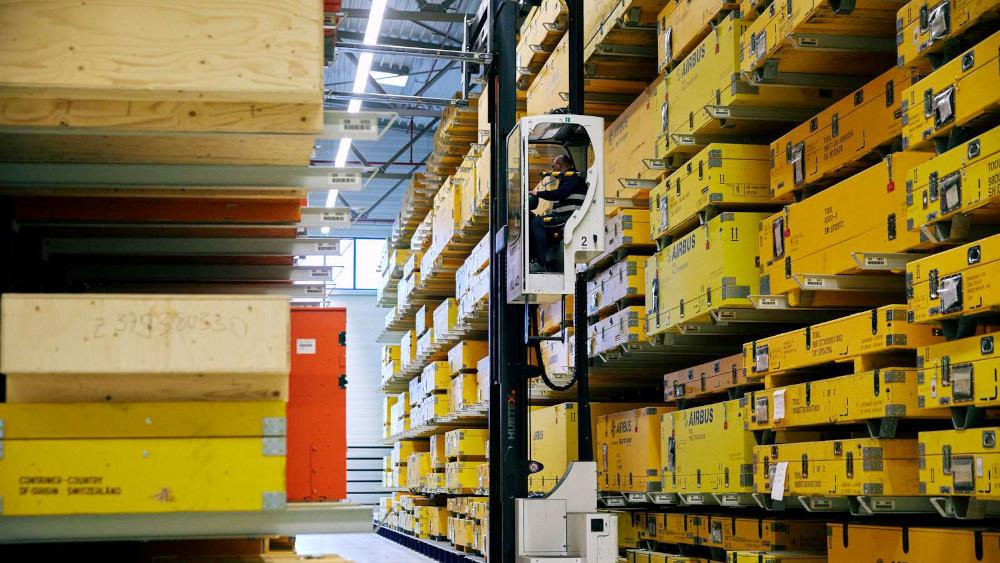
Under pressure to meet rising aircraft production rates, engine OEMs are prioritizing their airframe customers, resulting in shortages of certain parts for MRO providers.
As engine overhaul and other maintenance activity picks up around the world, so does demand for materials—new and used—to return equipment to service.
However, bottlenecks in the supply chain, particularly for forgings and castings, are creating tensions between the aftermarket and new-build protection.
Under pressure to meet rising aircraft production rates, engine OEMs are prioritizing their airframe customers, resulting in shortages of certain parts for MRO providers.
“Engine shops are finding it somewhat difficult to meet demand as one factor is the low rate of production in casting and forging facilities that make new airfoils and other parts of the engine. OEMs have been shifting the supply of all the newly manufactured airfoils to build new engines rather than send them to engine shops for repair,” notes IBA’s Jamie Davey in an article for Aviation Week's Engine Yearbook.
Another impact of shortages is that new parts prices are, in some cases, rising beyond the traditional annual escalation, with these increases being passed onto MRO customers.
“It has been reported to IBA that shop visit costs are currently escalating at 10% annually,” says Davey.
Davey also notes that the used serviceable material market is set to grow over the next few years as airlines and MROs seek alternatives to the short supply of new parts, a trend that will also boost demand for parts manufacturer approval parts and designated engineering representative repairs.
Another solution is green-time engine leasing. “Lessors are positioning themselves well for the uptick in demand for green-time engines as engines start to go into shop as the summer season ends, and as operators work to avoid any unnecessary expenditure as they continue to weather the storm from COVID and looming recession,” says Davey.
For a full insight into engine market trends since the pandemic, see the Engine Yearbook 2023, out very soon.