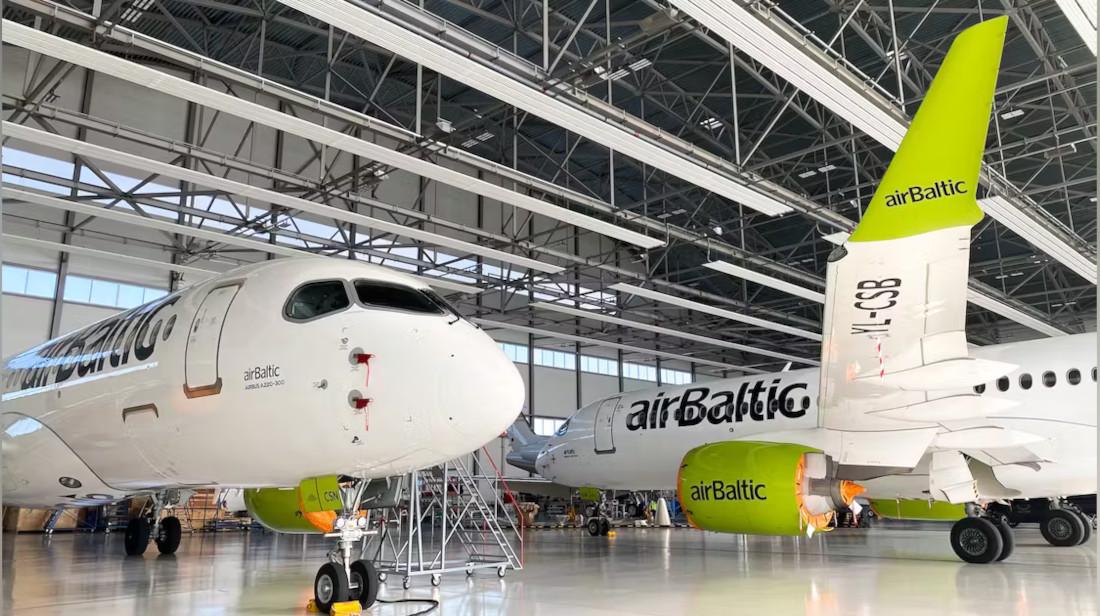
Maintenance cost planning must often balance near- and long-term priorities, setting the price of individual maintenance events against the cost and value of an aircraft or engine asset over its entire life-cycle.
Most airline technical teams will insist that life-cycle planning is their foremost concern, but in recent years many operators have had to consider more pressing financial requirements as they seek to recover from the damage of the COVID-19 pandemic.
“We still see many airlines looking for flexibility. Whilst the majors are reporting great results, there are many more airlines that have to think short-term as they repay loans and remain short-term cash focused,” says Phil Seymour, president of consultancy IBA Group, in an interview with Inside MRO.
One such airline is Riga, Latvia-based Air Baltic. “Everyone is still affected and trying to fully recover from the consequences of the pandemic and the war in Ukraine,” notes Oskars Zalkalns, vice president of engineering at the airline.
An easy way to cut costs quickly is to reduce workscopes during shop visits, thereby saving on labor and materials, albeit at the expense of shorter on-wing times—and of kicking the can down the road for a more expensive MRO visit in the future.
Many airlines have also opted to change the type of work performed for big-ticket items such as engines, as IBA’s Seymour explains: “A scheduled full overhaul and life-limited parts (LLP) stack replacement tended to become a repair with targeted LLP replacement in order to reduce the cash expenditure. But that will result in a premature next shop visit, since the build standard will have been reduced. The long-term cost per hour/cycle will have increased but the short term-cash saving was the priority.”
For a full analysis of airline maintenance cost planning, see the next issue of Inside MRO.