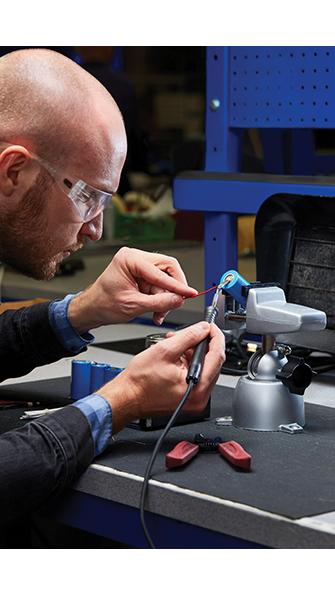
Despite progress in battery applications over the past decade, the market for aircraft batteries in 2021 remains centered on three types.
The commercial segment has long been primarily driven by nickel--cadmium (Ni-Cd) batteries, viewed as a robust option for powering systems in aircraft such as the Airbus A320 and a more popular option than valve-regulated lead-acid and lithium-ion battery types. Moves toward smaller and lighter lithium--ion batteries, deemed to be less maintenance-intensive and to have longer lives than Ni-Cd batteries, have stalled over the past decade because of concern about their associated safety hazards and higher costs.
While lithium-ion batteries are becoming increasingly common for functions such as electronic flight bags (EFB) in aircraft cockpits, their use as a main power application for the auxiliary power unit has not extended far beyond some of the newest airframe programs such as the Boeing 787.
The marketplace is dominated by several manufacturers including GS Yusa, Concorde Battery, MarathonNorco Aerospace and France-based Saft Aviation, which says it provides batteries for two-thirds of the world’s aircraft and has a network of 26 authorized repair shops.
Established MRO shops with battery capabilities also have sought to expand their offerings in the past few years. These include U.S.-based Sky Aerospace Engineering, which services new battery types at its facilities in Florida, and Duncan Aviation, which introduced mainship and emergency-power battery capabilities across 19 locations.
Although the COVID-19 crisis brought mass fleet groundings throughout most of 2020 that extended into 2021, demand for battery repair services did not slow. David Bigley, workshop manager at Satair’s UK facility close to London Heathrow Airport, which services batteries and provides warehouse distribution of spares, tells Inside MRO that grounded aircraft still require maintenance on their batteries to ensure they retain their charge. Among the largest repair specialists in the segment, Airbus subsidiary Satair handles around 7,500 Ni-Cd and lithium-ion aircraft batteries a year at the site, with volume for some 90 aircraft batteries in the workshops at any one time. It also operates a battery repair site in Miami.
Another established battery repair specialist is AJW Technique, the MRO parts-supply specialist in the AJW Group. The company announced last month that it is expanding beyond its Montreal maintenance facility with the opening of a repair base close to London Gatwick Airport. Capabilities there will include services for aircraft battery repairs, which include regular checks to carry out static reading, residual discharging, main and top charging, capacity testing, recharging, adjusting electrolyte levels and return-to-service releases. It also performs overhauls, disassembly, cleaning and temperature-sensor testing. Regular checks typically take up to five days and overhauls up to seven.
AJW Technique Europe will predominantly focus on Ni-Cd models, says AJW Technique CEO Sajedah Rustom. “There has not been a transition in the older platforms, perhaps driven by the certification issues experienced on the 787,” she says of the relative scarcity of lithium-ion batteries found on legacy programs.
Another prominent repair specialist is Aero Design/Battery Shop, the HEICO-owned subsidiary based in Mount Juliet, Tennessee, which supplies parts manufacturer approval (PMA) mainship and emergency batteries. It covers approximately 80% of the commercial fleet, including Boeing 737s through 767s, Airbus A320s, A330s and A340s, Bombardier CRJs, Embraer ERJs and ATR aircraft, with most repairs described as typical and manual.
The most common mainship battery work scope entails testing and overhaul functions based on scheduled maintenance, says Michael Montgomery, general manager of Aero Design/Battery Shop. “The capacity test determines if the battery meets the minimum capacity requirements per the CMM [component maintenance manual]. If a battery fails the capacity test, a general overhaul is typically required,” he says. “The general overhaul would include major cleaning and replacement of various bits of hardware. Any defective cells and/or temperature sensors would be replaced as well.”
Montgomery says the dramatic increase in the long-term parked fleet due to the COVID-19 pandemic led to some changes related to repair of batteries. “When bringing these aircraft back into service, our customers are asking us to test and recertify their batteries. In many cases, airlines have even chosen to scrap the old batteries and are replacing them with our new PMA batteries,” he says. “We have seen an increase in volume in both repair and new battery PMA orders and expect that trend to continue as the world recovers and more aircraft return to service.”
Repair challenges related to batteries center on several areas. One of these is undertaking the regular maintenance of batteries in an approved workshop as recommended by the manufacturer’s OMM/CMM [operation and maintenance manual/component maintenance manual], and ensuring the correct electrolyte levels, says AJW’s Rustom. “The main hazard for batteries with Ni-Cd technology is excessive heat that can lead to incidents in the event of short-circuits,” she adds.
Montgomery identifies Ni-Cd batteries themselves as “hazardous materials” that require special shipping and handling. “Ni-Cd batteries are composed of nickel, cadmium and a potassium hydroxide solution. Care must be taken in handling and storing the raw materials,” he explains.
“On top of those hazards, when maintaining aircraft Ni-Cd batteries, you must also be on guard for electrical shock and thermal runaway,” he continues. “Thermal runaway is caused when all the energy in the cell is discharged through a short within the cell. An experienced technician can identify any potential issues that might lead to a full thermal runaway event. Thermal runaway, if not caught, will destroy the cell and damage neighboring cells.”
Despite the existing challenges, Montgomery expects large commercial operators to continue using Ni-Cd batteries for the foreseeable future. “However, we are seeing lithium-ion and lead-acid batteries growing in the general aviation and business jet markets,” he notes, adding that he expects the latter trend to continue over the next several years. The market is also turning its attention to the potential of batteries for electric aircraft models.
Innovation in nickel-based batteries is also progressing, with development of lighter, more cost-efficient options due to added environmental considerations. In 2019, Saft unveiled a new ultra-low-maintenance (ULM) nickel-based battery aimed at offering longer maintenance intervals and lower total cost of ownership. Boeing contracted Saft to fit all its new 777 and 777X aircraft with the Ni-Cd battery system, which operates with a dedicated charger. The Chinese-made Comac C919 commercial aircraft also will be fitted with ULM batteries over a period of 20 years.