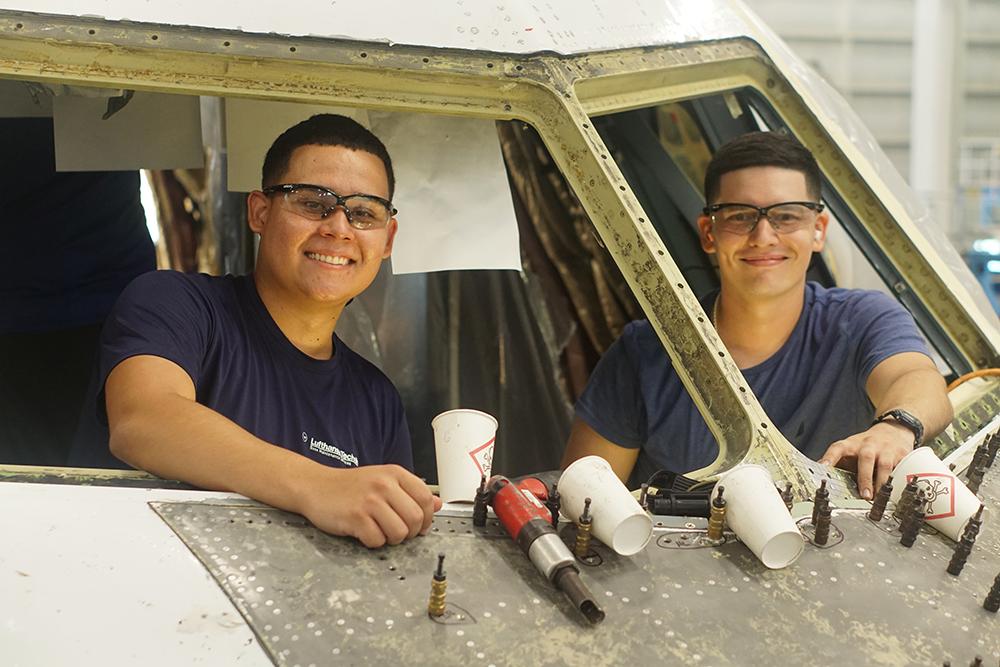
In the short term, U.S. and other countries’ airlines are struggling with a shortage of mechanics due to the COVID-19 crunch on flying. But in the medium- to long-term, the challenge is not shortages, but the pressures that demand and supply forces put on the market for talented mechanics. These pressures will determine where maintenance is actually performed, who does it and what it will cost.
One measure of demand pressure is Boeing’s forecast that North America—defined as the U.S. and Canada—needs 134,000 new technicians over the next 20 years. Based on relative fleet sizes, that implies more than 120,000 MRO recruits for U.S. aircraft.
Not all of these new mechanics will be located in the U.S. According to a Boeing forecaster, these are simply the workers needed to support airlines based in each region or country. “Where those new technicians work will be based on an individual airlines' operations, including any MRO partnerships they may have,” says the forecaster.
Historically, U.S. shops provided more maintenance to foreign carriers than foreign shops provided to U.S. airlines, especially in capital-intensive engine and component maintenance. But in the last two decades, U.S. carriers have increased outsourcing to foreign shops in labor-intensive MRO, such as airframe checks, painting and major modifications. Some experts estimate that 20% of U.S. airline MRO is now done abroad.
That is the major reason why, though U.S. airlines increased seat-mile capacity 28% from 2000 to 2019, the country’s MRO workforce remained roughly stable at 150,000-155,000 mechanics and 10,000-11,000 avionics technicians over the same period. Sending narrowbodies to Latin America and widebodies to Asia-Pacific and elsewhere enabled global supply to fill the growth gap and meet U.S. carriers’ demand for maintenance.
Consultants like Alton Aviation’s Joshua Ng expect this trend toward foreign outsourcing to continue. Mexico’s TechOps Mx can handle up to 15 narrowbodies. El Salvador’s Aeroman plans to boost its six hangars and 40 production lines by 20-30% in the next five years. Costa Rica’s Coopesa plans to add two narrowbody hangars. Lufthansa Technik Puerto Rico’s five lines offer labor rates 20% lower than North America, while still in U.S. territory. And LHT would like to grow more in the Americas.
Still, the great majority of MRO for U.S. airlines will continue to be done in the U.S. In addition, U.S. shops will continue to support foreign carriers, especially for American-made engines and components. The support for both U.S. and foreign airlines must come from three kinds of mechanics.
According to a pre-pandemic quick survey by the Aeronautical Repair Station Association (ARSA), just under half of U.S. mechanics are certificated by the FAA. These mechanics either graduated from an aviation maintenance technician (AMT) school or have passed FAA exams after obtaining 18 or 30 months of experience, depending on certification type. Just under half are non-certificated mechanics, who must be supervised by experienced mechanics or repairmen. The remainder, about 10%, are certificated repairmen, specially qualified for particular work and endorsed by their employers.
One supply challenge is increasing the portion of AMT graduates who actually go into aviation instead of other industries. In 2016, 20% of AMT graduates worked outside of aviation. That percent decreased to 15% in the boom year of 2018, then jumped to 23% in 2020, according to Crystal Maguire, executive director of the Aviation Technician Education Council. Apparently, healthy growth of aviation is the best means of encouraging AMT graduates to pursue aviation careers.
However, airlines and shops have also been increasingly proactive in recruiting all types of mechanics, with or without AMT degrees, through outreach to high schools, paid-for training, work-study programs and other means.
ARSA would like to increase both the value of the repairman certificate and the number of certificated repairmen. “We hope the small percentage of repairmen will grow,” stresses Brett Levanto, ARSA’s vice president of operations. The association is thus pressing the FAA to make repairman certificates portable among different employers.
Higher pay is one way of attracting new mechanics. U.S. shops were actually doing pretty well in paying workers when COVID-19 hit. Median real weekly wages for U.S. mechanics rose 19% from 2000 through 2019, or 1% annually, versus only 13% for U.S. wage and salary workers as a whole. Shop managers must ensure wages keep up with current inflation, but increasing real wages much faster, especially for airframe shops, may bump up against limits set by foreign competition.
Yet maintenance demands not just quantity, but quality of workforce. New mechanics will be required to work with expanding digital tools and to acquire the knowledge of veterans as quickly as possible. Remote help or instructions with augmented reality may assist here.
For example, ATP’s ChronicX and SpotLight tools help junior mechanics troubleshoot more like veterans by offering recurring defect analysis, tail history, technical publications, context-sensitive refresher training and system theory. All these capabilities are now available on mobile devices, helping mechanics fix problems right the first time.
If tools like these are deployed and work effectively, that may be enough. Based on the last two decades’ experience, the U.S. may not really need to increase the number of mechanics. Foreign shops, less maintenance-intensive new aircraft and better MRO productivity could take care of growth. But the U.S. would need to replenish a basically stable MRO workforce with new mechanics who are digitally capable and can use a variety of apps to become as MRO-capable as the veterans they replace.