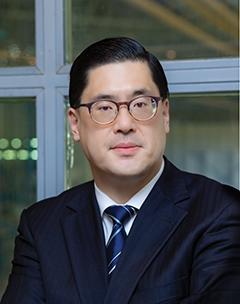
Marc Szepan
Marc Szepan joined Gameco one year ago as general manager, following Norbert Marx’s retirement. He spoke with Lee Ann Shay during MRO Asia-Pacific in Singapore about leading the 7,000-employee MRO in Guangzhou and a Comac milestone.
How is Gameco’s airframe maintenance business? In terms of airframe activities, line maintenance is on a good recovery path. In China, domestic flights are above the pre-crisis level, but international flights are below 50%, so international line maintenance activity does have some catching up to do.
We run 31 heavy maintenance lines, if we have ideal hangar utilization, for narrowbody and widebody aircraft. We are grateful to have China Southern as both a 50% shareholder and as an anchor customer for the business. We have an increasing roster of global premium carriers—including a deal with Lufthansa for the heavy maintenance of its Airbus A350 fleet. We completed the first intermediate layover check, which is a six-year check, and extensive cabin refurbishment at the end of last year. Earlier this year, we completed the first repainting of a Lufthansa A350.
For heavy maintenance activities, third-party customers now account for more than 50% of our business.
We run three lines for the 737 Boeing Converted Freighter program and two lines for the 767, which makes us the only partner in the Boeing network able to convert both at the same site.
We are also very proud to be doing the first conformance aircraft for Comac, converting an ARJ21 passenger variant to a freighter.
Comac holds the supplemental type certification, but Gameco is doing the actual conversion, and we contributed to the engineering effort. For our workforce, being predominately Chinese, it’s a special feeling to complete the first conversion of the first domestically produced passenger aircraft.
What is the status of the Comac conversion? It’s in the final phase. The physical conversion work is almost complete, but given this is the first development aircraft, there are some additional approvals that need to be done.
Who is the customer? I cannot say. But it’s actually the first two development aircraft, and there will be two launch customers. They are both cargo airlines. We are doing two development aircraft in parallel.
What do you think the market is for this converted Comac? It’s a solid aircraft. The total number of ARJ21s produced and delivered to customers is well above 100, so I think the market will be constrained by feedstocks.
Any other airframe news? We had the great pleasure of being part of the effort, along with China Southern Technic, the operator’s engineering entity, and Boeing, to bring the Boeing 737 MAX back into service. China Southern was the first Chinese carrier to operate regular 737 MAX revenue service. We supported the maintenance work, and the aircraft is flying a lot and very reliable.
What is Gameco’s relationship with China Southern Technic? Gameco takes care of the line maintenance needs of the China Southern fleet based in Guangzhou. There are around 200 aircraft. For the fleet that is based outside of Guangzhou, at various branch companies, China Southern Technic takes care of the line maintenance. On the heavy maintenance side, we take care of all the widebody heavy maintenance needs of China Southern. On the narrowbody side, at some branch companies, they have capabilities to perform narrowbody maintenance, so narrowbody maintenance is shared between Gameco and those sites within China Southern Technic that have narrowbody maintenance capability.
Gameco has extensive component capabilities. Will you be expanding them further? Our component business is doing very well and we are grateful for the OEM partnerships that we have. For instance, we have one with Spirit AeroSystems for composite repair, and we recently delivered the first Rolls-Royce RB211 inlet cowl and first GE90 fan cowl door to Spirit. We just signed an extended partnership with Honeywell, and we partner with Safran on landing gear overhaul. We are in the process of growing our component capacity and capability. Over the last few years, we have invested significantly in our PMA (part manufacturer approval) capabilities.
In addition to component repairs, Gameco is also manufacturing parts. How many? Over the last few years, we’ve invested significantly in our PMA capabilities. We can manufacture about 17,600 different part numbers.
Gameco is implementing a new ERP system. What is the status? We are developing it in partnership with a Chinese software company because we feel having additional in-house digitalization capability—the internal skills and competencies—is crucial.
The first couple of modules are running, and we should finish developing and implementing the final modules in the middle of next year.