraft seat production line in Colorado Springs. “We did have a large sand-filled cinder block bunker that created quite a monument that we had to work around,” Alberts says. “So in the new facility, we’ve opted for maximum flexibility as we’ve worked through all the design and layout.”
The new layout incorporates eight mobile magazines that provide flexibility depending on inventory requirements. The pyro room also includes a day box from which the company’s two state-certified explosives handlers move items for consumption each production day.
The pyrotechnic area is partially floored with electrostatic dissipating tiling and is carefully climate-controlled, as is the nearby parachute loft area, which has double the chute-packing space of the previous site. The space also includes a dedicated inspection table that eliminates any potential capacity conflict with production and packing of the now-standard GR7000 main recovery parachute, which was introduced after Air Force qualification tests in 2017.
The final area completed under the third phase of construction is ready for the rate ramp-up, Alberts says. Additional office space has been added to support the expansion. “Phase three is critical for us,” he adds. Another new capability includes a bead blast machine, which can remove paint and primer for rework without damaging the underlying plating or base material. The phase-three transition also features an expanded area for maintenance, repair and overhaul work.