Supply Chain, Workforce Struggles Hinder Booming Engine MRO Demand
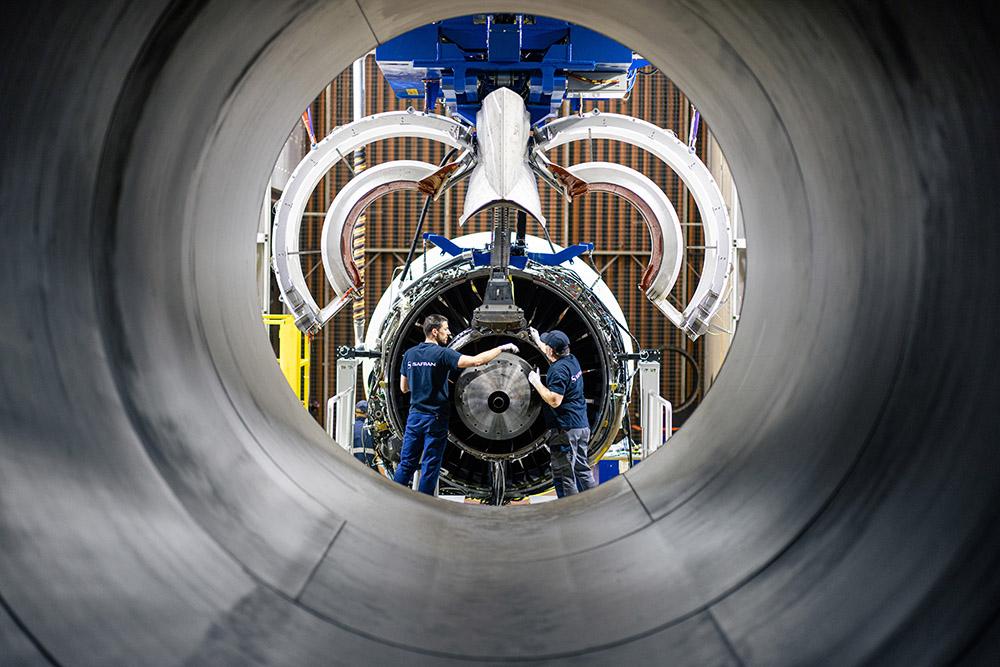
SINGAPORE—Demand for engine MRO is booming as commercial air traffic picks back up, but supply chain impacts and labor shortages continue to be a thorn in the side of aftermarket companies that are otherwise poised to benefit.
At Aviation Week’s recent MRO Asia-Pacific conference in Singapore, ST Engineering reported that despite slower traffic recovery in Asia, it is experiencing high demand for engine services. According to Tay Eng Guan, vice president and general manager of engine services for commercial aerospace at ST Engineering, the MRO has seen an influx of bookings in its engine shop over the last year.
“Everybody tried to book a slot. Everybody is struggling with slots, so we are almost fully booked and everybody is queuing up,” said Tay. However, he added that high turnover during the pandemic and a shortage of talent and resources has proved difficult.
Caroline Vandedrinck, senior vice president of business development at SR Technics, noted that the MRO has seen “huge demand” for engine MRO since this summer, but factors such as Russia’s war on Ukraine have impacted its business—and not just because it has customers from both countries.
“What we also see in the last 12 months is an increase in transportation costs,” she said. “With the war in Russia and Ukraine, you can’t overfly Russia anymore. So now, especially between Asia and Europe, we see longer transportation times and increased cost, which impacts both ourselves and our customers.”
Vandedrinck also notes that labor shortages are extending to suppliers, which is amplifying effects across the aftermarket. “Labor and supply chain issues are very closely linked,” she said. “SR Technics has a need for more labor, but so do all our suppliers.”
SR Technics benefited during the COVID-19 pandemic from government assistance that enabled short-time work for two years, which Vandedrinck said allowed the company to “retain skills, knowledge and experience when demand came back.” However, she added that “with vendors coming back, we still need to hire more people.”
ST Engineering’s Tay pointed out that many skilled workers left the aviation industry during the pandemic, and MROs' image problem is not helping—particularly in terms of less glamorous tasks such as welding, machining and other repetitive manual labor. He said ST Engineering is trying to combat this by implementing automation and robotics to eliminate repetitive work younger people do not want to do.
Tay also noted that ST Engineering used government grants to retain its entire staff during the pandemic, using the downtime to perform cross-training and reskilling of its workforce.
Vandedrinck feels optimistic that outreach efforts to introduce youth to aviation careers and a shift in how the industry markets itself to future workforce could help fill some of the gaps in workforce. For instance, she said SR Technics joined Pratt & Whitney’s GTF engine network in April and it is now working with Safran and CFM to introduce capabilities for the LEAP engine, which demonstrates its commitment to working on new technology platforms. “Being able to market that you are going to be part of the new-generation engine helps attract people,” said Vandedrinck.
She also posed the idea of drawing connections between aviation and e-commerce when marketing MRO careers to youth. “All young people know how to buy something online, but that product is at your doorstep because of aviation,” she said. “Young people will understand and will explore opportunities.”