Freebird Airlines’ Maintenance Strategy Post-Pandemic

Oguzhan Demiral, deputy managing director at Freebird Airlines explains why forward planning of shop visits and flexibility in its line maintenance are at the forefront of the Turkish charter carrier’s MRO strategy.
How has the COVID-19 pandemic affected Freebird Airlines and its maintenance operation?
Cash flow took an immediate hit at the height of the pandemic in 2020, as there was no cash coming in with flights grounded. As our entire fleet is leased, this meant speaking to the lessors about payment terms and restructuring them. Luckily, this was agreed for the first three months, but this kept changing as the recovery was clearly some way off and nothing much was changing throughout that year.
Eventually, we re-negotiated terms with the lessors over the long term. This included extending some of the leases and spreading out payments over these terms, something that is still going on today. We also re-negotiated payments with OEMs and other suppliers. On the manpower side, thankfully we didn’t lose any staff due to COVID-19. The Turkish government introduced a short-term working policy, and it was actually forbidden to let people go from their jobs during that period, with the government paying staff through unemployment funds. Our staff were mostly coming in sporadically to service our grounded fleet.
What are some of the key elements around Freebird’s maintenance strategy?
We haven’t changed too much, really. Our maintenance strategy is pretty much going in the same direction as before. This has several key elements. First, effective engine-shop management. We give big importance to this and the expertise our partners offer us, as we see engine maintenance as perhaps the most important part of the entire maintenance process. If this is managed well and cost-effectively, then that is a win. Every single engine shop visit is a seen as a project for us. Back in 2018, it was projected to us that our CFM56-5B engines would have 8-10 shop visits over a five-year period. Working with CFM International, we asked them to take these engines with their green time taken off and exchange them for new CFM56-5B engines. The old engines were given back to the manufacturer to utilize them as green-time engines in their spares fleet. Given the pandemic in 2020 meant much lower utilization, it has now nearly been five years and we’ve had no shop visits yet.
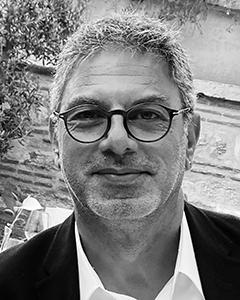
What about your line maintenance, which is carried out in-house by the airline?
We do flexible line maintenance. This means our line maintenance organization is operated to serve all the changing needs of the airline immediately. We’ve found that if this maintenance is outsourced, then it can be tough for that MRO provider to get aligned with the operation in a very efficient way. There are also culture considerations—a different entity may not be in line with Freebird’s culture; but if we deploy our own staff, then they will know exactly how to work. We are deploying our own line maintenance staff for the best adaptability and flexibility. When working with third parties, we also like to get support from where it is effective. We don’t make a big effort for daily routines; instead, we only focus on existing problems. For example, we have a parts-pooling agreement with Turkish Technic, which provides parts rather than us going to the market for every component we need at that time.
Given capacity constraints, has MRO slot availability been challenging?
Yes, but we try to plan our airframe and engine maintenance slots almost a year in advance. This year, upon receiving one of the aircraft from the lessor, we asked them not to plan a C check, as it was very early for this work to be carried out. Instead, we prefer to do it next winter, although we’ve still yet to find a heavy maintenance slot for this aircraft. We are certain we can find that slot somewhere, but 3-5 years ago, this slot would have been instantly available. Now, MRO providers are booked. This shortage won’t go away quickly, so we will continue to do our projections and book well in advance where possible.
What has been your experience with the labor market and the challenges it brings since the pandemic?
There is no big turnover in the labor, and 65 is our company retirement age. We’ve had experience of other companies poaching our staff, so it is a competitive market. This is mostly about experienced people being approached from places in Europe. However, we’ve built a strong reputation and have been able to actively recruit people of our own such as engineers, technicians and logistics staff. For younger people with less experience, we recruit mostly through internet applications before putting them into our staff and developing them. We have three divisions in our technical department—CAMO, which has eight staff, logistics with five, and line maintenance, which employs 45-50 people.
Has the pandemic been a good time for airline maintenance divisions to innovate? What technology investments is Freebird prioritizing?
During the pandemic, we focused on survival so, unfortunately, innovation plans went into the background. All our efforts were on finding cost reductions, cost restructuring and ultimately surviving. Now things are returning to normal, so we’ve started to think about innovation again and putting resources toward some projects. E-tech log is a priority for us, as we look to move away from paper technical logs. We are working with a software specialist who is writing this uniquely for Freebird. We already use a journey log system, and this newly developed E-tech log system will be an attachment to that. We will start to use this soon; that project is in its final stages. We also use a third-party maintenance management system for our CAMO activities called Wings, and our self-built Freebird portal for our line maintenance, which helps us with real-time tracking of tasks.
Freebird Airlines Fact File
History: The airline was founded in Turkey in 2000 and started operating the next year. It operates charter flights from Turkey to Europe and the Middle East.
Fleet: Freebird Airlines operates 12 Airbus A320-200 aircraft in total, all of which are leased. The Turkish side of the business has nine of these aircraft, while its Europe operation has three. Two more aircraft will be added to the Turkish fleet in July, taking the overall size to 14, although one will return to its lessor by the end of the summer.
Maintenance locations: The main line maintenance operation base is in Antalya in southwest Turkey. Freebird also has an administrative office in Istanbul. Other Turkish line stations are in Bodrum and Dalaman. Overseas, it runs a line station through a partnership with TUI Fly Belgium based in Brussels.
In-house capabilities: Freebird Airlines’ Turkey operation has an in-house line maintenance operation, although this does not extend to its Europe business. The airline’s technical division is also CAMO-approved.