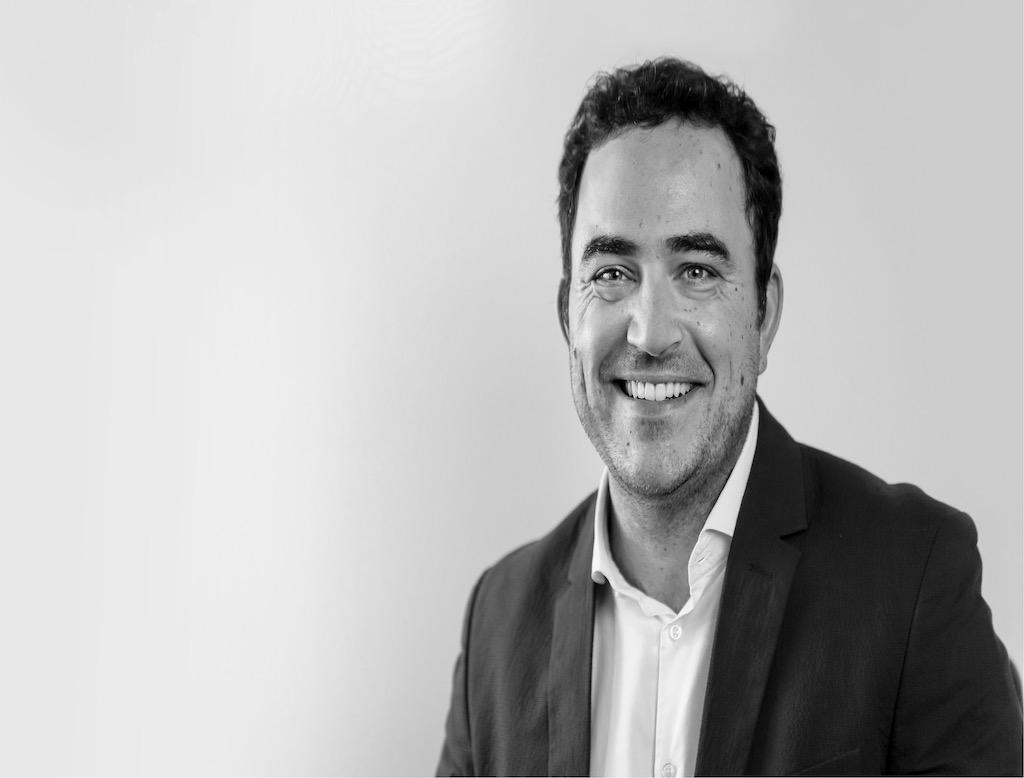
Vincent Carvalho
Vincent Carvalho, regional president, Asia-Pacific, Japan, Middle East and Africa, for IFS discusses what IT investments he sees MROs in the Asia-Pacific makings.
1. How will cloud technology help MRO processes?
The main advantage of having MRO IT software in the cloud is flexibility. In the cloud, airlines and MROs pay only for the resources they are using, and they can ramp up and down system resources almost at a moment’s notice. At the height of the of the pandemic with a majority of their global fleets grounded, carriers with cloud systems were able to ramp-down their cloud resources, reducing costs significantly. As air travel gradually increased, these carriers were able to increase cloud resources to keep pace. Airlines with physical hardware and their own servers did not have that option.
Furthermore, on-premise systems, maintained by local IT departments, often lag in terms of critical updates and patches to the underlying technology stack. In the cloud, the latest patches and security updates are always being installed, which reduces system vulnerabilities.
Cloud typically switches expenses from CapEx to OpEx, which can significantly reduce upfront expenses when embarking on new system deployments or system upgrades. OpEx can even have favorable tax implications based on the jurisdiction.
Finally, with cloud-based MRO solutions, organizations can quickly capitalize on new embedded technologies, so they better automate and optimize processes—simply by switching on new innovative capabilities when the business time is right. This makes it practical and affordable for MRO customers to quickly take advantage of technologies such as machine learning, augmented and mixed reality, artificial intelligence and the Internet of Things.
2. What is your artificial intelligence and data analytics research and development like?
Today, in collaboration with our client Rolls-Royce and their Blue Data Thread digital strategy, IFS uses AI to support airline customers to update predicted maintenance deadlines for every life-limited components inside Trent engines.
The IFS aviation maintenance solution enables the automated provision of field data, to ensure that Rolls-Royce receives timely and accurate information on its Trent 1000, Trent XWB and Trent 7000 engines. IFS aviation maintenance software then acts as a gateway to automatically push maintenance program changes from Rolls-Royce back to the airline operators. As a result, life-limited engine part maintenance deadlines are updated based on actual operating conditions and life consumed by each engine in use.
3. How will these technologies help MRO processes?
The IFS aviation maintenance solution uses a multivariable predictive maintenance forecasting algorithm, based on an amalgamation of data from Rolls-Royce and the airline, to provide the airline planning team with accurate information about their fleet and how to safely and efficiently manage their engine maintenance needs.
IFS is actively exploring wider opportunities around data collaboration and predictive maintenance with other industry players.
4. What gaps in areas of computing and digital services do you see in the APAC region?
The single most important trend is the drive towards increased digitalization to enhance competitiveness while reducing cost, offering a reduced and reliable turn-around time and the ability to offer differentiated services such as real-time visibility into work completion.
MROs in Asia-Pacific are either adopting advanced digital solutions for the first time or are replacing outdated digital solutions that are no longer supported, are expensive to maintain and are not able to support evolving business models.
At a high level, IFS has observed that Asia-Pacific MRO organizations recognize that aging IT systems act as barriers to digital transformation.
5. What specific IT investments are MROs in the APAC region making?
While less exciting than developments such as big data analytics, a major priority for these businesses is replacing core MRO systems, many of which are legacy MRO solutions built on generic enterprise resource planning (ERP) systems that were implemented 15-20 years ago. More specifically, MROs are investing in three major areas:
Advanced production planning & control capabilities: managing a knowledge repository of business rules, prior experience and best practices. Optimization tools are being investigated to reduce turnaround times and non-productive effort through the identification of resource bottlenecks and active critical path management.
Technician productivity tools: including mobility solutions for point-of-maintenance work capture, electronic signatures for paperless execution and augmented reality for remote assistance.
Customer engagement capabilities: adoption of customer portals for real-time updates, progressive billing and approval workflows, as well as integration capabilities for work package and task details.