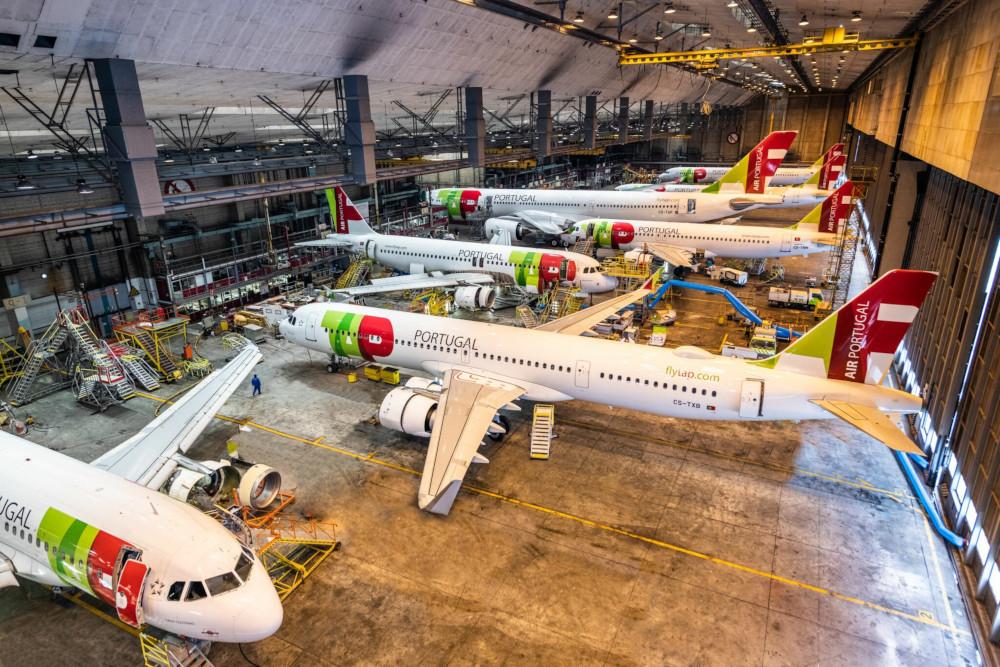
As aviation industry seeks to build momentum toward a comprehensive recovery, one of the key bottlenecks is the replacement of staff lost to downsizing during the pandemic.
In particularly short supply are skilled engineering personnel, with many having transferred to other sectors.
This is an acute problem for manufacturers, airlines and aftermarket providers, although it is also one that can be ameliorated in certain areas through digitalization, which can free up skilled workers from repetitive,time-intensive tasks.
Automated damage recognition is one example of how technology can help; another is predictive maintenance to avoid unscheduled removal and increase time on wing.
“The pandemic was a key driver for many airlines in the world to invest into digital solutions, which will enable them to become more efficient and lean going forward with less staff or the same staff with a growing fleet,” says Mia Witzig, head of digital solutions: predict & recommend, Lufthansa Technik, in an interview with Inside MRO.
Lufthansa Technik offers predictive maintenance via its Aviatar platform, which it claims helps up to 30% of unscheduled removals.
The MRO provider developed many new predictors during the crisis, including for the bleed and pneumatic systems on the Airbus A320neo and on Boeing 737 APU and hydraulic systems.
Looking ahead, it is developing other predictive aids for the A320neo, 787 and current-generation A320, although Witzig notes that the proliferation of sensors on newer technology aircraft provides the most scope for delivering data-driven solutions.
“With a full-flight data stream of an A350, for example, you can easily rebuild the behaviour of the components during the different flight phases,” says Witzig.
For an in-depth look at how attitudes to predictive maintenance are changing in the wake of the pandemic, see the next issue of Inside MRO.