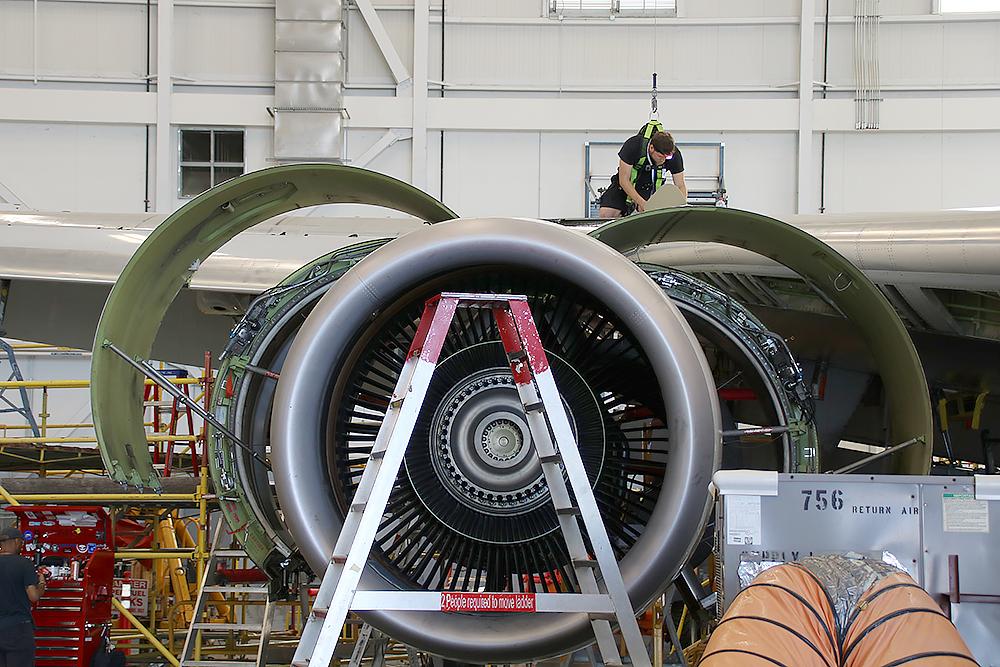
HAECO Americas is struggling to combat attrition among newly-hired technicians.
ATLANTA—Last summer Boeing warned that “juniority across the workforce” would become a major challenge for MRO providers over the next two decades, and now aircraft maintenance providers in the U.S. are echoing these concerns.
During a workforce panel at Aviation Week’s recent MRO Americas conference in Atlanta, senior executives at several MROs and airlines reported that the skills gap, which has been exacerbated by retirements of the industry’s aging workforce, is increasingly causing challenges. While the MRO industry is brimming with initiatives to attract and hire new technicians, the departure of those with senior-level experience and knowledge is causing stress for maintenance providers.
“It’s not just the number of [technicians]—it’s the skill level,” said Trey Bryson, senior vice president of operations at ATS. “In MRO there are healthy ratios of higher skill to lower-skilled people, and that literally affects the efficacy of what we do and the services that we provide. It is a pure numbers problem. The focus is having the right number of people on the higher end that are more skilled, provide oversight and do certain parts of the check where that skill level is important. It’s kind of a two-headed monster.”
At Atlas Air, which outsources much of its maintenance work to third-party companies, there is a growing need to send more senior level staff off-site to supervise. Lillian Dukes, senior vice president of technical operations at Atlas Air, cited an example where a maintenance vendor supplied two very junior-level technicians to deal with the airline’s maintenance needs. “I think, combined, they had their A&P licenses for 60 days. That concerns me,” said Dukes. “We started looking at, what are the things you have to do to mitigate those types of issues, increase oversight and things of that nature?”
According to HAECO Americas President Bill Collins, the independent MRO experienced significant attrition last year—an issue that he says keeps him awake at night. “Imagine hiring 500 technicians and losing 80. And then imagine your skill set—your average age at 55 with 25 years of experience—dropping almost overnight to 45 years of age,” said Collins. While one might not expect a skills gap between a 45-year-old and a 55-year-old, he noted that several years’ worth of experience makes a significant difference. “You start to see safety issues, and you start to see damages to aircraft throughput activity and not having enough of the right types of supervision to manage it.”
Ryan Goertzen, vice president of maintenance workforce development at AAR, pointed out that approximately 10 new airframe and powerplant (A&P) schools have launched since 2020, but “it’s still not growing fast enough.” He added: “It’s a balancing act between the people that have 3-5 and 10 years of experience. You need those people to be able to continue to hire the new folks coming into your organization. Keeping that right balance is on top of everybody’s mind every day.”
In addition to the skills gap, Collins noted that HAECO has seen high attrition levels with new, junior-level technicians. “It’s a huge expense to recruit people and then provide the training all the way through A&P or working certificate. What we’ve found is that the attrition in people with less than a year of experience is exceptionally high. It’s maybe 40% higher than what last year’s exceptionally high attrition rate was.”
Collins noted that HAECO is working on strategies to ensure new talent will stay long-term. “We’re getting smarter in the front end. We are working toward getting a five-day assessment in a legal way to make sure that we’re ferreting out who’s going to work and who’s not going to work, and who’s going to be there for the long term, so that we don’t go a year and then somebody quits, and we’ve blown another $100,000,” he said.
When it comes to concern about balancing junior-level workforce with experienced technicians, Goertzen says there are only two real talent pools to draw from: technicians coming from the military or from countries outside the U.S. However, he says this may be easier said than done.
Goertzen estimates that the MRO industry is only capturing about 10% of military technicians into the civilian sector, despite many initiatives to transition veterans to the workforce. He also points out that immigration policies in the U.S. make it extremely difficult to bring in international talent. “Google and all of the tech industries have this [issue] and they’re especially starting to see it with regards to the CHIPS Act organizations that are trying to get this talent,” he said.
Meanwhile, Goertzen says AAR’s facilities in Canada have technicians from 26 countries and Emirates has pilot and maintenance workforce from 50 countries, so “I think it’s something we as an industry need to address. If they can do it successfully, I think we should be able to do the same.”
Collins says HAECO is beginning to test the use of international talent in its Americas facilities, despite previous skepticism. “It’s an arm’s length arrangement with one of our partners because I’m not personally confident in it yet, but I want to go to 100 as quickly as I can there,” he said. “MROs [in the U.S.] could use 500 technicians each today. There’s so much work we’re having to turn away. So the strategy has to change if you’re going to get a stretch at some point.”