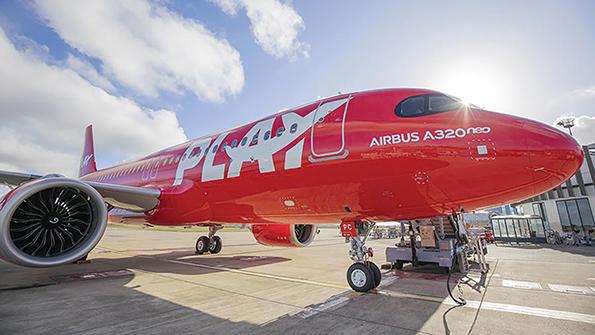
Play operates an all-Airbus A320neo fleet and recently took delivery of its 11th.
After Play was set up in 2019, how were you impacted by the pandemic the following year? The pandemic post-2019 indeed brought a significant pause to our operations, necessitating a delay in our launch by two years. Nonetheless, it served as a catalyst for us to meticulously refine our preparations. For instance, we invested considerable effort in creating a custom progressive aircraft maintenance program (AMP), which optimized the use of overnight stops and minimized the need for longer two-to-three-day A checks during ground stops.
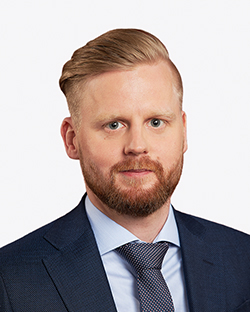
Moreover, we integrated Gannet, our maintenance software, with our flight operations and scheduling systems. This auto-rosters aircraft and schedules ground time for maintenance activities, drastically reducing manual labor in maintenance planning.
Finally, we put a strong focus on our power-by-the-hour contracts to streamline the receiving and shipping processes. This was instrumental in reducing the time needed for parts to arrive at and depart Iceland, addressing the logistical challenges posed by our geographical location in the middle of the North Atlantic. Thus, we effectively turned the challenge of the pandemic into an opportunity for comprehensive improvement.
What does Play look for when selecting a maintenance partner? When selecting a maintenance partner, Play places a premium on a series of key factors. Foremost among these are superior customer service and steadfast reliability. We also weigh heavily the reputation of potential partners within the industry. Although important, pricing is considered as the final factor in our decision-making process, ensuring we first and foremost prioritize quality and dependability.
How did the Play maintenance teams ready themselves for the new fleet of Airbus A320neos? At Play, we’ve opted to handle continuous airworthiness management operations [CAMO] for our fleet in-house, while entrusting all Part 145 maintenance activities to our external partners. Fortunately, Iceland boasts a robust legacy of managing and maintaining Airbus A320neo-family aircraft, which served as an invaluable resource for us. As early as 2019, we initiated discussions with Ground Maintenance Technics, with a vision to designate them as our home-base maintenance provider. This strategic partnership has been instrumental in effectively readying our teams for the introduction of our new aircraft fleet.
How is Play seeing the global recovery of passenger travel? From our perspective, the global recovery of passenger travel is advancing positively. For this year alone, Play is forecasting 1.5-1.7 million passengers. To cater to this resurgence, our maintenance division has implemented strategic measures to ensure seamless operations.
One key strategy has been standardizing our aircraft fleet with the A320neo family, all equipped with the same engine variant, the CFM Leap 1A. This standardization significantly reduces operational complexities and manpower requirements compared to managing a mixed fleet.
Moreover, we’ve harnessed the full potential of our maintenance software for efficient operations. However, the main focus of our ramp-up strategy has been staffing. With the projected increase in passenger numbers, we’ve placed great emphasis on adding personnel to our team to maintain our high service standards.
Over the past year, has Play experienced any supply chain challenges? Indeed, the past year has brought about notable challenges in our supply chain, particularly in terms of extended manufacturing time frames and lead times. While these complications have yet to result in an aircraft-on-ground situation, it’s clear that the supply chain landscape continues to evolve.
As it stands, we’re not seeing substantial improvements in the supply chain, which I believe is primarily due to persistent staffing shortages across the industry. Many companies, including ours, continue to grapple with staffing issues in this post-pandemic era. However, we’re proactively implementing measures to mitigate these challenges. Our strategy includes increasing our stock of parts to buffer against extended lead times, as well as closely monitoring trends in the supply chain to anticipate and respond swiftly to changes. In this way, we’re striving to ensure smooth and reliable operations despite the industry-wide challenges.
Which hangars and line stations does Play operate? At Play, we primarily focus on in-house CAMO, so we don’t operate hangars or line stations directly. However, we do maintain access to a hangar at our home base in Keflavik, which is managed by the airport authority. Most of our line maintenance activities are planned in Keflavik. If base maintenance is required, we tend to mobilize shops in the Czech Republic and Germany for these operations. At every destination we serve, we hold contracts for line maintenance, primarily to tackle any unforeseen defects and ensure seamless operations.
Which maintenance is conducted in-house and what does Play outsource to third-party MROs? Internally, our primary focus lies on CAMO. This includes tasks such as maintenance planning, airworthiness management, the application of AMPs, airworthiness directives, service bulletins, trend monitoring and other reliability activities. Moreover, we handle the procurement, repair and sales of aircraft parts. On the other hand, we delegate all Part 21 Design Organization and Part 145 Maintenance Organization activities to our third-party partners, harnessing their specialized expertise to complement our own operational capacities.
Which new technologies is Play utilizing or planning to invest in for its maintenance operations? To optimize our maintenance operations, Play has incorporated the use of Gannet, a software developed by Lundin, for managing all airworthiness tasks. Additionally, we’re employing Skywise Health Monitoring, a product from Airbus, which aids in maintaining a constant vigil over the well-being of our fleet.
Since integrating these technologies into our operations, we’ve experienced a notable improvement in the accessibility and manageability of our critical information. For instance, Gannet has significantly simplified the process of obtaining a complete overview of airworthiness status, tracking parts and maintenance history, thereby reducing the manual effort and enhancing efficiency.
In tandem with Gannet, the use of Skywise Health Monitoring has expedited data-driven decision-making. It enables quicker access to minimum equipment list references, troubleshooting procedures and in-service information letters from Airbus. These tools have been instrumental in making our operations more efficient and robust, bolstering our capacity to deliver excellent service and safety.
What are your digitalization plans for the airline maintenance business? Given that Play operates the most up-to-date A320neo aircraft, our digitalization strategy is centered around enhancing preventive maintenance technologies. By leveraging the wealth of aircraft parameters available to us, our aim is to mitigate the risk of technical delays, thereby bolstering operational efficiency and reliability. Our vision is to use advanced technologies to preemptively identify and address potential issues, promoting a seamless travel experience for our passengers.
How has the process of recruiting technicians for the new operation gone? Where have the challenges been in acquiring the necessary skills? The recruitment process for our new operations in the post-pandemic era has indeed posed significant challenges. The relatively small population of Iceland, coupled with a substantial existing aviation community, has made it difficult to source experienced personnel. To address this, Play strategically expanded its operations by establishing a second office in Vilnius, Lithuania, thereby widening our recruitment pool. This office has now been operational for over a year, and impressively, nearly half of our CAMO staff are based there. We’ve been fortunate to discover a rich vein of experienced professionals in Lithuania, which has substantially bolstered our workforce.
Play Fact File
History: Founded in July 2019 by two former WOW Air executives as WAB Air (We Are Back), the carrier rebranded to Play in November of that year. The airline commenced operations two years later in 2021, initially with a fleet of three A320neo aircraft previously operated by defunct Mexican carrier Interjet. Over the next two years, the airline has expanded its fleet of A320neo aircraft. Since the beginning of this year, the airline has undertaken reconfiguration projects to expand seating on each aircraft to 214 seats from 192.
Fleet: The airline operates a fleet of 10 Airbus A320neo aircraft. It took delivery of its latest new-generation narrowbody at the end of May.
Headquarters: The airline is headquartered in the Icelandic capital of Reykjavik, with its hub at Keflavik International Airport.