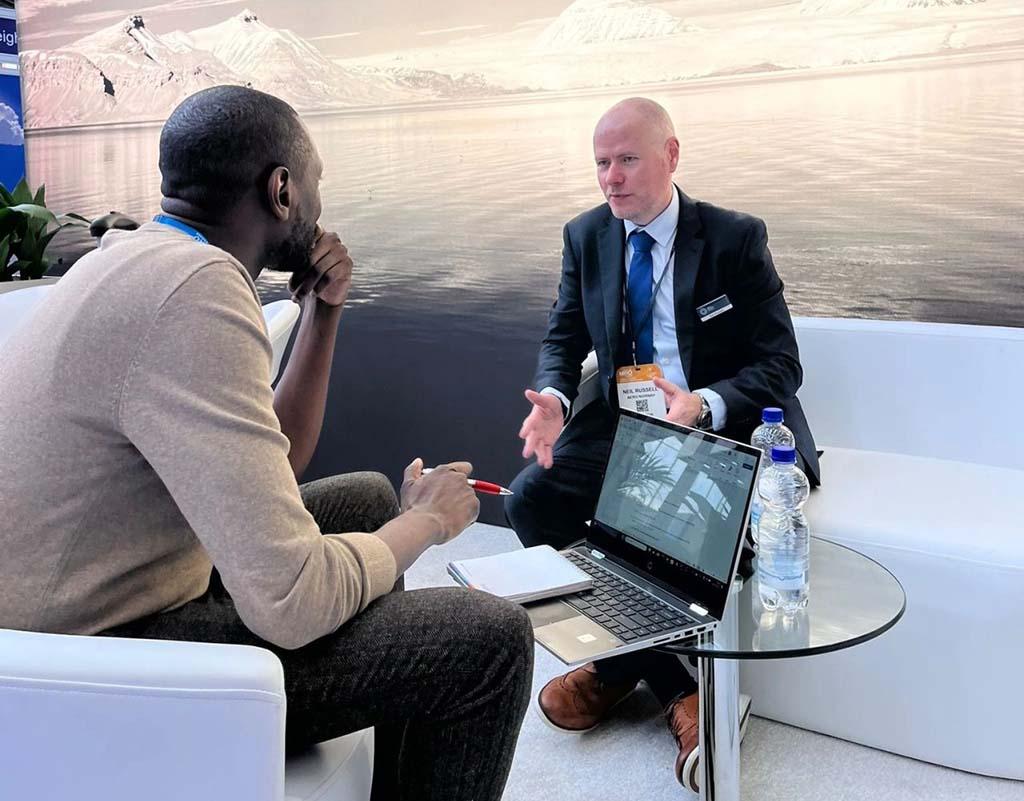
Aviation Week contributor Keith Mwanalushi (left) speaks with Aero Norway CEO Neil Russell (right) at MRO Europe in Amsterdam.
AMSTERDAM— Aero Norway’s new CEO Neil Russell has targeted at least 100 engine heavy and hospital visits/repairs annually, he reveals. “We are doing around 90 engines now. The facility has never done more than 100 but we want to reach that figure,” he tells Aviation Week.
Prior to the pandemic, engine induction projections circulating at Aero Norway suggested around 120 engines per year by 2020, however, Russell feels the immediate step target of 100 is a more realistic projection today.
His first priority as CEO will be to stabilize the team during the process of change, ensuring an easy transition. He also wants to see enough capacity for heavy MRO programs across its core engines—the CFM56-5B and -7B—especially from next year.
Pre-pandemic, Aero Norway saw around 60% of shop visits accommodating -5Bs and -7Bs but, when COVID-19 hit, much of that work reverted to the CFM56-3, primarily supporting the air cargo market. Russell confirms the focus is now back on the -5B and -7B. Four -3s are currently in Aero Norway’s Stavanger shop and, while work on this platform will continue, the volume coming through going forward is on -5Bs and -7Bs.
“We are also focusing on process improvement. There is process waste in the business, and every business has it, so we need to manage how to take that waste out to improve,” he says.
Russell observes several work scope requests from customers as the business climbs out of the pandemic, ranging from full heavy overhauls (including new life limited parts), low-pressure turbine changes, module swaps and special procedures/light work scopes in the hospital bays, which are currently full.
Although Russell says it was a slow restart post-pandemic, demand is back. “Recently, we almost peaked out on our max engines in work in progress, primarily because the turnaround time for the part repair window of the overhaul process is quite high (observed across the industry), but we have stabilized that through various mechanisms like adding key parts to stock,” he says. “We don’t want engines to stop. We want them to keep flowing through the overhaul process and [to] ship the engines quickly.”
Further, Aero Norway sees some traditional CFM56-3 operators shifting to -7Bs, and this is further pushing demand on the next-generation platforms.
Russell is familiar with all the supply chain disruptions and high repair costs the aftermarket is facing. He says Aero Norway is analyzing several possibilities to address this, including bringing some repairs in-house. “Essentially, in-house is where you want to go but it has a capital cost, and it takes a bit of time,” he says. “However, we want to do some of that, and it was always in our plans to do more in-house investment.”
In terms of rising material costs across the industry, Russell acknowledges that passing down the cost to customers might be unavoidable. “CFM has had a couple of big price increases and that changes the whole market because used serviceable material is all linked against the catalog list price. If that goes up, then everything else goes up,” he says.
The CFM Leap is a natural progression for the business and Russell admits the pandemic did slow down discussions with CFM, which are now back on track, at least as far obtaining the license. “We are talking to them about it, and hopefully this progresses well,” he says. “Our plan would be to introduce this over the next few years but keep the work scopes light and to only a few engines at a time.”