Podcast: Boeing’s MAX 9 Fiasco
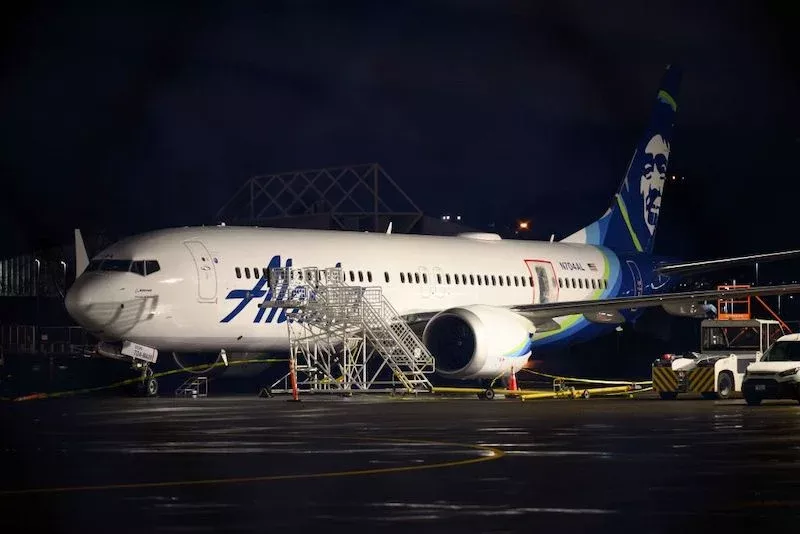
As bad as it is for Boeing, it could have been a lot worse. Listen in as our editors discuss the Alaska Airlines midair blowout.
Don't miss a single episode of the award-winning Check 6. Subscribe in Apple Podcasts, Google Podcasts, Amazon, Audible and Spotify.
Discover all of Aviation Week Network's podcasts on our Apple Podcasts channel or aviationweek.com/podcasts.
- FAA Boeing 737-9 Production Probe Adds To Boeing’s Woes
- Boeing’s Calhoun Cites ‘Quality Escape’ In 737-9 Groundings
- NTSB Eyeing Door Plug Bolts In Alaska 737-9 Accident Probe
- Preliminary 737-9 Door Plug Checks Reveal Possible Installation Problems
- Daily Memo: Forever-Lost Data Limits Potential Safety Benefits From Alaska Accident
- FAA Grounds, Orders Immediate Inspections Of Most Boeing 737-9s
Rush Transcript
Joe Anselmo:
Welcome to the Check 6 Podcast. I'm Joe Anselmo, Aviation Week's Editorial Director and Editor in Chief of Aviation Week & Space Technology magazine.
Just when it looked like Boeing had put its 737 MAX woes in the rear-view mirror, the program is in another big mess. As our listeners almost certainly have heard, a door plug on an Alaska Airlines 737 MAX 9 passenger jet blew off seven minutes after takeoff from Portland, Oregon, on January 5th. Flying a pressurized aircraft with an open hole in the side of the cabin, pilots were able to return to the airport. Miraculously, none of the 177 passengers and crew on board were killed or drastically injured. But subsequent inspections of other MAX 9s by Alaska and United Airlines, uncovered loose bolts in the door plugs, raising new questions about quality control at Boeing and 737 fuselage supplier Spirit AeroSystems.
Here to unpack this new MAX saga and what it might mean for Boeing are Sean Broderick, Aviation Week's Chief Safety Editor, Michael Bruno, our Senior Business Editor, and Daniel Williams, our Manager of Civil Fleet, Flight and Forecast Data. But first I'd like to share some insights from Guy Norris, a senior Aviation Week editor who has covered Boeing for decades. Guy today is participating in the AIAA SciTech conference in Orlando and could not join us for the podcast, but he has shared his thoughts with the team before the podcast.
Guy says that, quote, "With all this bad publicity, embarrassment and stock price damage might be bad for Boeing, it could have easily been much, much worse. Boeing really dodged a bullet here.” Lucky break number one, the fact that the event occurred at a relatively low altitude meant that it was a low energy decompression. Even a further 4,000 to 6,000 feet could have spelled disaster for the occupants and increased the risk of a total loss.
Lucky break number two, Guy says, is that nobody was in the adjacent seat and got sucked out.
Lucky break number three was that when the panel separated, it rotated up and away and did not impact with either the vertical or horizontal tail.
An FAA official Guy Norris spoke with said that if either of those had happened, we'd be dealing with a much different story for Boeing. As it is, his message is basically; "Tighten the damn bolts, check for missing or loose ones and move on. The design is proven and safe with thousands of flight hours under its belt and this quality escape for the company is just that, not a fundamental design problem."
Sean Broderick, over to you. What do you think of all that?
Sean Broderick:
Well, I think that this problem is big enough as it's emerging. So, at this point it would be good news for Boeing if the so-called quality escapes, as CEO Dave Calhoun called them, that are turning up in the grounded fleet are related to the Alaska accident. That has not been definitively determined by the NTSB. The good news for Boeing is they either have one problem. The bad news would be they have multiple problems. This is not Boeing's first quality escape as listeners know. This is, however, potentially, and I would go as far as to say likely the first one with a significant safety ramification. This is a safety of flight issue. Whatever happened to that Alaska airplane, if it's the quality escape, a production quality escape, and that while you can simply tighten the bolts and move on in an isolated case or even an isolated fleet case, I think this situation begs the question on... It has certainly put a spotlight on Boeing, it's made the crisis deeper and I think all of that is justified. That is my reaction to the tighten the bolts and move on. On the one hand, isolated case, yes, even in a fleet situation, yes, but quality escapes are not isolated cases at Boeing and if we begin to get into safety of flight issues, we have major problems. Well, at least Boeing has major problems.
Joe Anselmo:
And what do we know, Sean, about what happened? How did this happen?
Sean Broderick:
So, the simplest explanation is that these fuselage, there were these mid-emergency exit door plug assemblies, say it with me everybody, they are an optional way to block off an unneeded emergency exit on some of Boeing's longer aircraft. The plugs specifically only the 737-9 and its predecessor, the closest predecessor, the 900ER version of the NG family. This plug is supposed to remain in place and you don't even know it's there if you're sitting next to it. It's got a window covered over with interior paneling. It's in place. However, it is made to move for maintenance reasons and for installation purposes. It's not a traditional plug type. And when I say plug, I mean can't be forced out of the fuselage like a plug door. The plug terminology that's used is different. It means it plugs the hole. There's two different, and it makes it confusing, two different terminologies here.
The door can move and pivot upward and outward slightly if certain bolts are removed from it and it's designed to do that, but only during maintenance and installation. This airplane had about 130 cycles on it, no maintenance done on this airplane. So, the NTSB determined that the plug, left-hand plug on this airplane, did in fact pivot up, move out, and was ripped off the airplane. They aren't sure right now if there were ever bolts installed, but they will know, they may know before this podcast goes out to the public. All they got to do is find witness marks on the recovered plug, which they found, and on the assembly that's on the rest of the aircraft.
So as soon as this accident happened on January the 5th, Alaska grounded its 737-9 fleet, regulators followed immediately the next day of the FAA and then regulators around the world said every airplane, every 737-9 with this plug needs to be grounded for inspections. Even before Boeing developed the specific service instructions, the initial inspection started to turn up some problematic things. They were significant enough that as Dave Calhoun told CNBC in his first and so far only public remarks, or at least media remarks after the accident, the findings were significant enough to tell Boeing that they had a quality escape issue here. And the chain of custody and the process, how these fuselages are made, those plugs are installed at Spirit, onto the rest of the fuselage, loaded onto train cars and shipped to Boeing. They are standard operating procedure. They are not touched during the final assembly process or before delivery, unless testing of the fuselage shows a problem with the plugs.
So, Calhoun stopped short of linking the quality escapes that Alaska and United at least have found in their fleets, to the Alaska accident. But they are clearly concerned, and I'm going to go as far as saying, they probably have come up with a scenario under which the problems that they found in the fleet, if they get bad enough, they can lead to what happened with the Alaska airplane; a bolt likely working its way free, maybe to the rest of them, not being able to hold the load. The door opens when it's not supposed to or pivots, the plug opens when it's not supposed to, it's like a door and flies off the airplane. So, that's what we know and it is changing rapidly.
Joe Anselmo:
And Sean mentioned Dave Calhoun. Dave Calhoun is obviously the CEO of Boeing. The numbers guy, Dan Williams, Sean and both Guy Norris noted that there's many, many older generation, 900ER NGs in service. They've never had a door plug pop off, but there's not so many MAX 9s with door plugs in service either. We think about five airlines. That's it, right?
Dan Williams:
Yeah. Obviously it's a new aircraft. The MAX is a new aircraft, the MAX 9 is newer and obviously the MAX had its production pause and delivery pause from March 2019, through to December 2020. So obviously there was a period when nothing was getting delivered. United took the first MAX 9 in 2018, so there are 200-plus in service. This plug, as Sean has referred to, only applies to operators who want to operate the aircraft under the MAX capacity. So there are some operators around the world who are operating the MAX 9 with a door. Now, some of them have an active door, because they are low cost carriers, they stack as many people on those aircraft as they can. They need the door for emergency exit issue. So, that's fine. Those aircraft are still fine to fly, because it is not a plug.
There are other aircraft, other operators like Iceland Air for example, who have a MAX 9 with a door. However, the door is deactivated, so it won't be used in an emergency situation. They do not need it, because they have not got max capacity seating on their aircraft. However, there's pros and cons to a deactivated door. The pro is, right now, you can still fly it. The con is it's a little bit more weighty and it will cost a little bit more in maintenance. So while it doesn't cost as much as an active door, because the active door needs to pass certain criteria, it will cost more than a plug, because a plug ultimately, and I'm going to be very crude, is just a piece of metal that they jam in the hole. It's a little bit more sophisticated than that, but that's what it is. It's not a sophisticated item like a door.
So we have that, and predominantly we believe this is affecting obviously Alaska and United, the most prominent two. They are the biggest operators of the MAX 9 in the world. Copa, Aero Mexico and Turkish we believe are the other ones that are affected. There is an extra caveat to the report that the FAA put out, and that is for those that have less than 4,000 cycles, which therefore leads me to believe that those that are over 4,000 cycles have to have had their plugs checked, let's say at a 4,000 cycle. So there may be plug flying MAX 9s still in the world. This happened, and the first thing that I do is I reach out to Mr. Sean Broderick, because he's a much more learned man than I am, and I'm like, "Do these plugs differ from the NG 900ER?" Sean, very diligently, went out and said, "No, they're the same." Because my initial thought is; has there been some potential... this is what we do with the 900ER, so the MAX 9s the same. Let's just do it. Or has there been some latency between stuff like that, but they are exactly the same. So that takes away that.
Something that I have talked about is this quality escape, which seems to have made its way into our aviation industry lexicon, is Spirit [AeroSystems] installed the plugs. We don't know. Sean's just said that Boeing says that they don't touch them. I have no reason to disbelieve them. So that means there's been a failure of QA potentially at Spirit. There's been a failure of QA by Boeing, because they've had their fuselage in their possession, and then the FAA sign off on all of these MAX deliveries, because that is the rule that they say is they have to sign off. So, I'm just saying. And then we don't know post-delivery... The most interesting thing about this aircraft was that by the end of December it only had 134 cycles. So let's say it's about 150 cycle airframe. It was really interesting for something that young for that to happen, considering there are aircraft with 4,000 plus cycles out there already.
So, I don't know if upon delivery, if some of these aircraft have gone in for WiFi, IFC, live TV and the like, again, we don't know after delivery if anything's happened with those plugs. There's still a lot of outstanding questions and like Sean says, we need to find out how it happened. Was it because the bolts sheared? Was it because there were missing bolts? We don't know this yet and this is why we record these podcasts not the day of these things happen, because there's so many questions. We still have so many questions. However, we've gone through a bit of a motion to try and get through it. So, it's going to be really interesting and this is not helping the narrowody market at the moment. We've talked about the GTF [Pratt & Whitney Geared Turbofan engine] plenty of times. There are 400 A320 GTF powered aircraft that have spent significant time on the ground within the past couple of months. Add on to this, another 171 MAX 9s, that becomes a difficult situation for operators to operate in just from a lift capacity standpoint.
Joe Anselmo:
Okay, well, he’s getting into finances, which means it's time for us to hear from Michael Bruno. Michael, what does this all mean for Boeing, for the company's financial future?
Michael Bruno:
e don't know yet and we won't get a real inkling about it until January 31st, which is when Boeing is scheduled to report their 2023 financial results. And traditionally, and we widely expect them to have to address not only the plug issue technically, but as well as what does it mean for production forecasts, and most importantly for investors. What does it mean for free cashflow projections? Which are the most important thing when it comes to Wall Street and what they want to see Boeing meet in regards to commitments. Boeing CEO Calhoun has long said things like production, deliveries are going to be volatile. There's going to be lumpiness, some months are up, some months are down. But overall, there's been a projection of financial results that Boeing has led everyone to believe, and they're supposed to have achieved at least $3 billion in free cash flow in 2023. Tt's widely expected that they will do that. There is a expectation for maybe around $5 billion for 2024, but that expectation was before this plug thing came out.
So, the one big thing that is the issue here for both Boeing and Spirit is how much of an issue does this mean when it comes to supply chain problems that are unresolved? And by that I mean we know there are supply chain issues. We've been talking about it for years and Boeing and Spirit have been working on it and actually they came up with a new master agreement after Spirit AeroSystems got a new CEO last fall. And this new master agreement had already accounted for last year's problem with the aft bulkhead pressure situation in the tail fin assembly. But this new plug issue isn't covered by that agreement. So if there's financial fallout and it goes to Spirit, Spirit could wind up being financially responsible to Boeing who has to pay its own customers concessions in the end, and nobody really knows.
We've seen some Wall Street analysts come out with estimates that a two-week grounding of the affected fleet could be maybe $36 million. They're wildly guessing on what does it cost to do a repair, but it could be $15,000 to $30,000 per aircraft. Those are financials that you can stipulate with a pretty good guess, but what you can't guess is whether there's actual workers in a factory somewhere and the ability of a production line to rework and to get this issue taken care of on top of all the other issues that they're doing. And that's the last thing that I want to leave this group with and leave the listening audience with.
I'll be the doom and gloom guy here. Okay, so the problem is this opens a scenario where you've really touched upon the fact that there's been this tremendous change in the supply chains' workforce, with the expertise and the ability to carry out programs and to execute on contracts that have already been awarded. Joe, you and I have had a podcast just recently where somebody talked about work that people aren't bidding on anymore, because they don't have the workforce. Now, we could really start to see work that needs to be redone for stuff that you basically took for granted. You thought it was delivered, it got passed off on. Turns out you got to go back in and rework. And the question is how much else can you rework now at this point? So, there's going to be a lot of questions for the supply chain coming out of this probably for weeks and months to come.
Joe Anselmo:
Sean, I just keep getting back to that point Guy Norris made; Boeing really dodged a bullet here. The fact that no one was sitting next to that window where the panel blew out, that nobody was killed. But how does this happen? This seems to be an issue of just basic competence, installing bolts properly.
Sean Broderick:
Well, yeah, picking up off of what Michael said, you earn a type certificate by demonstrating that your designs meet the applicable regulations, and that includes every failure scenario is tolerable, or you have an answer for it. On the production side, it's similar except for you have to show that your systems can produce the same article, or in this case an entire airplane over and over and it meets the design specifications. Within those, you're supposed to have systems in place, if you are the company, if you are Boeing. It's not the FAA's job to go in and make sure that everything Boeing does is correct. It is Boeing's job to do that, okay. It is the manufacturer's, or the applicant's job in regulatory terms, to make sure that what they do complies with the regulations. It is the regulator's job to make sure that the applicant has systems in place to get that done.
What we are seeing repeatedly here, not just problems with Boeing's systems, but problems at the FAA as well to detect or to evaluate the competency of Boeing's systems. And so all the FAA can do is try harder. And for those in its wake, like Boeing, starting with Boeing, that means more scrutiny of things like service instructions to get grounded airplanes going, probably more scrutiny of airplanes that are in certification, and probably more scrutiny for anybody who does anything similar to Boeing, like build large articles.
How do you fix it? It's a great question, but with the pressures that Michael referred to and the changing landscape of the supply chain, it gives the companies more of an issue and the FAA more of a challenge. And I just hope that the systems they have in place and the safeguards they have in place and some good fortune keeps the safety record moving in the right direction. So far it has, but as you said, it's taken some good fortune to keep it there.
Joe Anselmo:
We heard the FAA official tell Guy, "You tighten up the damn bolts, check for missing or loose ones and move on." But it's not that simple, is it? A piece flew off an airplane and we averted a disaster, but is the flying public going to really buy that?
Sean Broderick:
Well, we'll see, but again, for this particular problem and in a vacuum, the FAA official is correct. The problem is that this is the latest and also most significant problem, not the only problem.
Michael Bruno:
To pile on with what Sean is saying, while the FAA official that Guy Norris talked to is right, and as Sean says in a vacuum, that's exactly what you would do, there's the unknown unknowns about what is the state of the supply chain. At Spirit AeroSystems, if, if that is where this issue is found to have a root cause, and that's if, that determination has by far not been made and there'll still be probably Boeing responsibility even with that, but if that's the case, you're talking about; why wasn't this simply bolted in the first place? Bolts and fasteners and things like that in an aircraft are not the most technologically troubling and difficult parts of building an airplane. We've become quite masterful at it over the recent century.
But, the issue is if you've got a significant new workforce, younger, new to aerospace and less manufacturers skilled, if there's institutional knowledge that's left and you can't quite hire them back, it's still not as easy a case of go tighten the bolts. You're probably trying to train up your workforce to understand exactly what they have to do, all at the same time of meeting... Let's not forget, production rate ramp is supposed to be happening this year. We're supposed to be going from roughly 30 MAXs being produced, newly a month now, to 40 by the end of the month, and that's below what Boeing would like to see. But in reality, from what we're hearing, that's probably what's going to happen. So, that's a one-third increase in the production monthly ramp that's going to happen even while all of this is taking place.
Dan Williams:
Just quickly jumping on, we don't like bashing Boeing. We need Boeing to survive. It gives us a lot to talk about, don't get me wrong. I've done a lot of podcasts. If it's GTF or Boeing this year, or 2023, I've talked a lot about them. However, it's another issue for Dave Calhoun to deal with. He stood up to the plate and he said, "Look, we have to own the mistake.” Because this is the first time in terms of the MAX that they've had to step up to the plate post the grounding where they've had to own it. And this is something that Dave Calhoun sadly has been involved in all of this, not as the top dog as he is now, but even when the initial MAX grounded and the initial MAX incidents, Calhoun was involved in the upper echelon of management.
So, they've had a learning journey to go on here to realize their mistake and they're owning it, which is a start. However, this problem, it could run much deeper. Like Michael said, it's supply chain. It's not necessarily a labor issue now we are seeing with the supply chain, it's the experience hours in that supply chain. We've spoken to various people around the world and they're like, "We've got as many people now as we had pre-pandemic. We've got more people now than we had pre-pandemic." Yes. However, people who had 20, 25, 30, 30-plus years of experience walked away from the industry, either went and retired or earned different money elsewhere, more money elsewhere in something that they were deemed as more secure and we were bringing in very new people into the industry. So, the experience workload gap is still big even if the headcount is not.
Joe Anselmo:
Does that apply to Airbus as well, Dan? We're not seeing these kinds of problems with Airbus.
Dan Williams:
Do you know what? Airbus right now, Airbus are very good at saying and doing nothing, because all they have to do is not mess up. We've had the incident with Airbus, the Airbus Japan Airlines A350, which was an horrendous accident in terms of when you look at it physically, it was tragic for the five people on board, the -8. However, Airbus will look at the A350 and say, "We've got every single person off that aircraft with three functioning exits in under three minutes." The industry when it works safe is brilliant, but the industry just needs to be consistent, deliver good quality products, because all you're doing, people... if this happened with the first MAX. My gran, and I'll give her a shout-out on this podcast, she knew about the MAX. She never knew about the MAX prior to the previous one, and now all of a sudden it's like, "Oh, I'm flying on a MAX. I'm not sure..." She was worried. The industry has forgotten that right now, because people were just happy to travel. They don't realize generally if they're traveling on a MAX, however, the MAX is back in the headlines again and my gran is like, "Hmm, the MAX." So, it's just bad PR.
Michael Bruno:
I do want to point out one quick thing to follow on what Dan says. Airbus and Europe in general did manage the workforce differently through the pandemic. And not to get off on a tangent, because we have done other podcasts on it, but they manage things very differently and we don't think that they quite had the institutional knowledge exodus that maybe happened here in the U.S. We don't even know necessarily for sure that that's still exactly what happened here, but it's definitely an issue that's haunting industry in the back of everybody's head.
Joe Anselmo:
Guys, we're going long, so we're going to have to wrap up soon. But Sean, I did want to get to one question. We keep talking about the airplane builders. Alaska Airlines, this aircraft that had the incident, they had an auto pressurization failure warning on three prior flights, and it didn't say that this specific panel was the problem, but it did say that there was a pressure problem and Alaska went so far as to say, "We're not flying this over the ocean to Hawaii." So they knew something was wrong. So, was it a mistake by Alaska to keep flying this without looking at it a little more rigorously?
Sean Broderick:
No. Based on what we know, I don't think so. Look, it's very common. The ETOPS Regulations are very strict and any airline worth its salt, if it has any concerns about an airplane, but there is a gap between not flying the airplane and having some concerns, but still thinking it's safe. It's the function of the minimum equipment list that are available. You can fly without certain things operating in certain conditions. ETOPS are the most rigorous conditions.
Alaska puts this airplane, one thing we haven't noted, short haul, this was a Portland to Ontario [California] flight. Alaska didn't have it on there for capacity reasons necessarily. They had it on there, because that's how they break in these airplanes when they bring them into the fleet. So that's an ETOPS airplane, and it could have been on that route even if it didn't have the issues, is what I'm saying. It's how they break them in. So I don't think Alaska made any mistakes. It's not clear whether those pressurization issues we're linked to the problem. It makes sense, but Alaska went through what it was supposed to do with those maintenance alerts, and by all accounts, the system did what it was supposed to do. Is it a problem with the system? Maybe.
One last point to throw on here, just to add more doom and gloom, you can rest assured that the FAA and Boeing are going through the system safety assessments for this particular failure on this airplane. And perhaps they will find that this was an extremely improbable event. But if they find that the misplacement or the backing out or the braking of one bolt can cause what we saw with the Alaska accident and potentially worse, had the panel flown off and hit something behind it like the tail, you might be looking at design changes and you might be looking at airplanes on the ground for a while. Not saying it'll happen, but saying it's certainly something that's going to be looked at and going to be looked at much more carefully today than it would have been pre-737 MAX and FAA certification and oversight changes.
Joe Anselmo:
Wow. Well, that's all a lot to digest and think about. We better get this podcast off to the editors before the story changes on us again. But guys, thanks for a really insightful conversation. That is a wrap for this week's Check 6 Podcast. A special thanks to this week's podcast producers, Guy Ferneyhough and Andrea Copley-Smith. We'll be back undoubtedly to talk about this issue in the future, but we will also be back with Check 6 next week. In the meantime, to our listeners, we wish you a great week and we thank you for your time.