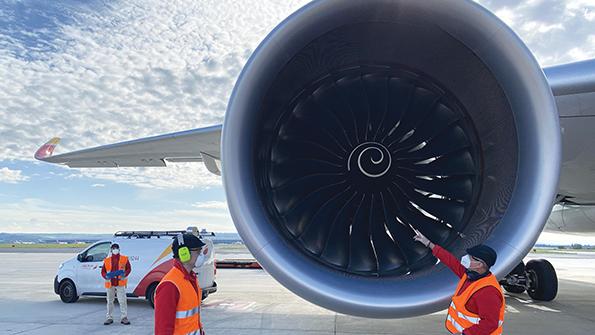
Iberia Maintenance has looked at process improvements and workforce additions to increase capacity.
With passenger traffic and flying hours ascending back to pre-COVID-19 levels this year, the market upturn has resulted in shops that are close to full and a consistent pipeline of work for MRO providers. While there are clear reasons for optimism this year, repair specialists now face something of a conundrum: Demand for maintenance services is back, but there is the very real possibility of a growing imbalance between demand and capacity, meaning further strain on suppliers and development of long-term bottlenecks.
Over the past few years, amid the global pandemic, factors such as production cuts by manufacturers and global workforce and skills shortages added pressure to an already stressed supply chain. Capacity constraints with which the industry was dealing before the crisis have continued as a mid-to-long-term concern.
For the global supply chain, which is still seeing turnaround times (TAT) lagging compared to pre-pandemic levels, industry consensus suggests the situation has improved somewhat. “We have been seeing improvements in the global supply chain situation so far this year compared to 2022,” says Tan Eng Shu, executive vice president and head of aerospace MRO at ST Engineering. “However, some OEMs and parts suppliers are still struggling to meet demand.” Meanwhile, a representative from Spanish engine component manufacturer ITP Aero, which provides full engine MRO services along with accessory and component repair, tells Inside MRO: “The supply chain is still the biggest challenge to deliver the services required by our customers. We have experienced a slight improvement compared to last year, but not enough to reach pre-COVID levels.”
In the parts segment, a shortage of OEM parts stock persists, along with an upsurge in used serviceable material (USM) parts demand, depending on the program, although availability is not a widespread issue. Ivan Gonzalez Vallejo, director of strategy and supply chain at Iberia Maintenance, says there is a defined difference between their own supplies and those of OEM parts. “OEM parts supply performance is erratic and has not gotten better,” he says. “There are continuous supply interruptions that are very hard to mitigate because bottlenecks constantly change. From a USM perspective, we see a good flow and contained pricing so far,” he says, adding that the MRO allows for longer lead times when sourcing USM parts.
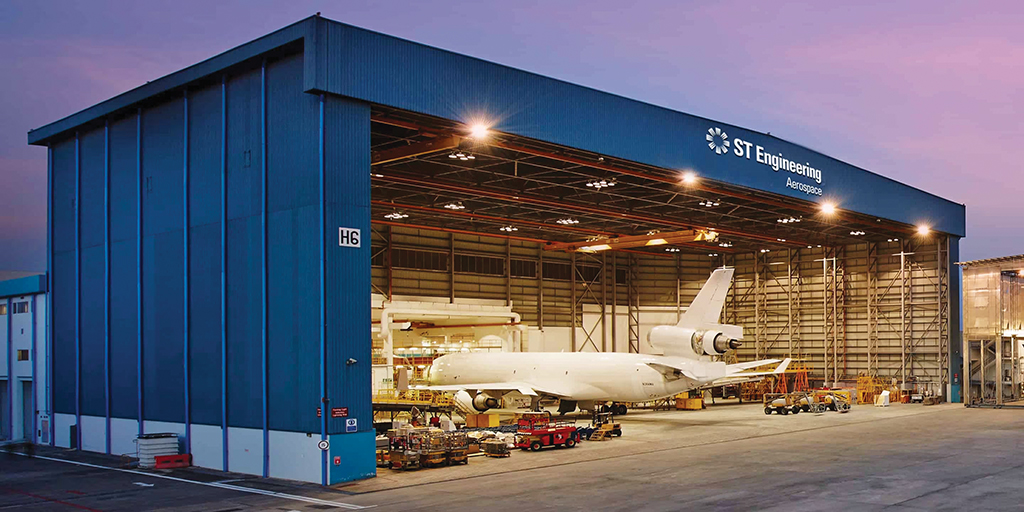
Chris Hudson, senior director of supply chain and logistics at Aviation Technical Services (ATS), says increased labor productivity has given some suppliers and OEMs the confidence to return to normal operating standards, but problems persist. “In certain pockets, there remain some continued challenges at the raw material level, delaying the production of various composite materials, as well as some paints and adhesives. Pricing in general remains inflated, but we see efforts in the supply chain to mitigate the burden,” Hudson says. Factors such as rising inflation and the war in Ukraine leading to raw material cost increases have also affected the market on a global scale, as geopolitical risks have led to overall capacity reductions in fewer countries, a representative for ITP Aero says.
The engine repair aftermarket, which has been tight since the COVID-19 crisis started, is seeing some signs of relief. “The repair service, specifically for engine components, has improved, and it is probably the category that is behaving best,” says Vallejo at Iberia Maintenance, which repairs CFM56, V2500 and RB211 engines and handles approvals for newer CFM Leap and Pratt & Whitney GTF models. “However, repair lead times are still double what they were pre-pandemic,” he adds.
Martin Friis-Petersen, senior vice president of MRO programs at German MRO provider MTU Maintenance, says the company has noticed improvement during the past few months in areas such as parts supply. “However, MTU may be less affected than others by parts shortages, as we have been replenishing our parts stocks by purchasing engines for teardown—and did so well ahead of the recovery—and repair a high share of parts in-house,” he explains. “This, in combination with a close alignment with our customer base on scheduling and forecasting, enables us to better prepare for upcoming shop visit volume.”
While moderate improvements in the supply chain give cause for optimism for an issue many expect not to be remedied until at least 2025, TATs for repairs are still a significant challenge. Philippines-based airline Cebu Pacific Air says it is seeing longer lead times across all OEM parts, some of 4-6 months or longer. It also is seeing its TATs for repairs with vendors remaining high above pre-COVID-19 levels. Shevantha Weerasekera, vice president and senior advisor for engineering and fleet management at the low-cost carrier, estimates that maintenance work related to engines has more than doubled from 60 days pre-COVID to over 120 days, but in some cases it is going up to 250 days. Meanwhile, landing gears, previously at around 90 days, are exceeding 120 days, while auxiliary power unit repair timelines have extended from 30 days to over 120 days.
Aware of the gravity of the situation yet optimistic that the environment will improve over the next 1-2 years, OEMs are looking for better ways to address the situation. Boeing plans to increase production of the Boeing 737 MAX to 50 per month by late 2026, along with ramping up the 787 to 10 per month during that same period. Airbus intends to increase A320-family production rates to 65 aircraft per month by late 2024 and 75 in 2026. It plans to build four A330s per month by late 2024, up from the three A330s it manufactured per month in late 2022, while the A350 is projected to go up to nine per month by the end of 2025 from its current level of six per month.
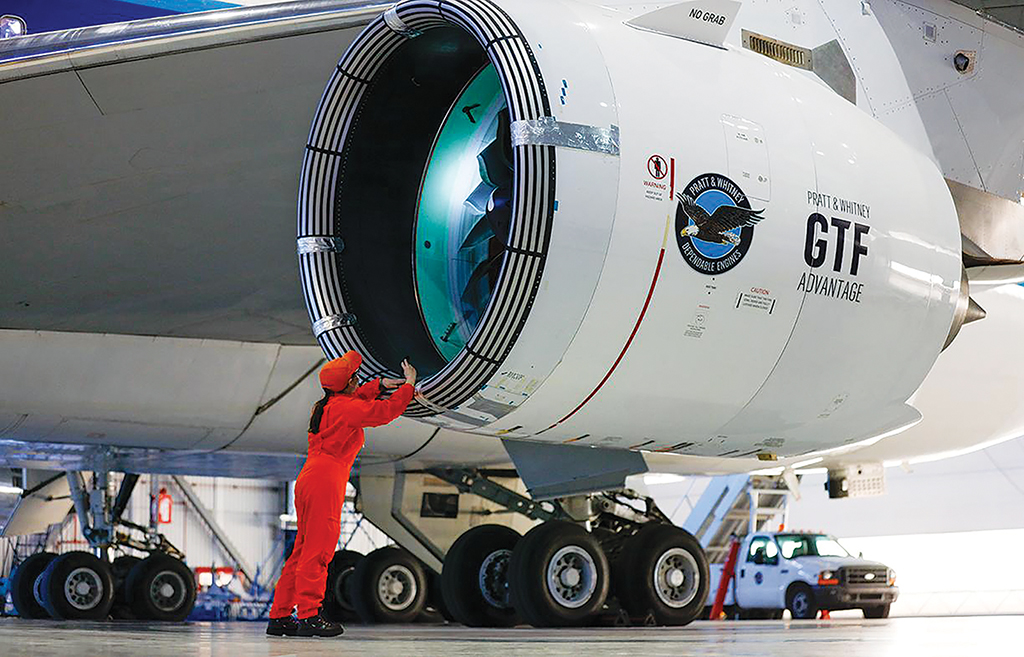
Over the past three years, the engine segment has been dogged by production cuts and technical durability issues. Pratt & Whitney, which has contended with supply chain issues related to the geared turbofan (GTF), says it has taken several actions to support both new and overhauled engines. A company representative told Inside MRO that these include “embedding staff with key suppliers to help accelerate the delivery of parts, continuing to qualify additional suppliers on key programs and assisting suppliers with employee and new staff training.”
This has led to some improvement, according to the engine OEM. “We are now starting to see improvements with year-over-year double-digit increases in supply chain output. As shop throughput accelerates, we expect to see a drop in lead times for induction,” the company representative says. “At the same time, we’re continuing to incorporate durability upgrades that will extend time on wing and reduce the demand for overhauls.” Pratt says it is expanding its GTF MRO capacity globally within its own shops and with network partners to handle increased aftermarket demand. It expects to add to its current number of 12 operational facilities, with seven more coming online over the next few years. In addition, it plans to hire “hundreds” of new employees while utilizing technology across its facilities to maximize operational efficiency.
Meanwhile, GE Aerospace, which along with its widebody engines programs also operates a 50-50 CFM International engine joint venture with Safran, is seeking to hire 2,000 people this year to address workforce shortages following layoffs at the height of the pandemic. While skills shortages have long plagued not just the aftermarket but aerospace as a whole, many companies see a recruitment drive as a challenging but necessary task to remedy the supply chain and capacity issues long-term.
In the widebody segment, which has bounced back strongly over the past 18 months, Rolls-Royce is expecting supply chain issues through this year but says capacity is relatively stable for now. The British engine OEM was trying to add more capacity across its network before the crisis, particularly to cater to next-generation engine types such as the Trent XWB and Trent 1000. It now plans to set up a joint venture with Air China in Beijing for next-generation Trent engines. CFM is also adding new facility locations to its network.
Independent MRO specialists, too, are ramping up next-generation airframe and engine capabilities to address a modernizing market and increased shop visit demand, with companies such as ST Engineering, StandardAero and SR Technics adding capability for Leap and GTF engines during the past year. Airline-affiliated MRO providers such as Luft-hansa Technik and AFI-KLM E&M have made similar moves in relation to their engine aftermarket networks.
Since capacity was a pre-crisis concern, given the high levels of demand seen in 2019, ST Engineering had planned more hangar capacity globally, even during the pandemic, and that priority remains in place. “We are still planning for more capacity this year and next,” adds Tan. Aside from its Singapore base, the company has pursued growth in China and the U.S. to address capacity constraints. In China, which reopened last year following an extended period of national lockdowns, ST Engineering established an airframe MRO joint venture with cargo carrier SF Airlines in Ezhou, Hubei. Once operations start in 2025, it will service the fleets of SF Airlines and third-party carriers. In addition, Tan says the opening of new ST Engineering hangars in Guangzhou, China, and Pensacola, Florida, this year reflects its focus on building industry partnerships and capacity growth.
“Capacity readiness remains a concern, as the demand for MRO services continues to outpace the supply of newly skilled and experienced maintenance workers,” says Hudson, who cites airframe and component mechanic labor shortages as the leading factor related to limited capacity at ATS. He says that for heavy maintenance and modification customers, ATS only commits to MRO tasks for which it has the necessary workforce to support. Maintaining and upskilling workforces is a priority for the company to ensure market readiness in the long term, and ATS says it is looking at a combination of sources to keep the talent pipeline supplying skilled labor. “In addition to recruiting the next generation of mechanics through our on-site, paid apprenticeship program, we are also maximizing workforce flexibility through intensive cross-training within our component repair product lines,” Hudson says. “These efforts help us respond to continued increases in market demand and support workforce career development initiatives.”
Friis-Petersen says MTU has opted to spread its capacity while looking to bolster its in-house capability instead of relying on third parties, such as pressurized-component vendors. “There are a number of factors we can control in that context, and they have operational flexibility at the core. One is to lessen our reliance on the parts market and focus on in-house repairs, which MTU is doing in Serbia, where we opened a brand-new repair facility outside of Belgrade at the end of 2022. The location portfolio covers five repair clusters for high-value parts like fan blades, cases and airfoils,” he says.
Friis-Petersen says MTU’s investments in additional and larger MRO facilities and staffing have helped the company boost its capacities for the future. “If you have more space and more people to conduct the work, that is an automatic increase in your ability to get engines out the door,” he adds.
MTU Maintenance plans to continue the expansion of its On-SitePlus service network, launched in the summer of 2021 to carry out aircraft-on-ground support, and on- and near-wing repairs, from borescope inspections to module swaps, among others. It also plans to address market requirements for smaller workscopes as well as hospital and quick-turn shop visits, which grew during the pandemic as airlines looked for new ways to keep engines on wing and defer full overhauls.
Airlines are still bearing the brunt of a lack of slot availability. Over the past few years, carriers have had to become more creative in managing their supply chains as well as to ensure slot availability far in advance of a shop visit. A common theme has been for carriers to postpone expensive shop visits and instead look to quick-turn and hospital shop repairs to keep assets flying instead of grounded for extended periods, owing to longer TATs.
Cebu Pacific’s Weerasekera says that in the short-to-midterm, the airline has found ways to deal with the lack of MRO slot availability and work around capacity constraints. “Cebu Pacific is self-sufficient with line maintenance, and we have contracted 12-18 months in advance for heavy checks and major shop visits—so we are OK for the moment,” he says. “But we do experience the shortage of MRO slots when we look for ad hoc work.”
As a means of hedging against parts shortages, some airlines have looked to grow their inventories as a buffer to keep aircraft flying. Another emerging trend for airlines looking to ease supply chain pressures is exploring the use of parts manufacturer approval parts—which are still a small fraction of the component segment.
Cebu Pacific identifies issues with consumable and expendable parts with specific brands, while it also sees a shortage of components with its contracted pool providers that are experiencing supply chain issues of their own. To remedy parts shortages, the airline has forward-purchased parts and consumables, while contracting in advance for MRO slots to overcome capacity shortages.