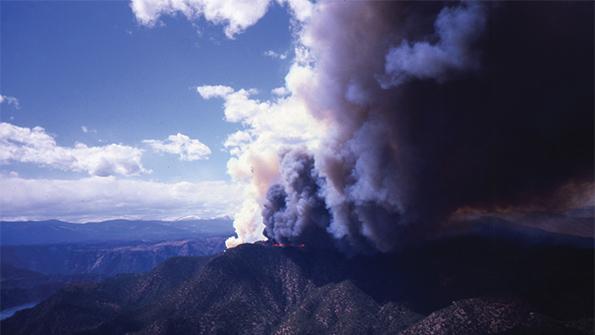
An unprecedented number of serious wildfires have occurred in recent years, and they are happening almost year-round now. Airborne resources are vital tools in fire management that are likely to see increased utilization. The increasing intensity of wildfires is certain to place inordinate stresses on our wildland firefighters and their aerial assets in these battles.
Firefighting aircraft are exposed to an adverse airborne environment significantly different from the “normal” atmosphere in which aircraft and turbine engines were originally designed to operate. This has negative consequences for the long-term airworthiness of both airframe and engine components.
Five particularly important parameters in the airborne environment created by wildfires place abnormal stresses on turbine engines:
• While the “average” air temperature around wildfire incidents tends to be excessively hot, localized plumes of super-heated air rise from the flames. Radiant heat from the flames also elevates air temperatures near the flame front far above the “ambient” temperatures.
• The air from burning wildland fuel is a complex mixture of gases and aerosols.
• Wildfires also emit large amounts of fine and coarse particulate matter.
• The air adjacent to the flame front is turbulent. Turbulent airflow through an engine inlet increases the chances of compressor stall and/or engine surges.
• Common flight maneuvers necessary for firefighting near the flame front increase the likelihood that hot gas will be ingested into the engine inlet.
All five of these adverse conditions are present simultaneously and directly compromise the safety margins of turbine engines.
Air Quality Along the Fire Line
Turbine engines were designed to operate in “normal” air, which is composed of 78% nitrogen, 21% oxygen and 1% other gases. The proper ratio of oxygen is absolutely necessary for engine combustion. If the oxygen concentration in the engine-inlet air drops below a certain ratio, the combustion process may no longer be sustainable, resulting in an engine flameout.
However, the air near a wildfire is anything but normal. Specialists at the National Oceanic and Atmospheric Administration’s Chemical Sciences Division released a report titled “The Impact of Wildfires on Climate and Air Quality,” which studied the wide variety of chemical compounds released by wildland fires. The long list includes greenhouse gases (carbon dioxide, methane, nitrous oxide), photochemically reactive compounds (such as carbon monoxide), nonmethane volatile organic carbon and nitrogen oxides.
Since wildfires consume voracious amounts of oxygen while creating the toxic compounds listed above, a localized air plume with this toxic combination renders a firefighting aircraft, especially one flying low and slow over a wildfire, susceptible to an engine surge or flameout.
Excessive Temperatures
Aerial firefighting frequently is conducted under high-density altitude conditions created by a combination of high altitude and hot temperatures. While the ambient temperatures often are exceptionally high, the immediate vicinity of active wildfire flame fronts can be even hotter. Under these conditions of extremely wide temperature variations, excessive heat can have an extra degrading effect on engine power availability.
Localized plumes of extraordinary temperatures result in increased inlet air temperatures, leading to exhaust gas temperature (EGT) fluctuations, EGT excursions and/or turbine blade over-temperatures. When subjected to over-temperatures, the internal grain structure and substrate material properties of metal turbine blades are negatively affected.
Exposure to excessive temperatures will also cause a phenomenon known as “blade rub.” As turbine blades experience high temperatures, they can begin to elongate. If the blades elongate too much, they will begin to “rub” against the walls. Research at The Ohio State University’s Gas Turbine Laboratory found that blade-to-case rub can degrade the performance of jet engines through the introduction of high-amplitude shaft vibrations and severe blade/seal wear. This can lead to catastrophic failure of the whole engine if left undetected. The smaller blade-tip clearance common to high-performance turbine engines are susceptible to blade-to-case rubbing during operation.
Particle Ingestion
Wildfires also produce significant amounts of large and small particulate matter. The smaller-size particulates remain suspended aloft in the atmosphere longer than coarse particles and disperse farther from the wildfire. Aerial firefighting helicopters are exposed for extended periods of time to varying densities of these airborne smoke particles, and the engines ingest significant volumes of these particles.
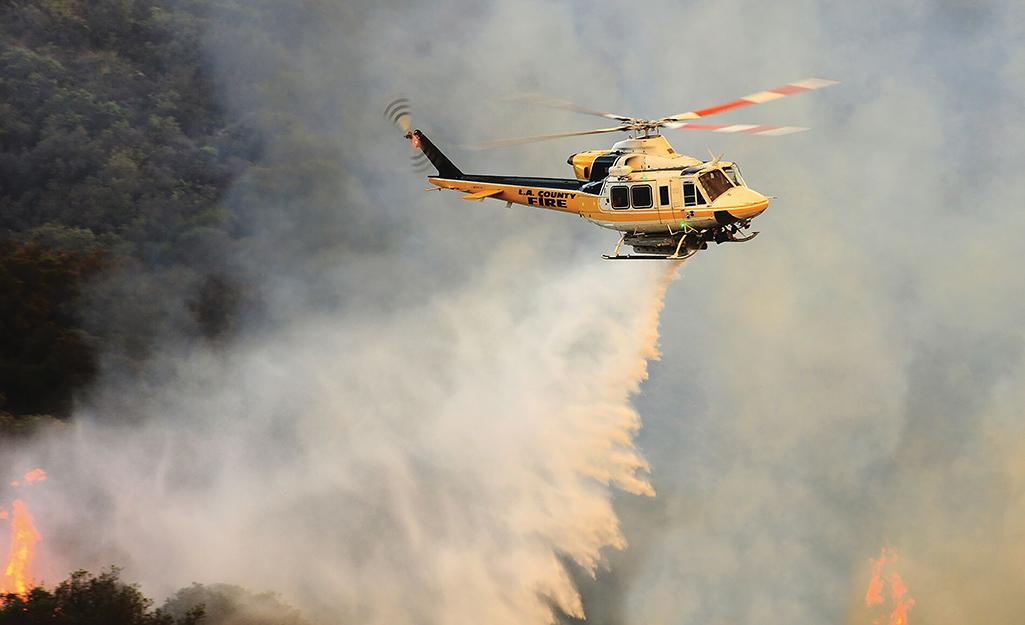
The Australian Civil Aviation Safety Authority (CASA) published an airworthiness bulletin in 2006 titled “Engines Operating in a Firefighting Environment,” advising operators about the multiple effects of smoke particles on turbine engines. To begin with, particles ingested from the smoke can block small-diameter pressure-sensing and control lines, leading to erratic fuel metering to the combustion chamber, erratic engine operation and malfunctioning of accessories.
These particles also can cause blocking of fine cooling holes within turbine blades. This loss of cooling air to the turbine blades exposes the blades to temperatures beyond their design parameters. Continuous exposure to high temperatures may result in blade failure, creep and/or rub as well as extensive damage to the turbine, leading to an inflight shutdown.
Airborne particles will also cause deposition of contaminants inside heat exchangers (such as the oil cooler) that may block free air flow and result in decreased heat transfer, which will elevate fluid temperatures. Higher-than-permitted fluid temperatures may result in rapid deterioration of internal engine components.
Finally, the smoke particles can cause rapid erosion, or contamination of the compressor airfoil surfaces on aircraft not fitted with effective air-inlet filters, resulting in loss of compressor efficiency, loss of EGT margin and compressor stall.
Engine Surges
Gas turbine engines operate best when the air is flowing smoothly through the engine. In reality, the flow within a compressor is quite complex, especially as flow near the compressor blade tips tends to be unsteady. Typical flow phenomena in rotating machinery can include vortices, separations, secondary flows, shock and boundary-layer interactions, and turbulent wakes.
The susceptibility to compressor stall of earlier gas turbine engine designs with manual or mechanical fuel control units was more common. Thankfully, later-generation turbine engines incorporate a variety of design features to reduce the probability of compressor stalls greatly. These features include the use of hydro-mechanical and electronic control systems such as full-authority digital engine controls.
To ensure safe engine operation over the entire range of flight conditions, several limitations are included in engine control systems. An N1 speed limiter constrains the maximum gas generator rotational speed to a pre-set value to avoid damage to the engine due to mechanical and pressure forces. The turbine outlet temperature (TOT) is also constantly monitored, and the fuel flow is limited to avoid exceeding the TOT limit. At low RPM, the engine is naturally not able to pump as much air. A compressor bleed valve opens when the engine starts, to adjust the airflow so that the compressor blades do not stall. Additional control devices such as variable stator vanes are used to extend the stability reserve in the low-power operating region.
When these devices operate as designed, the susceptibility of a turbine engine to compressor stall is greatly reduced. However, there are still many operational factors that reduce compression system tolerance to stall. These include distorted intake flows during abrupt maneuvers or hovering in adverse winds; reingestion of hot exhaust gases; degradation of the stall margin over time due to erosion, rubs and normal engine wear of the rotor blades, seals or bleed valves; and adverse adjustment of the engine control system.
Adverse Airflows
Turbulent and erratic winds adjacent to wildfires make a helicopter more susceptible to compressor stalls and surges. This can occur while hovering in a tailwind condition, resulting in distorted flow of air into the engine inlet. Helicopters hovering in locations with “squirrely” winds will be especially prone to this phenomena, most common in areas on the downwind side of obstructions such as large trees and mountainsides that create a turbulent wake of air in which the direction and velocity of the air changes rapidly. The airflow in the wake of obstructions will contain strong wind gradients, flow recirculation and unsteady flow.
Hot Gas Ingestion
There is an additional hazard created in the hovering environment, called hot gas ingestion (HGI). This happens when the engine exhaust gases are redirected by the rotor downwash and are reingested into the engine air inlet. HGI is particularly problematic when helicopters hover with a tailwind or during sideways or rearward flight.
HGI causes increased engine inlet gas temperatures, leading to a significant loss of power and potential flow distortion. Assuming an engine is operating at its maximum rated temperature, an inlet temperature rise of 40F due to HGI can cause a power loss of approximately 15%. In addition, temperature distortion (from the hot gases) can cause compressor stall.
Sources of hot gases are frequently found in close proximity to the flames of wildfires, where temperatures can be well above ambient. When these gases disperse into the helicopter approach, departure and landing paths, they potentially create a severe operational risk because any rise in ambient temperature along the flight path will result in a loss of both engine and rotor performance. Additionally, small increases in air temperature can result in a dramatic loss of engine power and rotor lift.
In turbine helicopters without auto reignition, the pilot needs to have cat-like reflexes to initiate a restart with the starter button. Since there is simply so little time and altitude, it is not uncommon for momentary torque or temperature exceedance to have occurred in past incidents. Given the extraordinary risk to an aerial firefighting aircraft in close proximity to a flame front, CASA believes it is prudent for such aircraft to be fitted with autoignition.
Compressor Blade Contamination
Dust, smog, wildfire smoke, saltwater and dirt in the compressor can reduce its efficiency and lead to a stall if the contamination is severe enough. This threat is mitigated by periodic “compressor washes” to remove the contaminants from the compressor. An example of recommended cleaning instructions are those included in the service letter entitled “Engine compressor cleaning—daily water rinse and periodic water wash” for the MD 369 series of helicopters powered by the Allison Model 250 gas turbine engine.
The service letter recommends a daily water rinse for helicopters operating in corrosive environments to remove contaminants and corrosive air particles from the compressor. The letter also recommends a periodic (200-300-hr.) compressor water wash for helicopters operating in smoggy areas to remove dirt buildup in the compressor. Comparable instructions are provided in the maintenance and service manuals for almost all turbine helicopters.
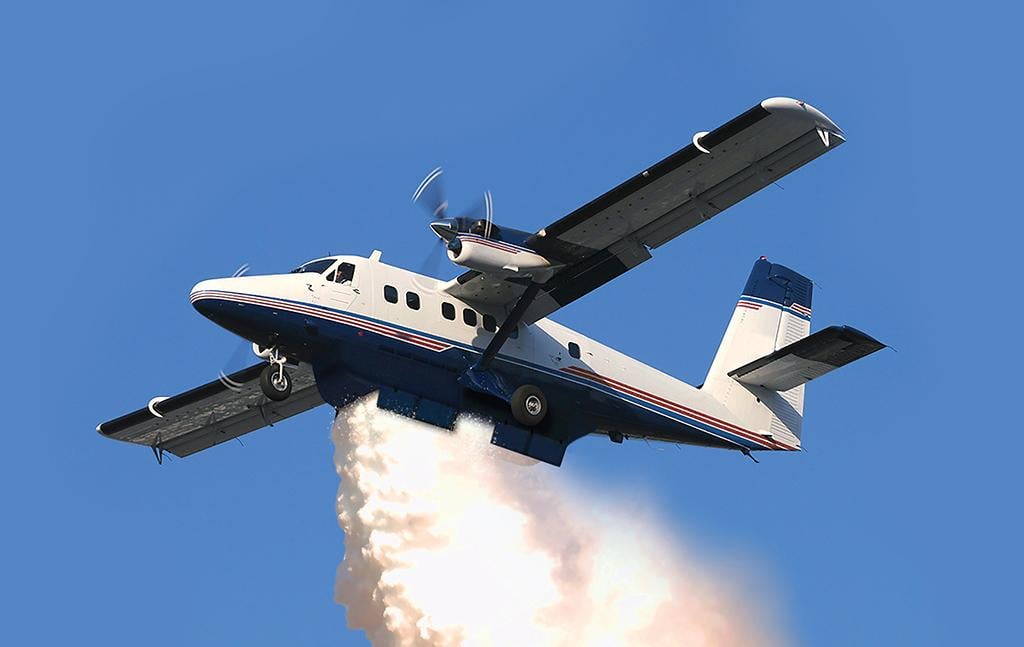
Engine Exceedances
CASA’s airworthiness bulletin titled “Engines Operating in a Firefighting Environment” advises operators of aerial firefighting aircraft that all exceedances and engine surge events must be inspected and corrected in accordance with the approved data from the manufacturer. The airworthiness bulletin states these will often specify a thorough visual as well as borescopic inspection of the engine inlet, compressor and turbine airfoil surfaces, and engine exhaust for signs of physical damage. An inspection of the engine’s inner gas path for nicks, dents or bending of blades as well as debonding and redeposition of plasma coating on the surfaces of blades and/or guide vanes should also be performed. In addition, turbine blade surfaces should be inspected for signs of loss of coating, oxidation, exfoliation and creep. If contaminant ingestion is confirmed by any of these findings, then removal of accessories for bench-check and engine compressor wash is recommended.
CASA recommends that pilots of firefighting aircraft should be encouraged to report all engine abnormalities. In the event that any of these are reported by the pilot, maintenance providers should ensure that the engine goes through inspections to ascertain the airworthiness of the internal components.
More Than Wildfire Smoke
When aircraft are operated in extreme environments—excessive heat, cold or altitudes as well as dust and sand and volcanic ash, for instance—critical components are exposed to stresses that can lead to unanticipated failures, possibly in terrain where an emergency landing will result in considerable damage and injuries. The U.S. military became intimately familiar with the destructive nature of sand on turbine equipment while operating in the Middle East.
Operators have learned from hard experience that these “off-design points” cause increased wear, fatigue, creep and corrosion, any of which can lead to component failure and, in the case of turbine engines, multiple points of failure. For maintenance technicians, this means more work and, to the extent possible in their initial stages, detecting these various failure modes. Retroactive corrections often include the need for modification of flight procedures, training of flight crews to deal with the extraordinary hazards, additional maintenance and perhaps modification of the hardware.