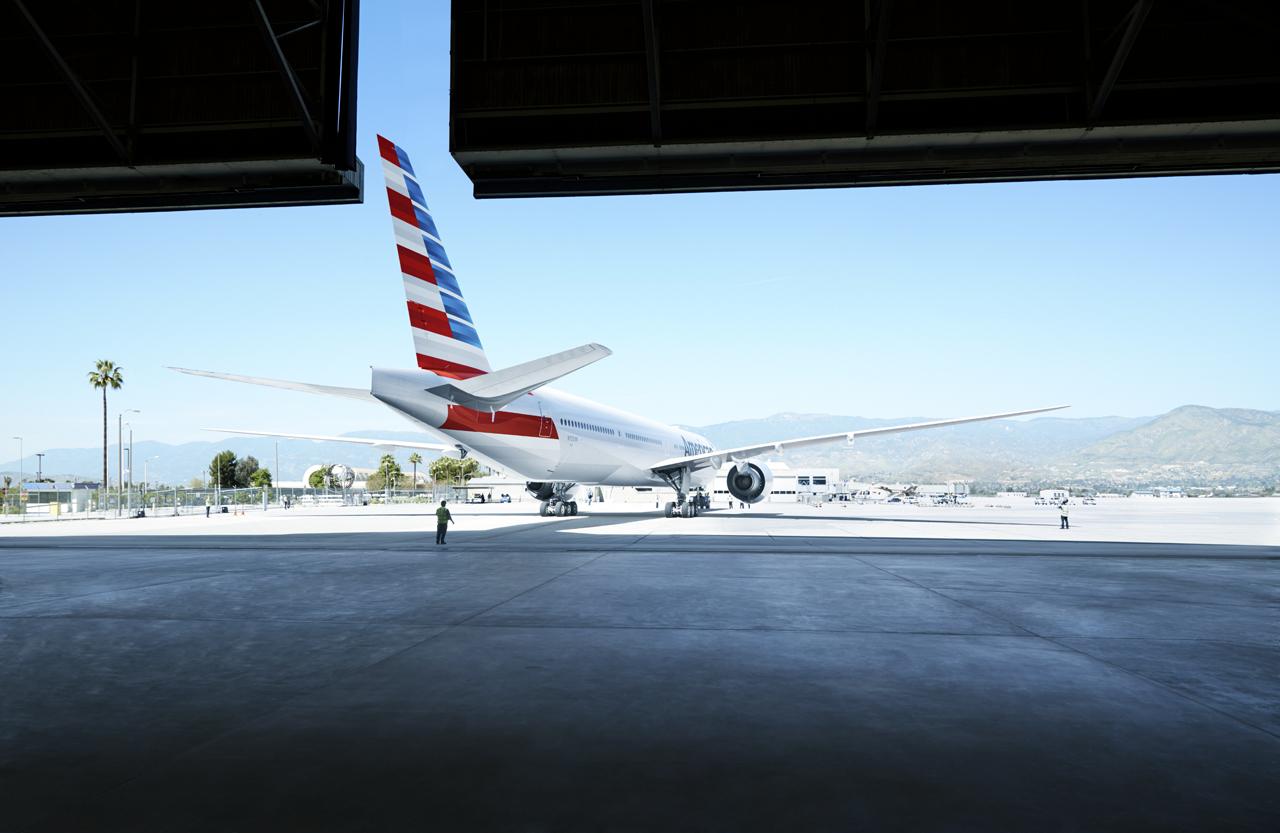
Predictive maintenance on non-engine parts is new and evolving. Major carriers may develop predictive tools in significant depth and with wide coverage. Smaller airlines may be restricted for a while at more basic levels of prediction. But whether large or small, carriers are beginning to reap significant gains.
American Airlines operates more than 450 Boeing aircraft and uses the OEM’s Airplane Health Management (AHM) tool, which gives operators faults and customized, prioritized alerts and analysis on a wide range of aircraft components.
However, the carrier goes well beyond AHM. “At American, all of our predictive maintenance is completed in-house by our predictive maintenance engineering team to reduce unscheduled maintenance,” explains Brent Kocken, manager of predictive maintenance engineering at American Airlines. This in-house predictive team was formed in 2020.
Kocken credits significant data and his team’s robust engineering knowledge for identification of adverse data trends. The team then recommends component removal before failure. Further, he notes, “by doing this work in-house, we can prioritize issues that may be specific to our fleet and operational needs.”
While analysis is done mostly by American’s predictive maintenance team, it takes other units to proactively fix aircraft. Some of those other teams include aircraft software engineering, technical services, and operations research and advanced analytics.
The aircraft software engineering team ensures that data coming off the aircraft is timely and accurate. “This team is critical to predictive success at American,” Kocken stresses.
The technical services desk reviews every predictive action for accuracy and practicality, then issues items to aircraft to be worked.
Finally, the operations research and advanced analytics team uses cutting-edge tools to accelerate analytic development by the predictive maintenance engineers.
Kocken says American’s predictive maintenance program has been exceptionally successful since it began in 2020. “In 2022 alone, we created more than 1,000 maintenance actions, leading to months of aircraft availability being returned to the operation, hundreds of avoided delays and dozens of prevented cancelations, and significant cost savings for the airline,” he says.
Kocken says American’s predictive team continues to add new analytics every month to increase the safety and reliability of the airline.
Across the Atlantic, Air Europa Lineas Aereas uses AHM on a much smaller fleet of 23 Boeing 787s, according Pedro Macias, the airline’s chief technical officer.
Air Europa’s Maintenance Control Center follows up AHM messages each day to get information about potential maintenance problems, failures or just the status of aircraft parts. “For instance, deterioration of brakes on 787s,” Macias notes. This information comes in real time.
Macias says Air Europa’s collaboration with Boeing on AHM is customized for the airline’s needs. “They try to configure triggers that alert us about a technical malfunction,” he says.
Air Europa’s main goal in using AHM is getting information on possible technical problems in real time. “Knowing the failure in real time, Air Europa can start arranging the material needed for the repair and the movement of the material from stores or other locations,” Macias explains. “Then we can, together with our Operational Control Center, start working on different scenarios for ensuring our operations and reducing costs.”