
The paint industry continues to develop lighter-weight, more durable and faster-drying coatings for aircraft applications as airlines and business aircraft owners insist upon faster turnaround times in the paint shop—and less environmental impact.
In the past, airlines mainly used a single-stage application process in which one coat of paint was sprayed over a primer, according to Julie Voisin, global marketing manager for Sherwin Williams Aerospace Coatings in Wichita. Now, she explains, the trend is toward applying a primer plus a basecoat, topped with a protective clearcoat. “The basecoat-clearcoat process has been used for more than a decade, but the commercial airlines, in many cases, still consider it a novel approach,” she says. “However, it is being adopted increasingly over what it had been years ago.”
Sherwin-Williams is focusing on three areas for aircraft paints: faster processing times; more environmentally friendly products, in the form of coatings free of chromates and volatile organic compounds (VOC); and the application of thinner films in order to save weight. As an example, Voisin cites SKYscapes, offered as a basecoat and clearcoat, and designed to enhance productivity.
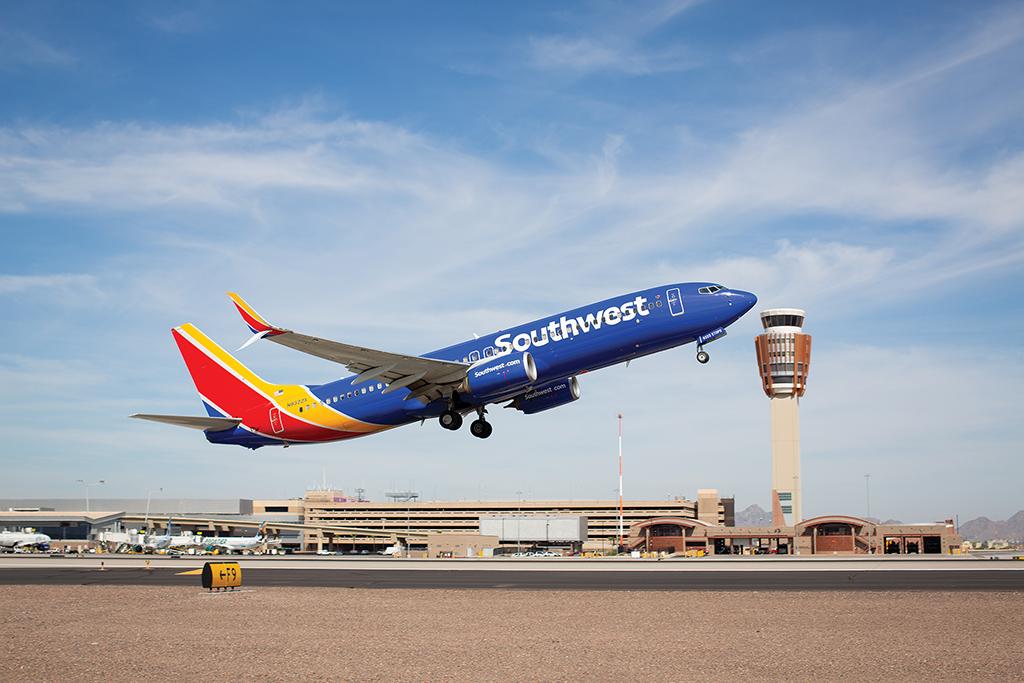
“With SKYscapes, paint processing times have been reduced by 30%, because the paint cures or reaches its optimum hardness at ambient temperatures in half the time of other single-stage systems, which can take as much as 6-10 hr.,” Voisin explains. “That means less time—and cost—in the shop, meeting customer demand for faster turn times. SKYscapes is ideal for aircraft paint schemes with multiple colors, stripes or elaborate designs, which are very time--consuming.” She adds that it also incorporates improved film thickness for greater weight savings.
Reducing the weight of coatings has, in fact, long been on the aerospace industry’s radar and remains a top priority, reports Sam Millikin, global platform director for coatings and sealants-aerospace for PPG.
For instance, he mentions PPG’s Aerocron, a chrome-free, electrocoat (e-coat) primer, used to coat structural parts by electrodeposition instead of a traditional spray process. “It also provides a more uniform film thickness on the part and can result in up to 75% weight savings on highly complex parts,” he notes.
Also spurring innovations in aircraft paint development, says Millikin, is the demand for more environmentally sound solutions, such as moving away from hexavalent chrome as well as nonylphenol ethoxylates, in order to meet regulatory mandates.
“Hexavalent chrome has traditionally been used as a corrosion-inhibitor solution in primers and pretreatments,” he says. “But there are pretreatments and primers now in use that provide the [same] needed corrosion-resistance performance.”
To do that, says Millikin, PPG has “innovated multiple strategies” that include special forms of environmentally friendly alkali earth, rare earth and transition metal compounds to replace chromium.
“The particular choice of these additives depends on their ability to meet the different specification requirements and full compatibility with a given paint system and its application,” he remarks. “Lowering the use of solvents within aerospace coating products and moving toward water-based technologies is another initiative picking up steam within the industry, due to the growing concerns [about] emissions and volatile organic compounds.”
As an alternative to current chromate wash primers, says Millikin, in 2014 the company introduced PPG Desoprime 7530, a chrome-free wash primer that can be applied with electrostatic spray equipment.
Asked about productivity developments in the paint application process, Millikin points to electrodeposition as an alternative to more time-consuming traditional spray coating processes. Specifically, he explains, electrodeposition coatings are applied via an immersion process that utilizes a bath with electrically charged paint particles that deposit the coating onto a conductive substrate once current is applied. Electrodeposition also includes a closed- loop tank system and a final bake to cure the coating.
“Both from an economical and part protection aspect, electrodeposition provides considerable benefits to customers,” he stresses. “This process offers the advantage of a more uniform coating thickness for complex geometric parts and faster part-handling due to thermal curing and the closed-loop system.” That, he explains, results in in a 95%+ transfer efficiency of paint.
“Spray coating, [in contrast,] uses an atomization process with a spray gun, which leads to inconsistent thickness distribution on parts, and an approximate transfer efficiency of under 40%. Primers and topcoats can be formulated for use with electrostatic as well as conventional spray equipment,” he adds.
Millikin also says that thermal curing takes only about 30 min., while spray primers typically require as much as seven days to cure fully. Parts can be coated and put back onto the aircraft more quickly, returning it to service sooner.
Aircraft paint shops are trending toward high-solid topcoats and primers that are not only more environmentally friendly but are less labor-intensive, according to Doug Bohac, director of paint operations for Lincoln, Nebraska-headquartered Duncan Aviation. “High-solid paints usually require just a two-coat application, while conventional paints require a three-coat application process,” he says. “Today, nearly all the aircraft OEMs use high-solid paints, as do about 50% of vendors specializing in airplane painting and refurbishments.”
In paint-speak, “high solids” refers to a higher concentration of resins and pigments than is the case for what are referred to as “conventional” paints. The pigments provide the color, while the resins contribute the high luster and shine. High-solid primers have at least 75% solids, by weight, in order to achieve 350 grams/liter of VOC. For the topcoat, it is generally 65%, to have 420 grams/liter of VOCs. In both cases, the remaining components are solvents. However, the composition of resins and pigments can vary, depending on the formulation and required performance.
Bohac points out that prior to painting composite surfaces, an anti-static primer must be used and applied to a specific mil (0.001-in.) thickness in order to provide lightning protection.
An increasing number of paint jobs, he explains, are specifying basecoat-clearcoat applications, although he notes that this is becoming more common for highly customized liveries in both the business jet and commercial airline worlds.
“Some business jet operators today want to have more personalized paint jobs,” Bohac says. “And you’re also seeing this for some commercial jets such as the paint schemes Southwest Airlines uses on its 737 fleet.”
The clearcoat, he explains, serves a threefold purpose, describing it as a “shell” that protects the integrity of the pigment in the basecoat. “It also provides a nice vibrant finish and it makes it easier to work with any imperfections in the basecoat after application,” he says.
In fact, Southwest Airlines does specify a basecoat and clearcoat application for its multi-colored livery, reports Tony Brown, a paint engineer for the Dallas-based airline, which contracts its painting to an outside vendor. The coatings currently specified by Southwest are manufactured by
AkzoNobel.
“The chemistry of each component [primer, basecoat and clearcoat] was not dictated by Southwest, but the suggestions we had were taken into account by the manufacturer,” Brown explains. “To name a few, they included chromate-free paints and primers, and UV protection within the clearcoat.”
Along with this, Brown notes improvements in paint technology, enabling the airline to increase the time interval between repainting.
“Originally, we painted aircraft every six years. With the introduction of a clearcoat, we were able to push that time frame to at least seven years,” he says. “We’re now looking at whether we can extend the life of the paint beyond that time period, provided the paint system is doing its job of protecting the aircraft and keeping its look within our brand standards.”