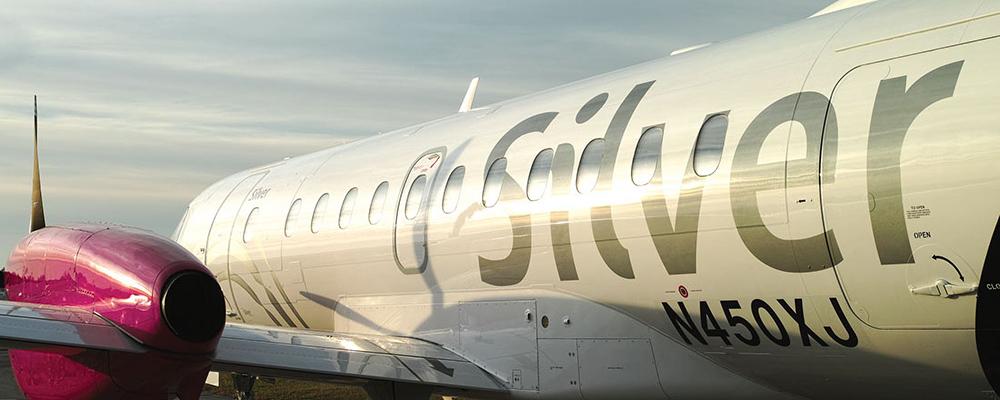
As aircraft fleets transition following the aviation industry’s tumultuous last few years, a new partnership is seeking to simplify the process of changing aircraft liveries. Paint and coatings specialist PPG has partnered with aircraft branding specialist Aerobrand to offer a combined paint supply and livery design service to airlines.
Under the new partnership, airline customers will be able to work closely with designers to create custom paint colors and schemes at PPG’s Livery Lab aircraft coatings and design facilities in Burbank, California and Shildon, UK.
“Our partnership with Aerobrand will prove invaluable for our customers on many levels,” says Sam Millikin, PPG’s global director of coatings and sealants for aerospace. “This direct collaboration between our color formulators and Aerobrand’s outstanding livery design team offers airlines a creative solution that will increase the speed and reduce the cost of these services compared to obtaining them separately.”
The service will provide cost estimates with the paint volume requirement built in, which PPG says will also lead to cost savings and reduced waste.
According to Aerobrand, which has designed liveries for airlines such as Eurowings, Lufthansa and Silver Airways, the service should also help familiarize customers with the latest advancements in paint and coating products.
“As we look to the future, there are many exciting new initiatives in the aerospace coatings world and this partnership with PPG enables us to offer our clients in-depth knowledge of these technologies and their real-world application,” says Aerobrand CEO David Hedley Noble.
Some of these new technologies include PPG’s solar heat management coating, which uses infrared-transparent stainers that allow solar heat to pass through topcoat pigments to a white primer coat. PPG says this reflects heat away from the aircraft, keeping it up to 25% cooler when using darker colors and reducing interior cabin temperatures by 5-7 degrees.
PPG has also developed new products aimed at improving sustainability and performance. These include lighter weight, chrome-free primers that are applied in a bath instead of via a spray method, which PPG says has higher transfer efficiency and helps to lower overall fuel consumption. It has also developed a basecoat/clearcoat system that it says offers longer durability, which reduces the need for aftermarket maintenance.
To further support airlines’ aftermarket paint and coating needs, PPG recently announced plans to build a $17 million aerospace application support center (ASC) in Toulouse, France. The center, which will be PPG’s 17th, is expected to begin operations in the fourth quarter of 2023. The facility’s capabilities will include laboratory and shop areas for paint and coating development, qualification and blending, as well as a spray booth for hands-on training, filling lines for touch-up kits, a transparencies inspection cell and other customer-focused areas.
“Our ASCs service their local customers with sealants, coatings, application equipment and repackaging of sealants and coatings for right-sized application. The ASCs play a role in supporting both large, commercial OEMs and aftermarket maintenance of aircraft,” says Millikin.
PPG is also ramping up its manufacturing output to meet growing demand for its commercial aerospace aftermarket products. This will include investing in more factory automation to improve delivery times. While announcing plans to increase output last month, Dan Korte, PPG’s global vice president for aerospace, said: “We’ve benefited from year-over-year improvements in the market. As travelers continue returning to the skies, we are focused on meeting the immediate and longer-term needs of our customers.”