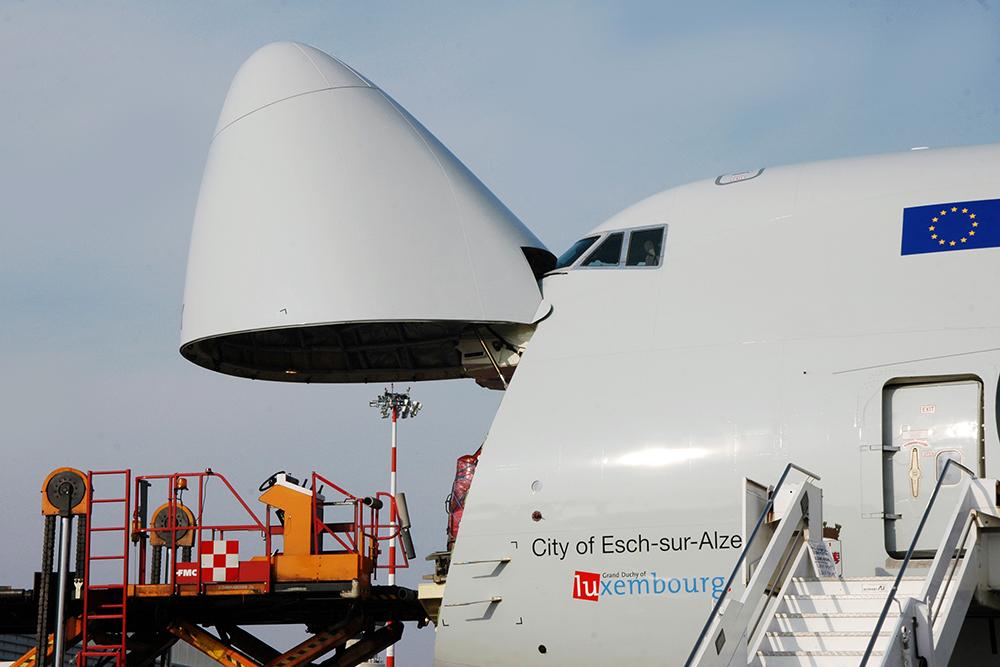
Times are challenging for supply chain managers, from the top of the aerospace pyramid to the base. According to aftermarket stakeholders, relief will only come slowly.
For example, Boeing Global Services continues to work with an unpredictable supply chain as some suppliers and their sub-suppliers experience problems caused by the pandemic, mostly due to government lockdowns or delays in shipments to or from hard-hit regions. A spokesperson says the OEM is working on contingency plans to mitigate risks. Meanwhile Boeing is monitoring the situation.
Barry Swift, procurement director for the AJW Group, can feel Boeing’s pain and that of the entire industry. “The supply chain in commercial aviation has gone, and continues to go, through the most challenging of scenarios possible,” says Swift.
Two years of low aviation volumes, cost-cutting, inventory reductions and resetting logistics have set up the “perfect storm” as COVID-19 restrictions ease and aviation volumes start to recover, Swift argues. Plus, he says, some suppliers are still short of staff due to COVID-19 infections and supply chains must be constantly adjusted as the shortage in air freight makes some prior options unacceptably tardy.
In addition, COVID-19 created semi-conductor shortages, which affect many components from air data inertial reference units to the humble anti-collision beacon, “both of which use integrated circuits,” Swift notes. In 2017, Swift says it took 17 weeks for the average order for a semi-conductor chip to be filled. Now the lag is 26 weeks, causing massive disruption across many sectors, including aviation.
Labor shortages reflect changes in labor markets—some temporary and some more enduring. Swift believes workers are “re-scoping their lives,” changing the industries they wish to work in, the places they want to work and what they consider acceptable commutes. Two years of working from home has reset expectations and challenged recruiters, and there has been at least a small shift of staff out of aviation into less volatile sectors.
Swift believes it could take 12-18 months for semi-conductor issues to be fully resolved and 24 months for office teams to be rebuilt and staff to become fully effective. Furthermore, “the logistics-related issues mentioned above have no end game in sight, and a 36-month recovery would not be too extreme a forecast,” he adds.
Erik Goedhart, global head of aerospace at Kuehne+Nagel (K+N), agrees with Swift on aerospace supply chain problems originating in both suppliers and in logistics. He cites Raytheon’s recent report that labor shortages are a major challenge in aerospace manufacturing as just one indication of supplier problems. Suppliers facing these labor challenges are now being called upon to support Boeing and Airbus plans to produce aircraft in 2022 at nearly pre-COVID-19 levels.
On the logistics side, both sea and air freight have faced difficult times. For example, by late January more than 70 container vessels were waiting to be unloaded at Los Angeles and Long Beach docks. “The next challenge is once they are unloaded, there is only one trucker for seven containers,” Goedhart notes. K+N has developed a digital tool, Seaexplorer, to predict how many ships will wait at ports and how long they will wait.
The shortage of aircraft belly freight is well-known, with capacity currently at 39% below pre-COVID-19 levels, and all the compensating measures are imperfect. For example, Goedhart says it takes four times the labor to load cargo on the passenger deck of a temporarily converted freighter as it does to load the same cargo on a regular freighter. All this pressure is occurring as e-commerce grows and demand shifts from sea freight to air freight.
Airbus is even putting its A300-600ST Beluga into cargo service as a substitute freighter. The queue for cargo conversions is long and deep, and these conversions demand both scarce skilled labor and parts made by only a few suppliers.
As a result, the cost of logistics has skyrocketed, and Goedhart says logistics is now a frequent topic of C-suite conversations with K+N customers—which was unusual before the COVID-19 crisis. When will the logistics challenge ease? Goedhart says industry colleagues don’t expect things to be any easier in 2022, and “in the first half year, surely not.”
Kellstrom Aerospace is seeing the same logistic trends as K+N. “In struggling to meet global demand for cargo air transport capacity, the speed of global transport has suffered,” observes Daniel Adamski, executive vice president of distribution at Kellstrom Aerospace. “The costs of global cargo transport have increased dramatically.”
However, Adamski agrees with AJW’s Swift that the problem extends well beyond logistics. He says airlines, OEMs, MROs and others cut inventories, including stocks of long lead-time parts, so raw material delays and cold starts for castings, forgings and extrusions makes things worse. So do delays by repair vendors in tagging used serviceable material components and delays by vendors of chemical processing, plating and surface treatments.
Labor shortages have also restricted manufacturing capacity as some of the most experienced workers retired just before the production ramp-up.
Adamski says supply challenges have been toughest for parts made from aluminum, steel and nickel alloys—especially super-alloys, including castings and forgings. Another pressure point is electrical components made from rare earth metals and especially microchips. Adamski adds: “Parts requiring specialty surface treatments, plating and other processing have also seen delays.”
Generally, OEMs that rely on sole source vendors for tier-one vendor parts introduce single-point failure risk into their supply chain. Adamski argues that parts with very high tooling and non-recurring engineering costs for cold-start production may require a multiple-source, work-share supply chain solution. “At the end of the day, it is about supply chain risk mitigation and effective buffering strategies,” he says.