How New Technologies Are Aiding Air Canada’s Maintenance Operation

Tony Lowery, vice president for maintenance at Air Canada, shares why the flag carrier is tapping into new technologies and software management tools to target improvements in areas ranging from fleet management to predictive maintenance and the supply chain.
What are some of the key elements of your existing maintenance strategy?
Air Canada has a strong leadership team in place at its maintenance operations and continuously invests in new technologies to optimize processes. This includes new software to manage our inventory as well as our logistics footprint and network. We have also enhanced our manpower planning and forecasting through new software. Our aircraft maintenance engineers use tablets that are connected to our network and receive up-to-date information on the aircraft they are assigned to, enabling them to have the parts needed for the repair already with them, thus improving efficiency and minimizing downtime for an aircraft.
How has your maintenance operation recovered since the COVID-19 outbreak two years ago?
Air Canada’s recovery has been stable, as we have ramped up our fleet operations and returned most of our aircraft to active service. Unlike many airlines, Air Canada has continued to operate throughout the pandemic, so our maintenance functions carried on. The majority of Air Canada’s fleet, both mainline and Rouge, is back in operation. During the worst period of COVID-19, Air Canada reduced its workforce across all branches by nearly 20,000 people. Most of those who were eligible to return and wished to return have since rejoined our workforce.
Has the pandemic represented a good chance for airlines to innovate in MRO?
The pandemic has been very challenging, as cost-reduction and cash conservation has been the order of the day. However, we did make significant changes in critical processes where lower volumes allowed us to adapt, measure and future-proof them for growth and complexity. One example is the use of an onboard parts bin to allow maintenance during natural ground time in the schedule. We also embarked on upgrading our material management software system and redesigned our logistics network, with the goal to reduce inventory and increase material availability. That effort should be completed this year.
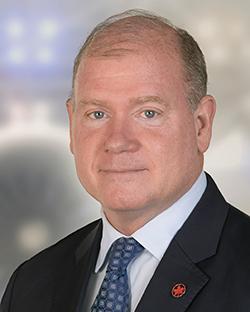
How is the maintenance division ramping up for Air Canada’s fleet modernization plans?
Air Canada’s maintenance division offers a very innovative training program that is flexible and adaptable to any changes in fleet mix and growth. We’ve had an ongoing fleet renewal program—beginning with widebody aircraft—taking place over the past decade, so we are well-versed in incorporating new aircraft types into the fleet and our maintenance programs.
Do you foresee the airline insourcing more maintenance work long-term or outsourcing to third parties?
Air Canada has always kept a healthy mix of in-house operations and outsourced work, and there is no plan on that changing. We have sufficient capabilities to maintain our fleet to a healthy and reliable standard. We also have a long-standing relationship with local MRO providers to supplement any needs that may arise.
Are you anticipating capacity constraints across your maintenance network as soon as maintenance demand picks up?
As mentioned, we have a very strong management team and advanced technology to optimize our processes, including manpower requirements, and this allows us to plan effectively for future workflows. While Air Canada does not expect any near-term constraints, we continue to look out for future challenges and develop appropriate mitigation plans to address those constraints before they arise.
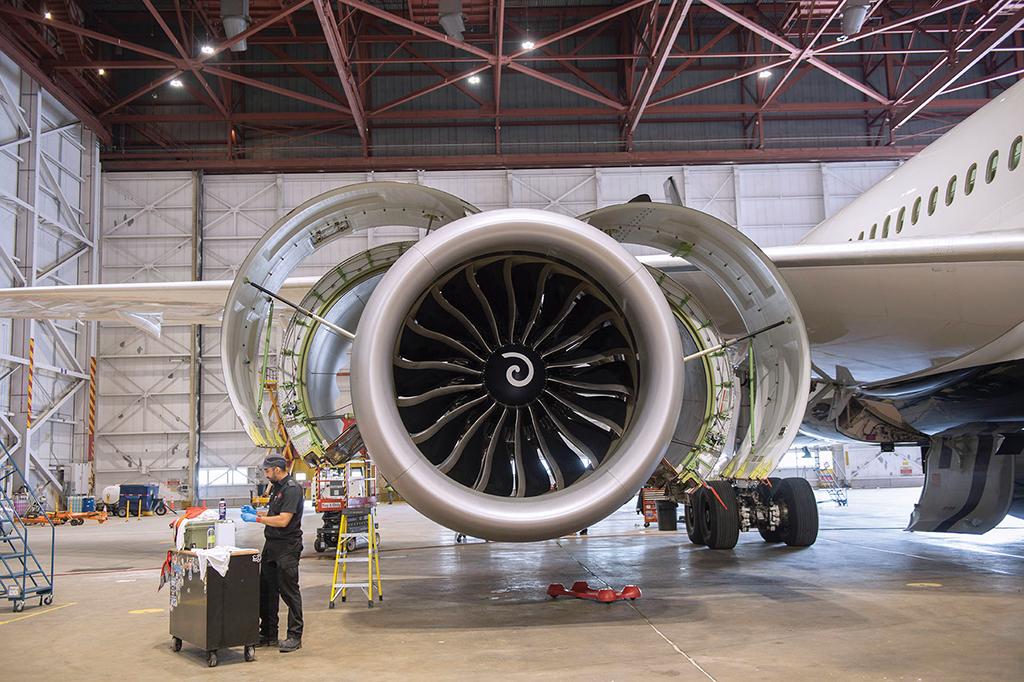
Which technology investments is Air Canada prioritizing across its maintenance hangars, and what benefits are you gaining?
In addition to the manpower and inventory technologies, Air Canada has also invested in artificial intelligence tools to forecast significant maintenance events and identify cost-avoidance strategies to lower costs and improve fleet reliability. We are currently in Phase 1 of its rollout in maintenance, which will focus on optimizing high-cost maintenance events such as those for airframes, engines and components. Inventory allocation management tools have allowed us to improve and optimize our inventory and supply chain to lower costs and also remove waste. We currently use the latest version of TRAX as our primary maintenance management system, and we are considering upgrading to TRAX 15.
How has the Air Canada supply chain held up over the past few years? Have there been challenges?
There have been significant supply chain challenges across all industries; however, lower traffic volumes have helped mitigate the operational impact. The new software tools will provide additional levels of insight to ensure we don’t fall behind our growth plan. Digitalizing and automating transactions with the goal of higher compliance, cost control and improving the speed of the supply chain is a must. Predictive tools will be deployed and information-sharing with strategic suppliers is a necessity. The global supply chain must improve, and that starts with customers understanding and forecasting their needs better.
What is Air Canada’s experience with the labor market in 2022? Do you anticipate challenges?
We will be able to meet our labor needs for this year and into 2023. Experienced aircraft maintenance engineers (AME) seem to be available, and we are forecasting our long-term needs. While there is no doubt competition for talent, Air Canada is well-placed because of its attractive work environment as well as the opportunity it affords to work on an ever-changing array of state-of-the-art aircraft. While we have been able to bring in talent from the outside, Air Canada also can upskill and train technicians to become AMEs in-house, if needed.
What are some of the sustainability initiatives Air Canada is undertaking across its maintenance division?
Many of our initiatives have been aircraft-related, from reducing the use of the APU, removing weight from the aircraft and finding better ways for cleaning engines. We are exploring the use of flight data to measure fuel-burn and aircraft trim characteristics prior to major maintenance and post-major maintenance to identify benefits and actions needed for improvement.
Air Canada’s maintenance teams, as well as flight crews and other areas of our operations, have also gone paperless. This not only reduces paper consumption, but the elimination of bulky onboard manuals also reduces weight on the aircraft, which reduces fuel consumption.