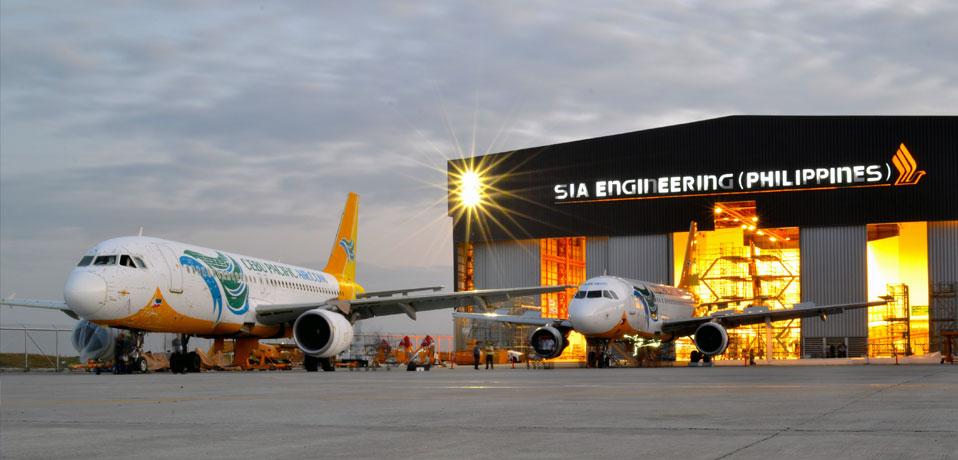
With each new generation of aircraft, manufacturers tend to promise lower maintenance costs.
They point to factors such as longer intervals between maintenance checks, fewer maintenance tasks, new materials and more durable components, as well as the power of digitization and predictive software to refine maintenance planning.
Ramón Roque, Embraer’s product support engineering director tells Inside MRO that “the lifecycle maintenance cost of newer variants takes into consideration all lessons learned from previous products”. He adds that the Embraer E2 line has a “double-digit” maintenance costs advantage over the E1 line.
But when it comes to supporting aircraft over the lifecycle, one of airlines’ chief complaints is the ever-increasing cost of parts, and the particularly severe inflation of the most popular life-limited parts.
On new-generation aircraft this problem is exacerbated by aircraft manufacturers’ growing use of single-source supply, potentially offsetting some of the cost savings promised by longer maintenance intervals and more durable parts.
“There is a trade-off: fewer manhours to fix them and fewer spare parts but the parts that are required are high cost,” says Phil Seymour, president of consultancy IBA, adding: “It’s very important to negotiate maintenance cost guarantees when buying a new-gen aircraft and ensure the warranties and guarantees are robust.”
Olof Nittinger, head of aircraft evaluation and market intelligence at Lufthansa , says: “We only get lifecycle improvements and commercial improvement if we a have a certain pressure we can build up against the suppliers.”
However, he also points out that OEMs grant exclusive supply deals for certain components to help them offer the lowest possible aircraft acquisition price to airline and lessor customers, and thus there is a balance to be struck between original equipment pricing and long-term costs.
For an in-depth look at aircraft lifecycle costs, see the next issue of Inside MRO.