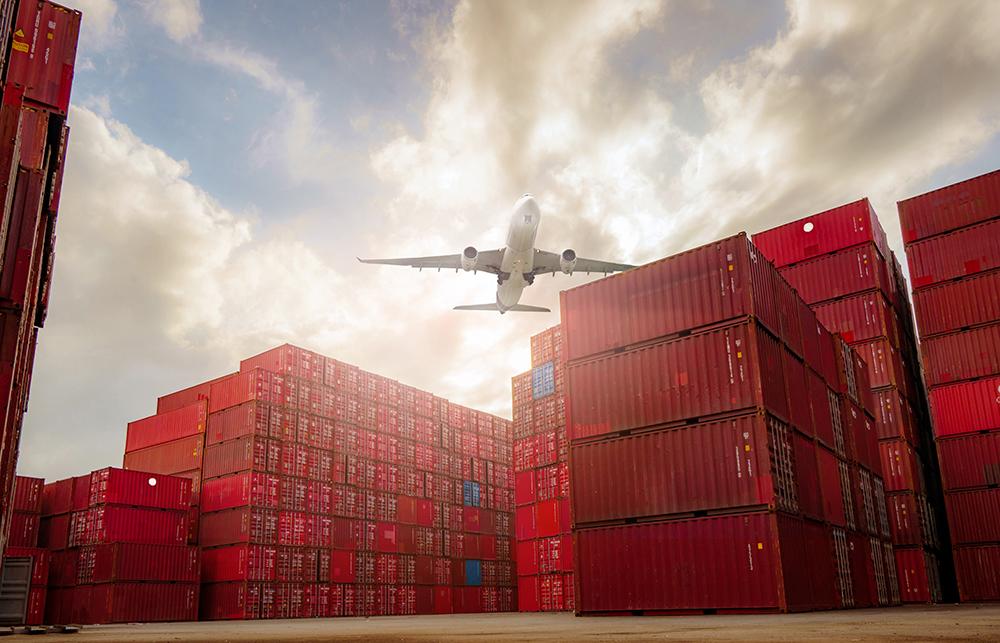
The turmoil of the last three years—including COVID-19, lockdowns, travel restrictions, air-cargo shortages, war in Ukraine and tensions across the Taiwan Strait—has led many industries to reexamine their supply chains.
A recent survey by nonprofit research organization The Conference Board found that European CEOs are seeking to bring supply sources closer to home. A Bloomberg survey of corporate presentations and earnings calls found references to “on-shoring, reshoring or nearshoring” up 1,000% in the last year, and actual factory construction in the U.S. has doubled over the same period.
Yet, the commercial aviation supply chain is rigid, if only because lengthy qualification processes are required to prove the safety of new suppliers. So far, major aviation companies seem mostly determined to work with existing supply chains, while diversifying possible future sources of supply.
Boeing did stop sourcing titanium from Russia in spring 2022. Fortunately, the airframe OEM has long had titanium suppliers from around the world, including the U.S., Japan, Kazakhstan and China. Its plans also include qualifying secondary sources for all parts, thus reducing sole-source risks, according to a spokesperson.
A spokesperson says the OEM’s other tools for managing supply chains include: frequent communication; locating Boeing experts with suppliers around the world; supporting suppliers when necessary with operational, technical or logistical assistance; and strategically placing critical buffer inventories. Boeing also informs sub-tier suppliers of its schedule for producing each aircraft.
Boeing’s rival is also holding steady. "Airbus is monitoring the situation closely and is analyzing the impact of sanctions and so forth on its business and operations,” a spokesperson says. “Regarding supply of raw materials and components, we do not see any issue in the short- to medium term."
Engine delays have posed problems for both airframe OEMs. Pratt & Whitney acknowledges it has experienced supply chain challenges with structural castings and other parts, which have resulted in engine delivery delays. “We continue to work mitigation strategies with our supply base and expect pressures to begin to ease in the second half, which will support both our original and maintenance output plans,” a spokesperson says.
Singapore-based Alton Aviation Consultant Joshua Ng argues that most aviation OEMs are not so much seeking to bring supplies closer to home, as they are seeking to diversify their supplier base across geography and companies to make it more resilient. This is especially important because certain processes, such as castings and forgings, have but few current suppliers.
However, slow changes continue to take place in the aftermarket. Ng notes that converging labor rates and high fuel costs for ferrying are making outsourcing airframe maintenance to Asia-Pacific less attractive to U.S. and European airlines. “For both U.S. and EU airlines, near-shoring options in Latin America and Eastern Europe are becoming increasingly relevant options,” says Ng.
Proximity is definitely one reason for bringing maintenance closer to home, but Latin and Eastern European MROs have also been increasing capacity and capabilities. This trend was happening well before the COVID-19 crunch.
Meanwhile, Asian MROs such as ST Engineering have entered the cargo conversion market in a big way.
Oliver Wyman Consultant Derek Costanza does not see much U.S. or EU airframe MRO being pulled out of China yet due to lack of capacity elsewhere. “There are a number of other Asian airframe MROs ramping up and others being contemplated that offer very competitive rates, but they do not yet have the scale, track record or capacity to take large share away from China,” Costanza argues.
Bringing widebody MRO back to western airlines’ home bases can be difficult if capacity does not exist and it is very expensive to build. Like Ng, Costanza sees Latin America becoming more and more important for future MRO for North American airlines.
Costanza predicts there will be no quick shifts for aircraft maintenance. “It simply isn’t possible on a large scale to move, so if it does happen, it will be a slow creep,” he says.
But for OEMs, qualification of more diversified supply sources could enable quicker shifts if these become necessary.