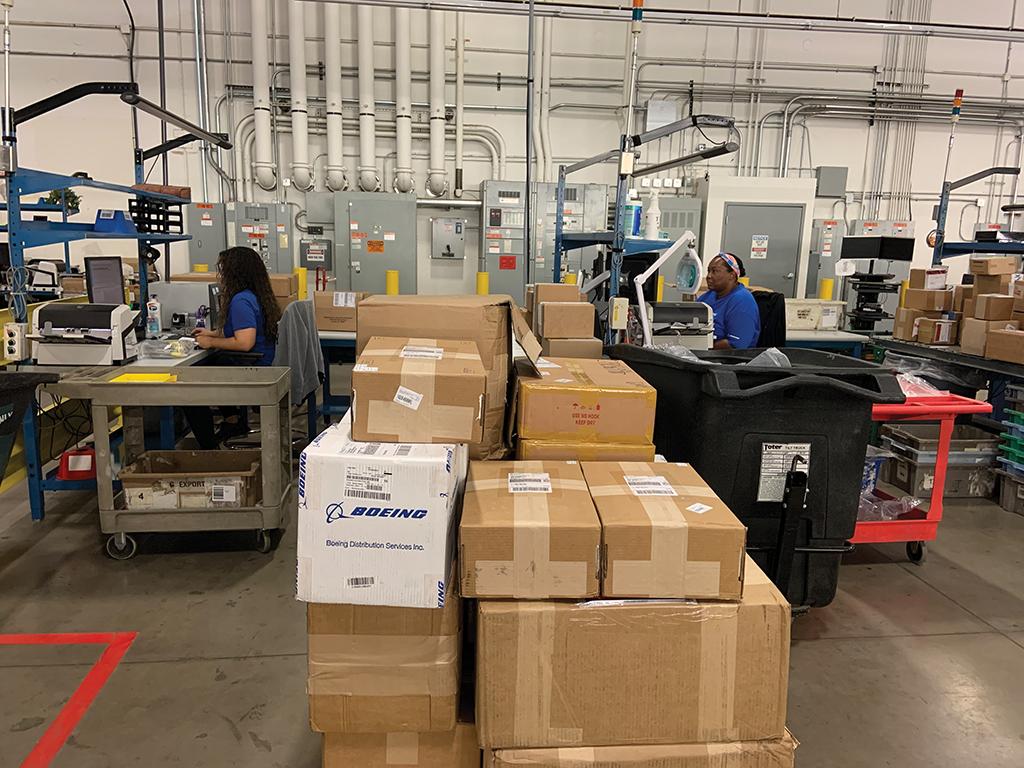
Boeing operates this 550,000-ft.2 distribution center near Dallas-Fort Worth International Airport.
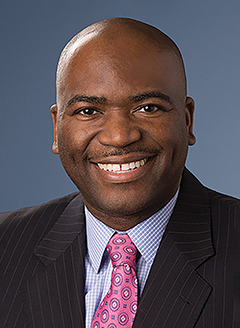
William Ampofo, Boeing’s vice president for parts and distribution services and supply chain, spoke with Lee Ann Shay at the Paris Air Show about the short-term outlook and meeting challenges, as well as growth.
What’s your take on supply chain challenges? What’s changing? There continue to be constraints in the supply chain, but we’re seeing light at the end of the tunnel. There are still challenges with raw material and labor, especially labor. We’re seeing demand—flight hours are essentially back in North America. We’re still waiting for some of the international widebody routes to open, but we’re encouraged by what we’re seeing. We’ve got a lot of focus on parts from Tier 1 and Tier 2 suppliers, and we’re also working with distressed suppliers. We’ve got a lot of folks out in the field helping our suppliers—the collaboration continues to be pretty strong.
What are the raw material shortages now? It’s the classics: castings, forgings and raw material. The propulsion side of the business is probably the most constrained.
How many global field ops people are working with suppliers? We’ve got nearly 300 people in our global field ops organization, and they’re supply chain professionals, industrial engineers and lean specialists who go to suppliers and help them understand the root cause [of a problem] and lay out their productivity in their line. The group works at the Boeing enterprise level on behalf of each of the three divisions—Boeing Commercial Airplanes, Boeing Global Services, and Boeing Defense, Space & Security. We have one common approach; it helps them get organized, and it helps us to get the information from them so we can make allocation decisions as they start to produce at rate.
What are you biggest pain points for the six months? Labor capacity. Demand is there—that’s the great news—but it’s really about labor capacity. And there are still some Tier 1s and 2s that are distressed, so we’re going to have to help them stabilize. Some Tier 2s and Tier 3s are financially distressed to the point where they’re going to go out of business, so we have to go find potential buyers or potentially go in and take them over ourselves. If we start to make inroads there, I think we’ll start to stabilize our supply chain a bit.
Do you expect supply chain consolidation? If so, will it be focused on the distressed or capability expansion/service bundling? There hasn’t been the consolidation at the high level that we had anticipated, quite frankly. It’s been more on the Tier 2 and 3 levels. Some of those Tier 2s and 3s were created as a result of Tier 1s outsourcing certain work. Now that work is coming back because the risk is too high. The good thing is that because of how it started, in many cases the intellectual property and the know-how is still there with the Tier 1s or OEMs that decided to outsource. So now it’s about reallocating funds to restore capacity and bring that work back in-house.
Is most of your labor capacity concern in the aftermarket? A lot of suppliers produce for production and the aftermarket, and some of these suppliers are not at rate—whether it’s because of labor or physical capacity. So if we have five parts coming in, do we have three go to production and two go to the aftermarket, or vice versa? I want to get past that. I want the demand signal that we send to be produced, so we don’t have to make those decisions. Flight hours are continuing to increase aftermarket demand—whether for shop visits on the engine side or basic wear and tear of components such as landing gear, wheels or brakes. It’s almost back to pre-pandemic levels.
Boeing Global Services recently opened warehouses in Germany and Poland. Are there other planned facilities? The facilities in Henstedt-Ulzburg, Germany, and Rzeszow, Poland, opened to support demand and get closer to our customers in the region. We’re also in the early stages of defining a footprint for India.