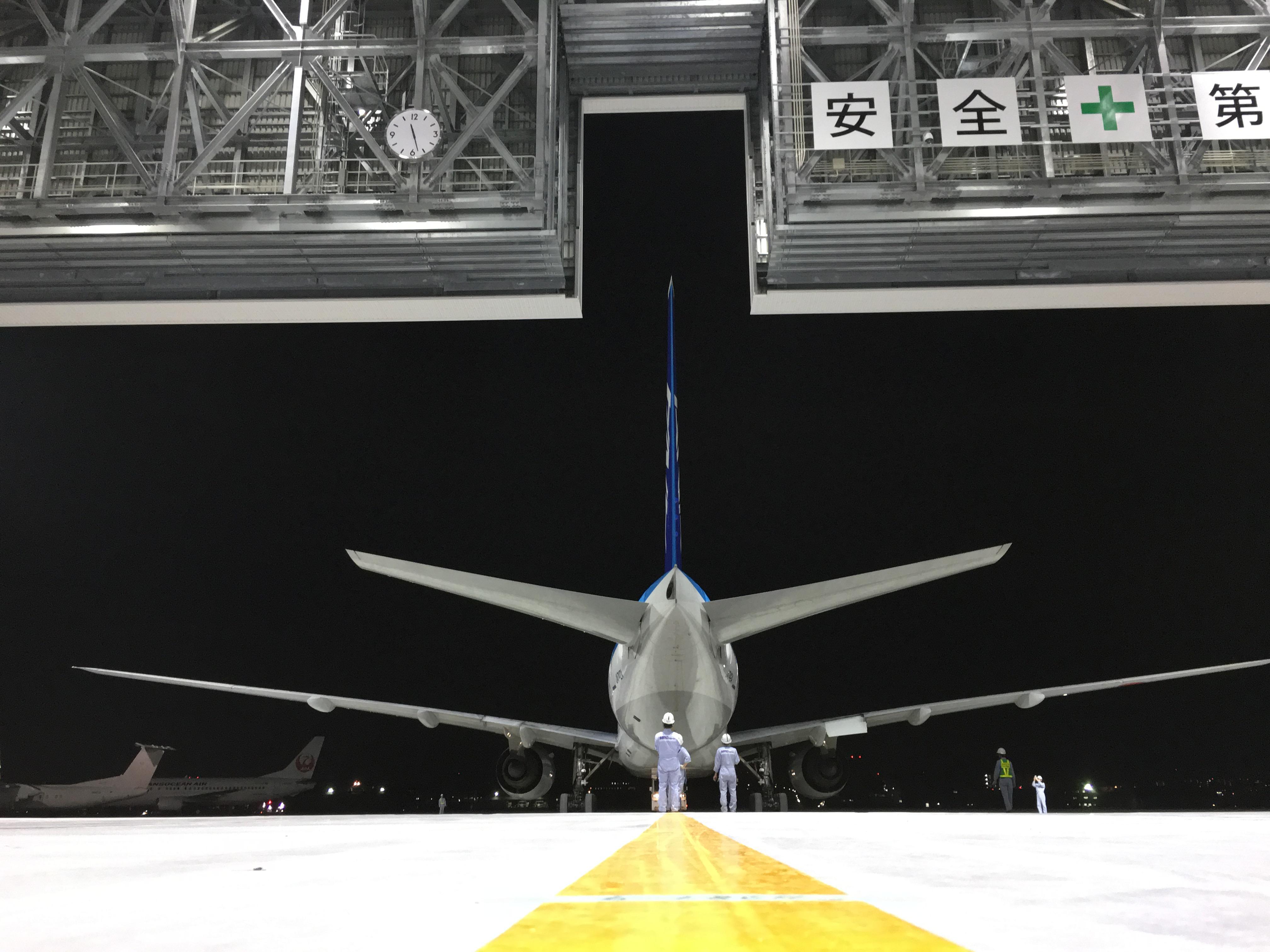
Japan’s major airlines, All Nippon Airways (ANA) and Japan Airlines, have increased their use of PMA parts over the years, but there are still significant hurdles to PMA adoption by start-up Japanese carriers and by other Asian airlines, according to Takuma Otsuka, manager of sales and marketing at MRO Japan.
Otsuka spent several decades in parts procurement at ANA and was seconded to MRO Japan in 2015.
MRO Japan, a joint venture between ANA and the Japanese government, acquired a few new Japanese customers in the past and hopes to gain a non-Japanese customer in the coming year.
MRO Japan must, of course, follow the part policies of its customer airlines. Otsuka says ANA began using PMAs about 15 to 20 years ago, starting with small non-critical piece parts. The major carrier slowly expanded PMA use to include more important parts, but ANA had been reluctant to adopt PMAs for flight-critical parts, according to his experience at ANA.
The new Japanese low-cost carriers, on the other hand, have not so far made much use of PMAs. One reason is that these LCCs have kept their engineering departments as lean and efficient as possible to focus on regular engineering tasks from a technical perspective. “It doesn’t help to hire a big engineering department just to save $10,000 on one small part,” Otsuka notes.
Another reason for LCCs’ avoidance of PMAs is that most of their aircraft are leased and are expected to be returned at fixed dates in their original conditions. “There might be a big cost saving obtaining from PMA part options, but they will have to return the aircraft in original condition, paying considerable expense for PMA replacements,” Otsuka says.
As far as Otsuka has learned, China has a process for adopting PMAs similar to that of Japan. As in Japan, Chinese approvals of PMAs depend on each airline’s ability to assign engineers to evaluate PMAs. Like Japanese carriers, he thinks “the Chinese are a bit reluctant to use PMAs.”
Because the Chinese aviation market is so big, if China increases adoption of PMAs, this would lead to major changes in the part business.
Otsuka says PMA parts have generally been about 30% lower in price than OEM parts. But OEMs have recently used their financial strength to “get closer to operators” and limit PMA use. Nevertheless, he sees the competition between PMA and OEM parts and sometimes between different PMA providers as beneficial to airlines.