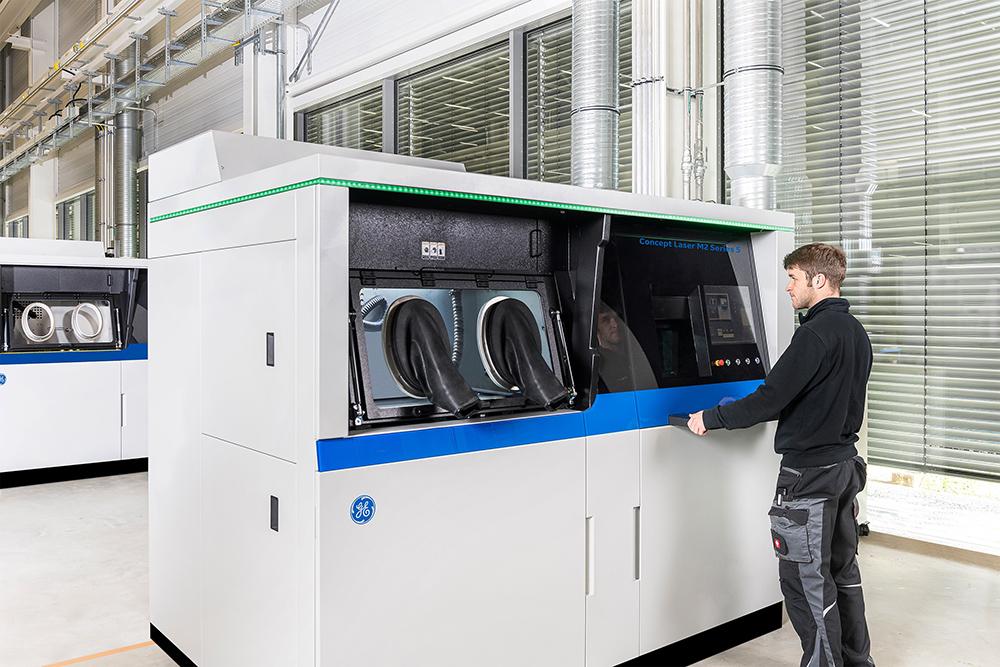
Additive repair of commercial aircraft parts has been well established, but it is still not coming anywhere near its full potential, according to points made in a recent Additive Manufacturing Coalition webinar. However, new additive tools are being developed and the additive industry is working on standards that should help accelerate adoption of these technologies.
David Ramahi, CEO of Optomec, said the company has now installed more than 100 additive machines approved by the FAA for the repair of flight-critical parts. “Still, penetration is low at 10%,” Ramahi noted.
Optomec’s directed energy deposit printers are repairing engine turbine components at companies such as GE, Rolls-Royce, Pratt & Whitney and Delta TechOps. Repairing wear on blade tips and Z notches is a typical and common use of additive methods.
Ramahi says these kinds of repairs cost up to 90% less than newly-made parts and 70% less than traditional forging fixes. They can be done up to 80% faster than traditional repairs and repay investment in 18 months, according to Ramahi. Each machine repairs 50,000-70,000 blades per year.
Each turbine blade is different, so Optomec also provides software that scans each blade, detects the needed repair and customizes a tool path to make the repair.
However, the potential for using additive to fix the wear caused by abrasion, erosion and corrosion is immense. Complex rotating metal structures require lifecycle costs 5-10 times their acquisition costs, according to the National Association of Corrosion Engineers. This amounts to about $1.2 trillion for the U.S. and $10 trillion for the world as a whole.
Jason Jones, CEO of Hybrid Manufacturing Technologies, highlights three basic advantages of additive repairs: the ability to renew, to make better than new and to offer an inside view of repaired parts.
In the age of sustainability, additive can avoid throwing out worn parts, enabling their reuse. It can improve the repaired part by adding stronger materials to the worn area. “We can triple the lifetime,” Jones stressed. Better materials can be added to the vulnerable edge of parts, or additive can even change the shape of parts to match a better design than was originally used.
Hybrid Manufacturing Technologies’ additive equipment can also deploy inspection heads that use eddy current fields to detect cracks and thus exert quality control automatically.
Dave Abbott, senior staff engineer at GE Aviation, chairs the Society of Automotive Engineers (SAE) International’s subcommittee on additive repair for aerospace, which is working on standards for using additive more widely and easily in aviation.
SAE has already developed multiple standards for controlling materials and processes for additive production. Abbott’s group is working on analogous standards for four types of additive repairs: repair of conventionally made parts, repair of additively manufactured parts, additive production of a replacement part and additive repair of a part consumed in repair.
Additive repairs create some special challenges for developing standards, including deciding on the criticality of a part—a subject that is now being addressed by an FAA-European Union Aviation Safety Agency workshop. Data must also be gathered on the performance of additively repaired parts.
Another factor that could accelerate deployment of additive would be the U.S. Defense Department, which spends $50 billion a year maintaining its equipment, adopting an additive strategy. “They have done it little by little, from the bottom up,” Ramahi said. “I’d like to see a more systematic approach.”
Jones argued that if defense or private buyers of capital equipment insisted on guaranteed uptime for their equipment in return for a steady payment—as in engine-makers’ flight-hour contracts—OEMs would lose the incentive to make and sell new parts and would seek the most efficient means of keeping equipment functioning, which he says is additive repairs.