
Paul Kinstedt, Republic Airways senior vice president and chief operating officer, spoke during the C-Suite series at MRO Americas on April 27. He answered questions from Aviation Week Executive Editor for MRO Lee Ann Shay.
With so many changes over the last year, how do you balance your operation and demands from the three carriers for which you fly—American Airlines, Delta Air Lines and United Airlines?
We saw our block hours and departures go down to about 20% of what we scheduled early in the pandemic. We were able to work with both the pilot and the flight attendant unions to come up with different programs, to give voluntary time off. We didn’t have to furlough any of our active employees. It was really great for them to come together and work with us.
We’re heavily focused in the Northeast. With business travel just falling off, we shifted our flights in tandem with our partners. We were able to move into different hubs that we typically weren’t in. We had to do some TDY [temporary duty travel]-type operations and move people around. We had to close a couple of crew bases, but we were able to really pull together as a group and meet the demands of our customers—United, Delta and American. And they were great partners. Our team did a great job of working together and reacting and getting us through.
Then early last fall, we really started to see a pick-up for our operation because they were replacing some of the mainline flying with regional flights—and the Embraer 170 was a great option to put into some of what would normally be mainline narrowbody markets. We were able to work with [the airlines] and build up those routes. Now we’re more than 80% back on block hours of where we were in early 2020. So the recovery for us has really started to kick in aggressively.
Do you plan any fleet changes in the near future?
No, we like the Embraer 170/175 fleet—and having a single fleet and a single engine type makes everything extremely simple. It makes us a lot more nimble and able to react to changes in the market. We think that the Embraer 170/175 is the premier retail aircraft out there. A lot of people as they board say it seems like a mainline narrowbody. They love the overhead space. It’s comfortable. It’s two-by-two seating so there’s no middle seat. It also has the three-class service of our partners. So all of them have first class, the Economy Plus or Delta Comfort, and economy. It’s good for our partners that they can manage what kind of tickets sales that they want to have and the passenger loads on that aircraft, which can go up and down, depending on what they’re seeing in the market.
We previously operated four different fleet types. We were ecstatic to get rid of the others and consolidate to a single fleet. It just makes sense, especially on the technical side. It’s much easier for the technicians and the management team to focus on one fleet type and work with our maintenance providers and component providers. We’ve been a fleet leader. We were the first carrier to run Embraer 170s in the early 2000s in North America. So we built up great relationships with Embraer and all of the OEM providers.
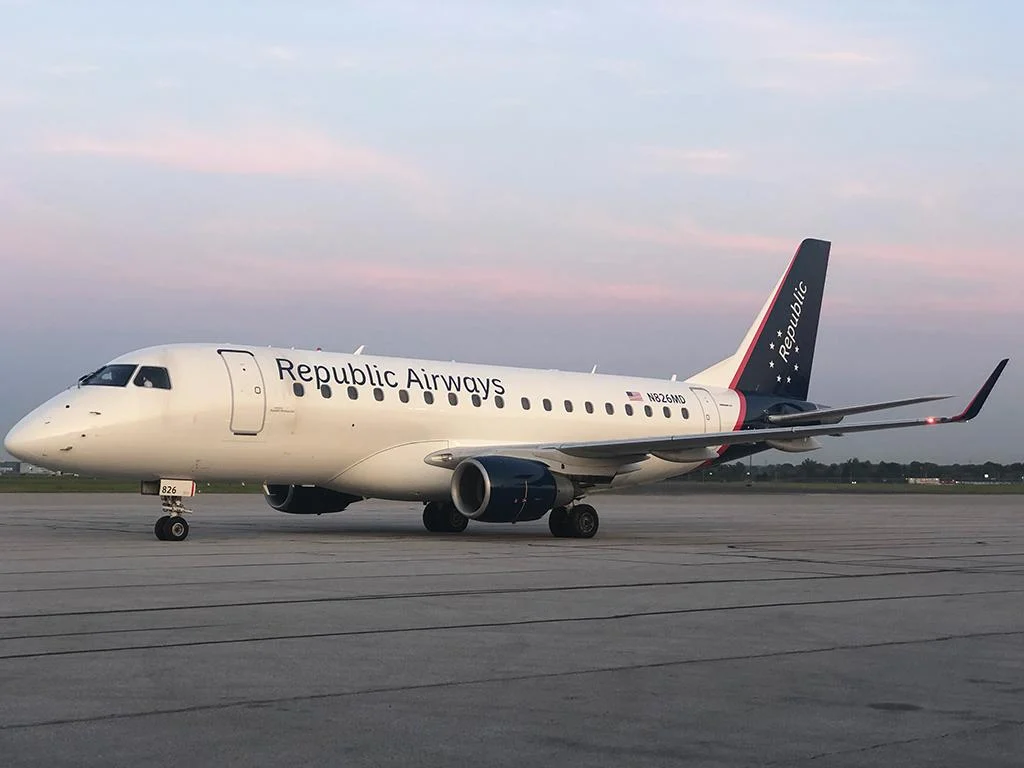
You said your operation is at 80% capacity. When do you expect to be at a 100%? What’s the outlook for the rest of the year?
We’ve got 100% of our fleet back up in the air. The aircraft themselves are flying, which is great because they do not like to sit on the ground. So getting them up, getting them exercised continuously, is really helpful for the fleet. What we’re seeing is our utilization is down. So instead of flying 10.5-11 hr. per day, we’re flying 8.5-9.5 hr. All of our technicians are back, we’re in full scope for heavy checks and supporting the aircraft, and all of our hangar bases are fully operational. What we’re seeing is a little bit less actual block hours on a daily basis, but it’s been enough.
Republic Airways operates its own pilot and technician school. How many technician apprenticeship spots do you have for your Lift Academy? What would the maximum capacity be?
Our Indianapolis Academy can handle about 300 flight students and 30-40 maintenance technicians. We are close to signing a deal for a second campus location, probably in the southern U.S. It would probably start at about half the size of the Indianapolis Academy, but have the potential to grow. We’ve got 50 Diamond aircraft but have options to order more so we could build up another campus that could handle 300 flight students.
The pandemic has spurred a lot of innovation, especially on the digital side for MRO. Does Republic have any digital initiatives innovations underway that you can mention?
We’re investigating a lot of opportunities. We’re working with Embraer and a number of manufacturers, including GE, to come up with what a connected aircraft can tell us. You can get terabytes of data from an airplane on every flight, but you have to use that effectively. We want to see operational performance and ensure aircraft reliability. Partners pay us to be there and be there on time. We’re really focused on the operational integrity and the performance, and the associated cost.
Last year, we installed an RFID system on our emergency equipment that took a 4-hr. job card to 30 min. We’ve issued iPads to all of our technicians, so they have electronic manuals and the RFID system, so as they walk through the aircraft it verifies the dates of the emergency equipment. If there’s something that needs to be changed, it flags it, or if it comes through green, they can sign off on the job card. We’re also looking into how we can better work with our manufacturers and vendors on component reliability. How can we take off the component at a convenient spot versus having it break in Key West [Florida] or Hilton Head [South Carolina], where there’s limited technical support?
We use Ramco’s maintenance system and just installed AirVault to ensure records reliability. We doing more digitally and looking at the electronic log book. We think that will alert us when maintenance is due and make sure that human error doesn’t happen. For instance, if you have a two-day check, it automatically flags you and won’t let you fly again without a human coming in and verifying it—whereas today, that’s on another computer system that can just be a flag and somebody can miss it.
So how many different systems are on the iPad? How are they using iPads now?
They’ve got all their manuals. What’s unique for us is we operate for three different partners and some of our airplanes have operated for multiple partners. So all of those aircraft have had different configurations. It’s not like you just have one manual in one configuration on one aircraft. That’s very straightforward. There’s multiple layers on one. Was this work done? What configuration was it in at that time? The technician has to dig in and find exactly which parts are right. So there might be four different parts that are exactly the same but it might be a different color. It might be a different seat type, depending on the partner that we’re working for. So that’s where we see the technology really helping the technician versus having to go through volumes of paper to figure out exactly which component goes into which aircraft.
Do specific technicians work on specific partner airline aircraft or do they work across the board?
Across the board—because that’s where we get the cost-efficiency. We have hangar bases in Pittsburgh, Louis-ville, Columbus and Indianapolis. None of our partners would want to put eight aircraft into one of those stations on an overnight. But if one puts in two, another puts in three, another one puts in three, all of a sudden you have the eight aircraft that keep the entire hangar busy throughout the night. So you get that efficiency and then we swap those out so they can rotate into and out of the different hangar bases. All the hangar bases can do the exact same type of work.
This is efficient, but it makes our planning a little bit more challenging. We have to make sure that we level the workloads. We did a Theory of Constraints project two years ago that examined how often we bring aircraft into a hangar. When an aircraft comes out, how many days is it good for before it needs to come back into the hangar? We really want the aircraft out on the line flying consistently and don’t want the aircraft visiting the hangar too many times because other tasks need to be done. They now come back in effectively once every 35-45 days, and then they’re done and then they can go back out onto the line. Those are the technology pieces that we’ve really been working on to try to improve the operation, maintain the costs and make sure that we’re keeping our technicians busy.
Let’s talk about slot restrictions, a situation that is a moving target. How is that affecting you?
It really has been challenging. Aircraft are not in our typical line maintenance stations and we’re seeing a lot of overnights in Florida. We’ve got contract maintenance that we’re using for them to touch the aircraft if there’s an MEL (minimum equipment list) issue. It’s been a challenge getting the routings to come in, but that’s where the partners want to fly and that’s where the traffic is. Our technicians have done a great job. They’ve been volunteering for TDY. They’ll go away for 4-7 days to support a line station. And then they come back home.
So like I said, we’re heavily in the Northeast. We believe the slot exemption that is currently in place is going to end somewhere around October. If not a hard end, it could be some type of limited restriction. We expect New York to open back up, and carriers are not going to want to lose those valuable slots because they know business traffic will come back. So we would anticipate a shift for us toward the end of October or early November to get back up into the Northeast.
What has been nice is that it has really given LaGuardia and Washington airports time to renovate and accelerate planned gate work because there hasn’t been much traffic there. So we’re looking forward to getting back into not only the normalcy of our round of operation, but also to brand-new facilities.
Republic Airways Fact File
Headquarters: Indianapolis
Fleet: 220+ Embraer 170/175 aircraft
Employees: 6,000
Airline Partners: American Airlines, Delta Air Lines, United Airlines
Maintenance Bases: Charlotte, North Carolina (CLT); Columbus, Ohio (CMH); Washington (DCA); Newark, New Jersey (EWR); Indianapolis (IND); New York (LGA); Chicago (ORD); Pittsburgh (PIT); Philadelphia (PHL); Louisville, Kentucky (SDL)
Daily Flights: Nearly 1,000
Destinations: 1,000 cities in 40 U.S. states, Canada, the Caribbean and Central America