
MIAMI--What it takes for MROs to become more digital, as a holistic operation, can be seen by the transformation process underway at AAR. While drone inspections and augmented reality are the attention grabbers, there are many behind the scenes digital transformation projects there as well.
AAR recently shifted its digital strategy to focus on external and internal customers, as opposed to just being customer-centric. Taking this more holistic approach of “how we make ourselves more efficient, more intelligent and make better decisions, allows us to be a better provider of services to our customers,” says Rahul Ghai, AAR’s chief digital officer. This all leads “to a more productive workforce that gets us closer to our vision of being a digital company,” he adds.
Ghai, who joined AAR in July after nearly 12 years with United Airlines, most recently as managing director of digital technology, says the aftermarket service company started building a 2-3 year road map for digital services that spans the company’s portfolio.
“One of the biggest challenges has been where to start, because there is so much opportunity,” says Ghai. “We have to be strategic about where we place our bets.”

Think of those bets as building blocks.
For MRO, the digital blocks include going paperless, making inventory smarter and making MRO more efficient—including the use of drones and augmented reality (AR).
AAR hopes to be a paperless operation in 18-24 months, resulting in a 15% efficiency gain for technicians, says Ghai. Today, tasks cards and documentation are still mostly paper, so technicians walk back and forth between the aircraft to get their next assignment and task cards. “We’re reimagining their processes, where they all have a mobile device and everything they need is on that device,” he says. “The idea is to tie images, documents and historical log page data together so that we start to run the learning algorithms against it,” says Ghai.
The goal to become paperless is to include everything from integrated planning and execution to dynamic workforce management and mixed-reality collaboration.
AAR’s Miami facility is trying out AR for hands-free workflow and communication. It is using RealWear HMT-1 headsets and Librestream’s augmented reality platform.
With AR, a junior technician can show a master technician what he or she is doing and get instructions overlaid onto the tasks. AR will save master technicians’ time spent walking around the hangars answering questions, similar to how AAR’s engineers field frequent questions from their desks.
AAR also is using AR to grant permissions before technicians cut and drill sheet metal. A technician can use the hands-free video, voice and photo capabilities to collaborate with a remote expert before making the cut.
So far, technicians and quality assurance managers report positive engagement with the tools.
DRONES
AAR’s Miami facility also is piloting drone aircraft inspections. The process could take 1-2 years, from bringing in off-the-shelf technology to conducting live pilots, getting it certified and scaling it.
AAR is using a Donecle drone for Boeing 737 general visual inspections (GVI) and has seen at least a 50% reduction in time compared to its traditional manual procedure. The drone flies itself on a preplanned flight and takes 1,500-1,900 pictures per narrowbody aircraft. “The quality and the data is what gets us really excited,” says Ghai.
AAR plans to conduct 150 inspections during the pilot phase.
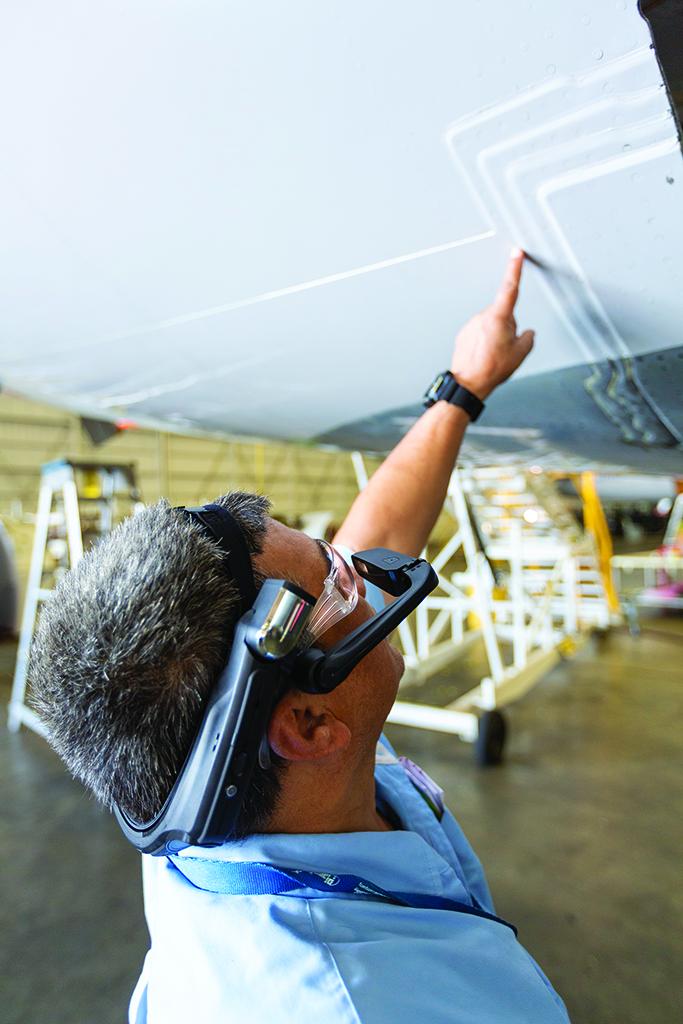
As AAR pursues FAA certification, an inspector is reviewing the photos and identifying follow-ups and lightning strikes, in parallel. The drone system identifies more abnormalities, about 10-20% of which are false positives, but AAR says there is still an advantage over people and equipment moving around the aircraft.
To get the GVI-by-drone process certified, there are two options. Either Boeing approves it and adds it to its aircraft maintenance manuals, or AAR can work with a consortium to gain approval. AAR is pursuing both, including working with a group that includes the FAA, Boeing, Airbus, United Airlines, American Airlines and some component OEMs, says Matt Kammerait, AAR’s director of digital and emerging technology. Industry sources say the FAA liked the consortium idea pursued by Airbus and airlines for A320 approval. “We think a rising tide raises all boats.” says Kammerait. “It’s good for everybody if everyone has visibility into what’s possible.
He thinks it will take another 9-18 months to obtain FAA certification for drone inspections inside the hangar. For the long term, the MRO would like to be able to use drones to inspect aircraft for lightning strike damage at airport gates, but that requires different authorizations.
While the maintenance staff have found it easy to learn how to use the drone, they asked for extra rechargeable batteries to be included as part of the process, because the battery needs to recharge after each flight.
Digital Details
As part of its digital journey, AAR also has developed in-house a closed-loop process for quality and safety management. The tool, called Aprise, includes everything from investigations to audit findings, customer feedback, injury reporting and import/export compliance. The tools within it—including self-audits, decision trees and investigation checklists—allow managers to immediately review and fix problems.
“Every employee has access to the dashboards because we think it’s good to be open and see what’s happening in the building,” says Shachar Hacohen, director of corporate environment, health and safety.
This system also includes Safety Management System dashboards, which AAR built in-house. AAR reports that since this program went digital and became part of Aprise, it is seeing more proactive reports.
To solve a problem in Miami—lots of aircraft movements—AAR also developed HangarNotes. It provides a sky view of the hangar floor, with each aircraft rendered to scale and color-coded to reflect its status. It is a way to see where aircraft are, by tail number, work overview and customer.
Although AAR created HangarNotes to solve a problem, it is considering commercializing it.
The combination of digital projects makes “AAR an easier company to work with,” both inside and out, says Ghai.