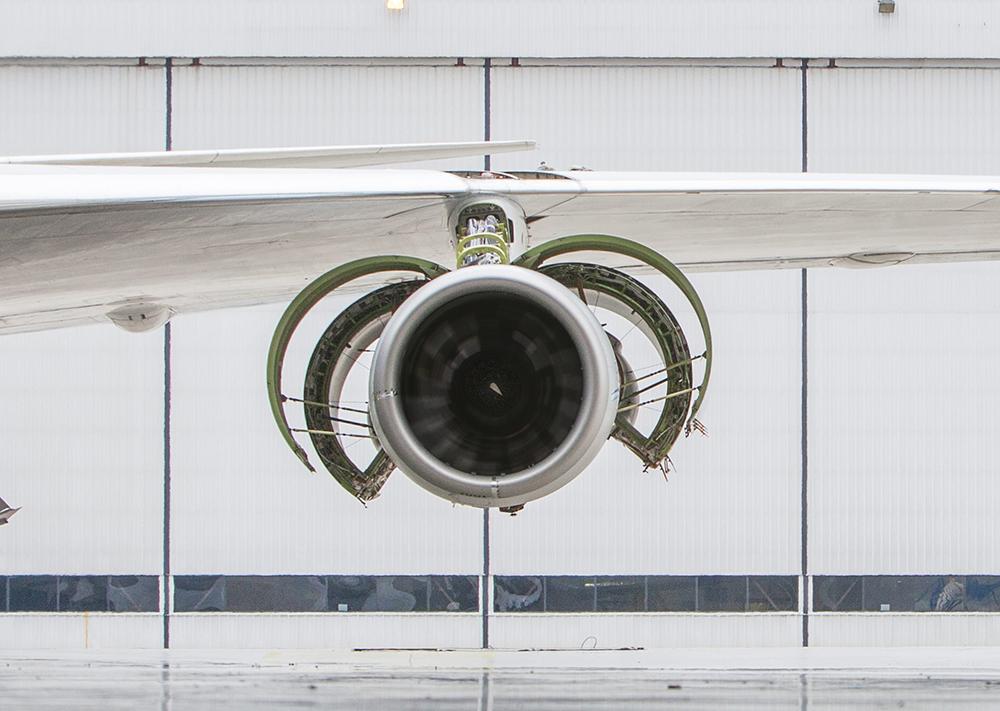
In a recent webinar, IBA’s Manager of Commercial Engines, Jamie Davey, said stress in engine overhauls is sending turnaround times up. Meanwhile, Davey says lead times—the time from initial order to delivery of the shop visit—are often six months and “in some cases a year.”
Two engine shops back up Davey’s general point, but say they are working on and expect slow but steady improvements.
David McCrory, director of AE 3007 and AE 1107 programs for StandardAero, says the company supports a wide range of platforms, from auxiliary power units (APU) and small turboprops to large fan engines. “Our turnaround times (TAT) vary widely, from 20 or more days for APUs to 100 or more days for large fans,” McCrory says. “To give one specific example, our overhaul TAT for the Rolls-Royce AE 3007A turbofan on the Embraer ERJ145 is 45 days.”
StandardAero lead times also vary widely by engine. For AE 3007s, inductions typically occur less than a week after receipt, but for other engines, “it’s not uncommon to see lead times of 30-90 days, due to current levels of demand and supply chain issues,” says McCrory.
Delays are predominantly caused by parts, not labor shortages. “A single part can cause a significant impact to TATs, especially if the part is sole-source,” McCrory says. StandardAero has internal capabilities, extensive in-house part repair and new parts manufacturing, plus engine trading and used serviceable materials, all of which help to overcome some new part roadblocks. “But on certain occasions we are reliant on the external supply chain for sole-source parts,” he adds.
StandardAero is now seeing gradual improvement in its TATs and lead times, but expects supply chain issues to continue “for several years.”
Pratt & Whitney measures total wing-to-wing time for airlines as well as TAT at shops, both of which vary according to engine model and work scope, says Kevin Kirkpatrick, vice president of aftermarket operations. Kirkpatrick declined to give figures for these metrics, but notes that wing-to-wing and TAT for legacy engines has been able to sustain fleet operations. “For GTF engines, the supply chain is under more pressure due to rapid increase in utilization, upgrades to improve time-on-wing and increased demand for new aircraft,” he says.
As with StandardAero, the chief cause of Pratt’s longer TATs is material availability. “Labor remains a challenge, but the supply chain is the primary constraint on output for the entire industry,” Kirkpatrick says.
Kirkpatrick notes the supply chain is improving and often delivering higher volumes than previously, but it is not keeping up with growing demand. Further, “TATs will lag the supply chain recovery as work-in-progress clears from the shops,” he says.
The OEM is attempting to improve matters further by embedding its staff with key suppliers, qualifying additional suppliers and assisting all suppliers with employee training. Kirkpatrick expects increased output of both new and overhauled engines later this year. However, “it will take some time to return to pre-COVID turnaround times in our MRO shops,” he says.
Meanwhile, Pratt is both expanding its GTF MRO capacity, hiring hundreds of new employees and inserting new technologies to increase efficiency. Delta TechOps’ new GTF engine overhaul facility, which opened in February, will increase capacity to more than 300 shop visits per year. Kirkpatrick says Pratt also plans to hire 700 more employees in 2023.