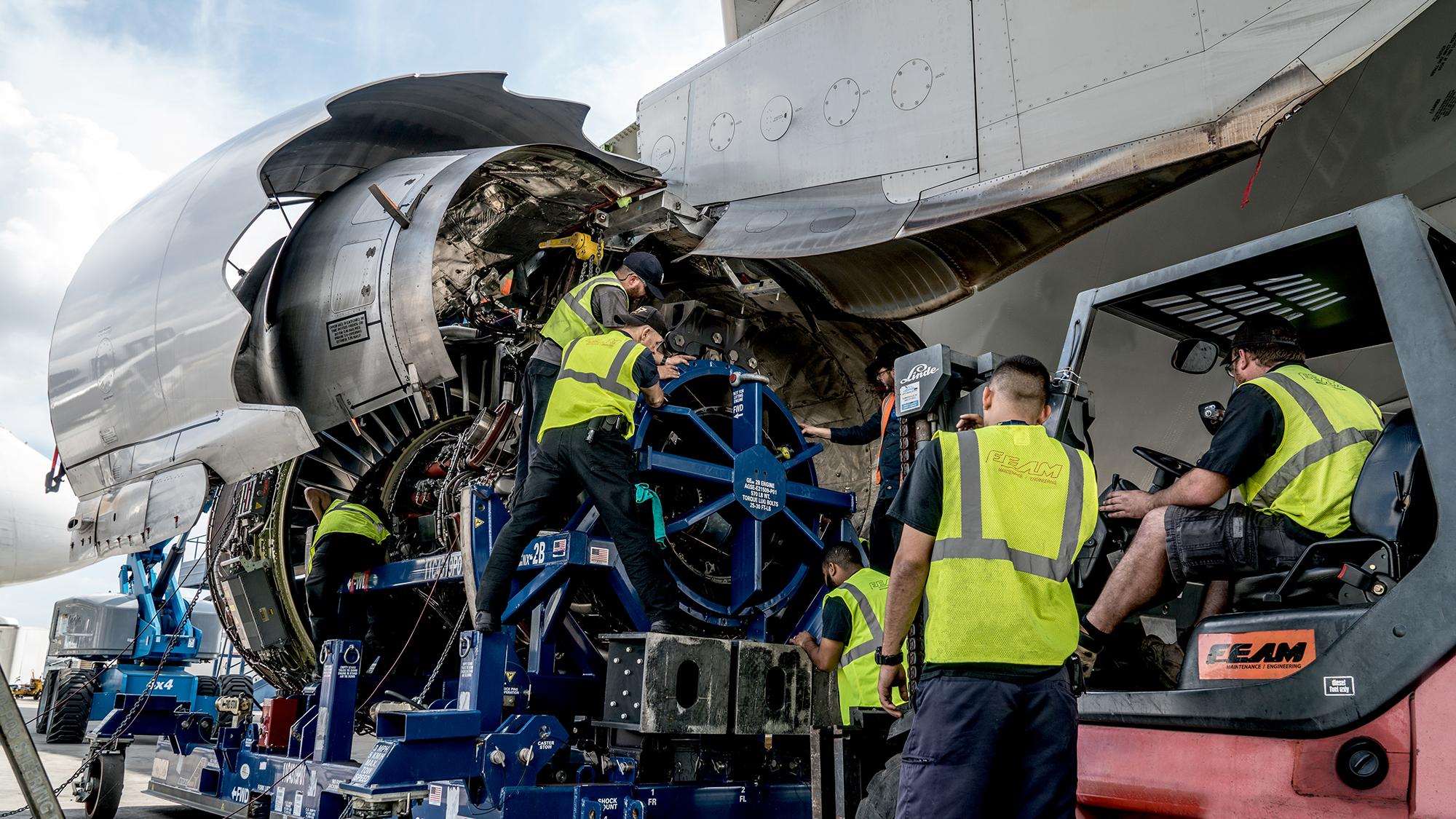
FEAM is implementing several new technologies to make aircraft maintenance more efficient—particularly as the MRO industry faces a qualified workforce shortage.
The line maintenance provider has purchased several Microsoft HoloLens 2 augmented reality (AR) devices to use for a new virtual tech assistance program with customers. While wearing the AR smart glasses, FEAM’s on-wing technical staff are able to share real-time views and collaborate with remote experts on troubleshooting issues.
“Even though we have other smart devices technicians can use like tablets and phones, the smart lens is safer and just a much better, easy way when you’re working with experts to be hands-free and actually work on the aircraft,” says Chris Stanley, director of technical services, FEAM.
While collaborating through the AR technology, Stanley says remote experts can deliver technological data to on-site technicians, who can then paste and pin highlighted schematics, wiring diagrams and illustrated parts in place. He notes that the technology can help bridge the gap between newer, less-experienced technicians and the long-time workforce the industry continues to lose through retirements.
“Everybody has a school of thought toward sustainment. To me, I’m about sustaining the expertise in the industry,” says Stanley. “Whether it’s going to be technicians, non-destructive testing inspectors or engineers, if you look at the [industry workforce] data, it shows that you’ve got the expertise exiting while at the same time you have a workforce you have to keep building around shortages.”
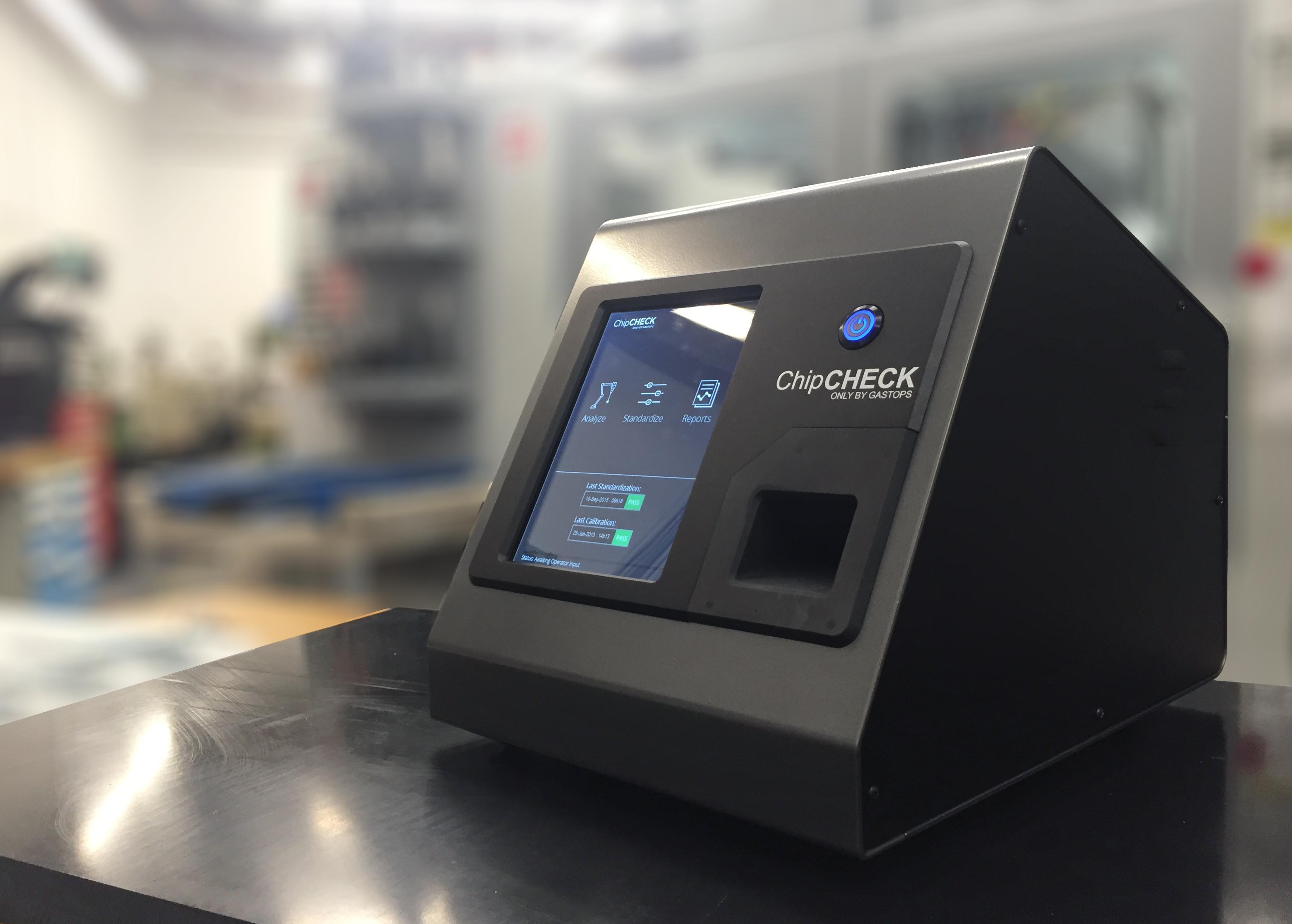
Gastops' ChipCHECK device is one of the new technologies being implemented at FEAM.
To further build its maintenance technicians’ expertise, FEAM is also partnered with Boeing to implement advanced Charlie Works Training on advanced technologies, tools and procedures for aircraft maintenance. Stanley says its AOG team and around eight of its line stations are receiving Charlie Works Training, with that number continuing to expand in the future.
“The aviation industry is on a very fast pace to modernize fleets, and technological advances are leading to major changes in how modern aircrafts are maintained and repaired,” he says. “This innovation is resulting in a large-scale paradigm shift in flight and maintenance operations, and FEAM continues to revolutionize MRO and share value-adding emerging technology to support our customer base.”
FEAM’s line maintenance teams have also implemented Gastops’ ChipCHECK, a portable device that uses alloy identification spectroscopy technology to analyze metal debris from engines to quickly determine wear and tear on engine parts. Stanley says ChipCHECK is able to analyze engine debris in minutes, so FEAM is able to avoid days’ worth of delays from waiting for laboratory results. While FEAM currently has the ChipCHECK devices positioned in specific locations, Stanley says the units are portable so they can be shipped within 24 hr. to any location.