
Nicolas Takahashi, Viva Air’s director of engineering and maintenance, spoke with Lee Ann Shay on the sidelines of MRO Latin America about the Colombian LCC’s big growth plan and technology investments. Takahashi joined Viva Air in its start-up process and is known for having reduced maintenance costs while increasing productivity.
How many additional aircraft does Viva Air plan to receive in 2020 to accommodate growth? CEO Felix Antelo recently said he hopes the carrier will transport 7.2 million passengers in 2020, compared to 6.3 million in 2019.
We target four new aircraft, but in the next three years we hope to receive 35 new neos from Airbus plus the 15 new A320ceos received to date, for a total of 50 aircraft. These aircraft have more density, 188 passengers, so by adding these aircraft and increasing our operation we can reach those numbers.
How do you handle maintenance for your Airbus fleet? What is done in-house?
We perform line maintenance in-house and up to A checks. We have two main bases in Colombia—Medellin and Bogota. We outsource line maintenance in Peru to Avianca, and we subcontract the C checks. We subcontract outstations in Colombia to Avianca, and in Peru we use a mix of suppliers, including Avianca.
For components, we have a power-by-the-hour agreement (PBH) with Airbus for the new fleet and a PBH for the older fleet with AFI KLM E&M. For engines, we just signed a 12-year, $3.2 billion contract for maintenance of the neo engines with CFM. We are launching an RFP (request for proposal) for the ceo engines. That one would be of 12-year duration, too. We hope to bid and close that by June.
What turnaround times does Viva Air strive for between flights?
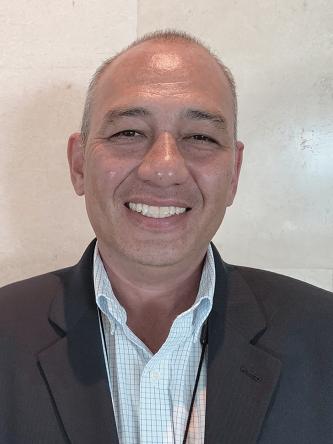
Our average turnaround time for domestic flights is 30 min., but international can vary between 40-90 min.—with most closer to 40 min. But the U.S. takes more time due to TSA. Our turnaround is quick so we can increase the number of operations.
The new aircraft have wider aisles so we can offload and load passengers quicker, which also helps with the short turnaround times. We also have good coordination with the ground personnel and crew before aircraft arrive, which is a key point of the operation.
Right now, Viva Air has the second-highest on-time performance in the region, but we perform a lot more cycles with shorter turnaround times. If we adjusted the measurement to compare apples to apples, we would be first in the region.
How does maintenance contribute to this punctual performance?
Maintenance performs everything that is planned, and we do it on time. So preparation is key. Doing this increases the availability and reliability of the aircraft, which helps the on-time performance. We also prepare for the high season as best was we can in advance.
How do you expect Viva Air’s maintenance department to change over the next few years?
We need to invest in the infrastructure and people to meet growth. We are working to have a training facility and new software systems. A predictive maintenance system will be set up in the near future. We signed an agreement with Airbus for Skywise in 2019 and are waiting for new maintenance software that can interface with Skywise—the current one does not. Predictive maintenance is the future.
Which software system are you looking at?
We are looking at all of the leading ones including TRAX, MXI and AMOS. We hope to make a decision by the end of June.
How difficult, or easy, is it to find qualified maintenance personnel?
Colombia has a population of 50 million and is quite young. Getting people is manageable and training is a key issue in keeping them at the highest level possible. It’s more difficult in Peru because there are no technical schools or universities with aviation maintenance. Maintenance technicians there also move to higher paying jobs in mining and shipping.
News reports have said Viva Air is investing in new technology. Is any of that for maintenance?
Viva Air is investing in a lot of technology for operations. We have a new simulator in the region for pilots and maintenance technicians. We are also looking at a new maintenance training facility in the first half of the year. One of the challenges for maintenance, as I mentioned before, is our maintenance software.
How much of the maintenance department’s operation is paperless?
All of our technicians have an iPad. All of the manuals are included and updated on the iPads, so you don’t have to print manuals. Unfortunately, we need to write tech reports due to the lessors and regulatory authorities, but the future is to use paperless tech logs.
Is the Viva Air Labs innovation center working with the maintenance department?
That’s more for ground and flight operations. In the future, we could use it for maintenance.
Does Viva Air have any sustainability initiatives underway?
Viva Air has made a big investment in its fleet, which will reduce carbon dioxide by 15% and noise by 50%. We also are working on initiatives to use paper cups instead of plastic. All of the pilot manuals are integrated into an iPad, which reduces paper. We also removed as much weight from the aircraft as possible. For instance, we have two ovens now instead of three or four. The seats are lighter-weight and state-of-the-art. We also now only fill 50% of the water tanks. We use single-engine taxi and wash engines, as required. Those small initiatives add to fuel savings.
As Viva Air moves toward an initial public offering, is that process affecting your maintenance operations in any way?
We expect to be public in a few years. We need to have the best maintenance practices and the lowest operating costs as possible because that is one of our competitive advantages. Our target is to be the lowest-cost operator in the region—and one of the lowest in the world.
Viva Air Fact Box
Founded: 2012
Ownership: Irelandia Aviation
Fleet (number of aircraft, by type): 22 A320 aircraft
Routes: 33
Passengers carried (2019): 6.3 million
Headquarters: Medellin, Colombia
Maintenance base locations: Bogota, Colombia, and Lima, Peru