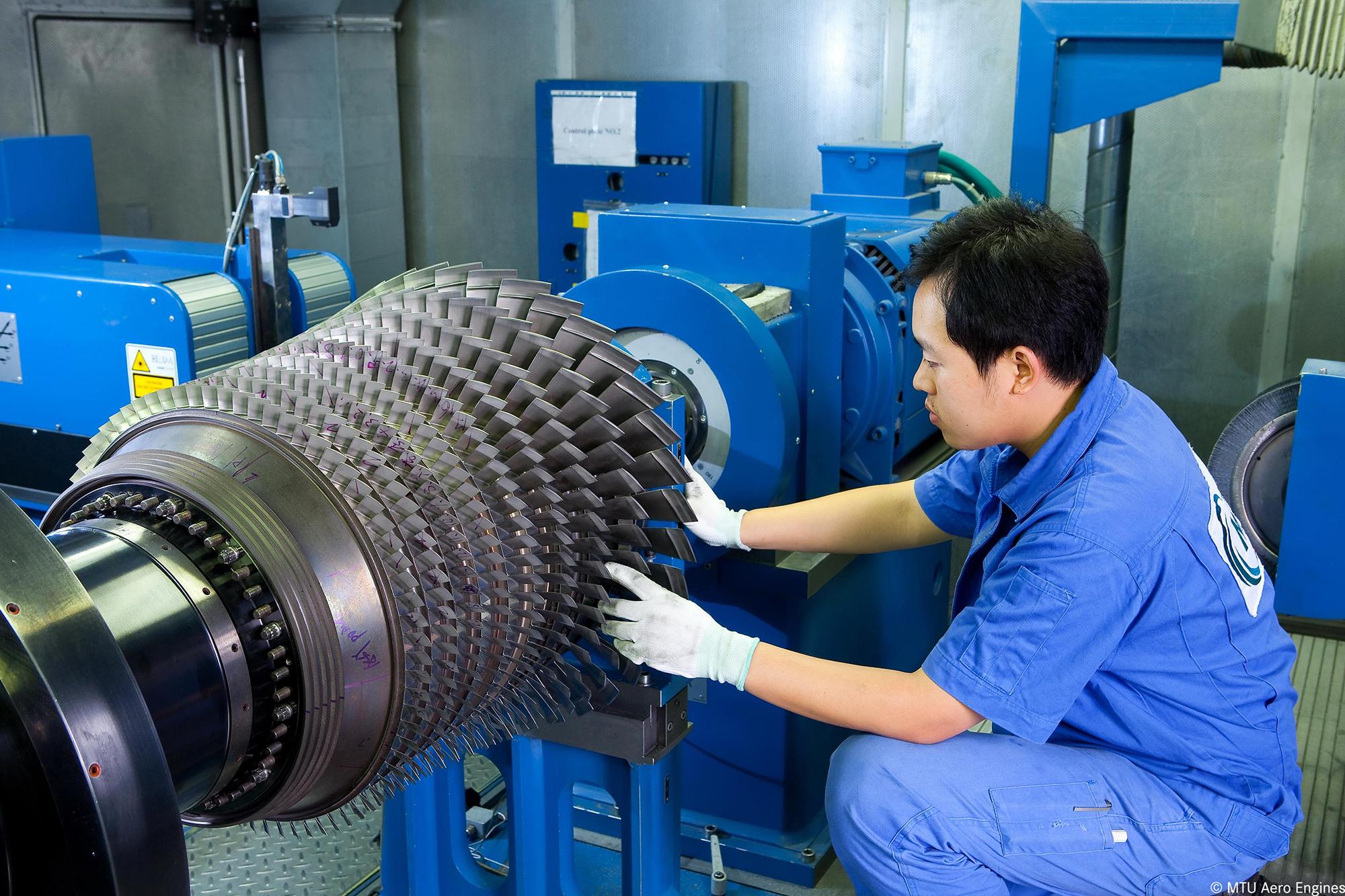
DALLAS—While engine MRO demand plunged during COVID-19 as passenger operators delayed overhauls due to parked aircraft and cash conservation efforts, some MRO companies used the time to improve their facilities and add capabilities. This helped adjust to market needs and prepare for what they see post-recovery.
For instance, BP Aero invested $2 million in capital expenditures and site expansions. One of the largest chunks, $700,000, was devoted to expanding its facility at Dallas-Ft. Worth International Airport. The new fourth facility will become home to BP Aero’s engine disassembly and parts trace identification. By moving disassembly out of its existing spot at DFW, BP can expand its “hospital shop” services on the east side of the airport. Dennis Walsh, BP Aero president and CEO, speaking at Aero-Engines Americas, says these smaller work packages have been instrumental to return aircraft to service. This has been a growing area of the business along with lease returns.
The company now has 200,000 ft.2 at the airport.
It also purchased a high-speed grinder from KLM for use in engine core work, says Walsh. Other equipment purchases included items such as a borescope, 4D digital inspection tool and BalanStar component balancing tool.
In addition, it spent about $265,000 on quality management improvements for its enterprise, he adds. It used the downtime during the pandemic to earn ISO 9001:2015 and AS 9110 certification.
Likewise, MTU proceeded with facility and capability expansions around its global network. “We saw others were downsizing and we wanted to be ready for the uptick when it happened,” says Les Cronin, MTU Maintenance senior director of sales for the Americas.
It is in the process of moving its Canadian site from Richmond, British Columbia, to a new nearly 250,000 ft.2 shop at Boundary Bay, a Vancouver suburb. The move started in May 2020 but is still progressing as it shifts the work from facility to facility. The larger space allowed it to add GE CF6-80 and F138 engine MRO capabilities.
MTU Maintenance also expanded its Hannover, Germany facility by 200,000 ft.2 last year, added a new logistics center and is expanding its on-wing support for hospital visits at Berlin-Brandenburg. It also opened its Engine Maintenance Europe (EME) Aero shop in Poland for Pratt & Whitney GTF engine MRO. That facility is a joint venture with Lufthansa Technik.
MTU Maintenance also plans to open a component shop in Serbia mid-2022 that will have capabilities to feed its network, says Cronin.
In Asia, it is expanding its Airfoil Services (ASSB) JV compressor blade shop in Malaysia and is greatly expanding MTU Zhuhai, a 50/50 joint venture between MTU Aero Engines and China Southern Airlines. MTU Zhuhai is getting an additional 450,000 ft.2, which will allow it to add CFM Leap 1A and 1B maintenance capability, and it plans to build a second facility in nearby Jinwan for Pratt & Whitney GTF engines. That facility, targeted to open in 2024, will include a 65,000-lb. thrust test cell.
Cronin says MTU is now starting to get the first GTF engines in for performance restorations, which will be done at its Hannover, EME Aero and, soon, Zhuhai facilities. He says the turnaround times will be a little slower than ideal because of supply chain issues. “The whole supply chain is struggling to ramp up at the moment,” he adds.
This is part of the reason it is bringing more repairs in-house. “During the boom pre-COVID, we tended to send out more (repairs) to external vendors and now we’re bringing them back in,” to control supply chain pressure points, says Cronin.