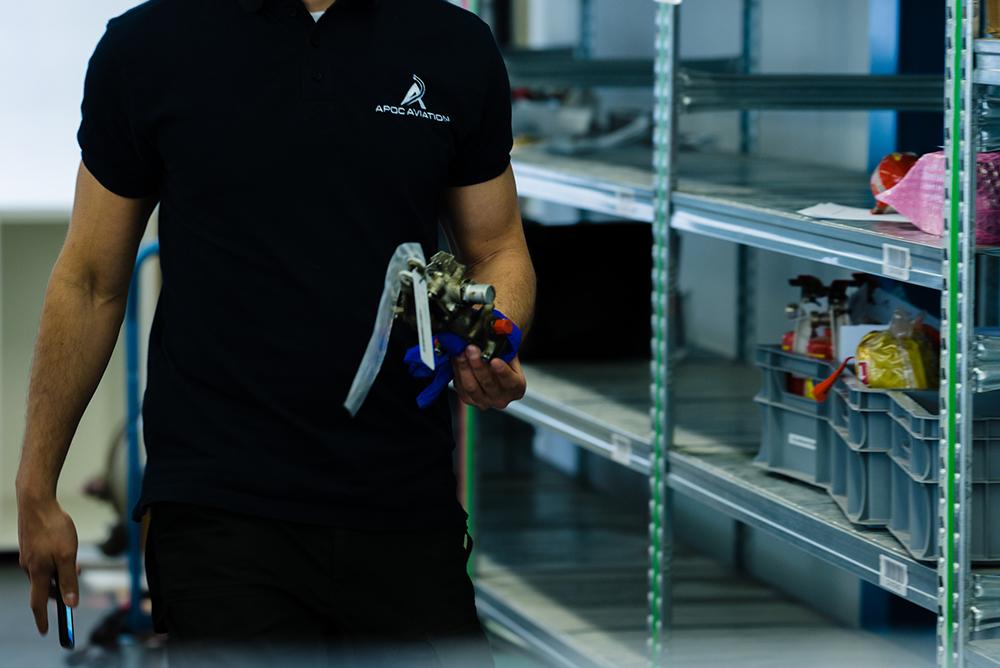
Analysts are predicting macroeconomic headwinds through 2023, even as markets recover from the COVID-19 crisis. Given the supply chain challenges within the industry, especially with problems in spare parts availability, the impact of a downturn in the global economy is an ongoing conversation at industry conferences.
Jorge Irribarra, managing director of engine product lines at Kellstrom Aerospace, feels there is justification for concern by industry leaders, especially considering the day-to-day economic indicators. “Unfortunately, these factors could affect the overall cost of parts repairs, which limits cost-effective access to inventory pools,” he says. Irribarra adds that a slowed-down economy might also increase the cost of raw materials such as metals, as well as components to raw chemicals, which will be reflected in the overall cost of the repair.
AerFin has seen unprecedented increases in repair costs over 2022-23 as OEMs seek to insulate themselves from increased production costs caused by both global and local cost escalations. Mark Shimizu, vice president of sales, says these escalations have been driven by several factors including price spikes in the energy and fuel markets, post-COVID recruitment driving up new employee salaries and national interest rate and inflation increases. “The current situation in Ukraine has had a major financial impact across the globe and is evidence of how action in one country can truly resonate across the globe,” he says.
However, Shimizu reckons it is not beyond reason to believe that future macroeconomic challenges at a national level will have far-reaching effects across the industry, therefore, the industry must continue to work around the current challenges. It also must take preemptive measures against future challenges to minimize any impact to pooling inventory.
Some experts feel a lack of shop replaceable units and raw materials are impacting lead times and will continue to have an effect. Notably, some repair shops are not even offering AOG and/or expedition fees to finish repair of items more quickly. Lead times of one year are now common and, in some cases, there is no commitment on delivery dates, according to a recent conversation with an expert from AMROS Global. If there are no serviceable spares on shelves due to long lead times for repair shops, pool and exchange providers are thus challenged to supply within the agreed terms.
Irribarra remains upbeat, noting that data and communication are key drivers to navigating uncertainty, and the demand for lift and material for maintenance support associated in the near term will outweigh the economic hurdles that will come in 2023. “As disposable income is scarce, air travel might experience a slight reduction, but MROs and line maintenance activities should stay active within reasonable levels,” he says.
Demand from operators also has shown the need for investment in exchange pools and increased willingness to partner with select vendors to support their critical parts needs. Since the entire industry is seeing costs rise, maintenance providers are likely taking steps to mitigate the headwinds to operating costs as far as possible. Industry observers think this will have limited effect on access to pooling and exchange inventory in the near term, though there may be some tempering of additions to pools and exchange stock in certain cases to balance investment versus cost.