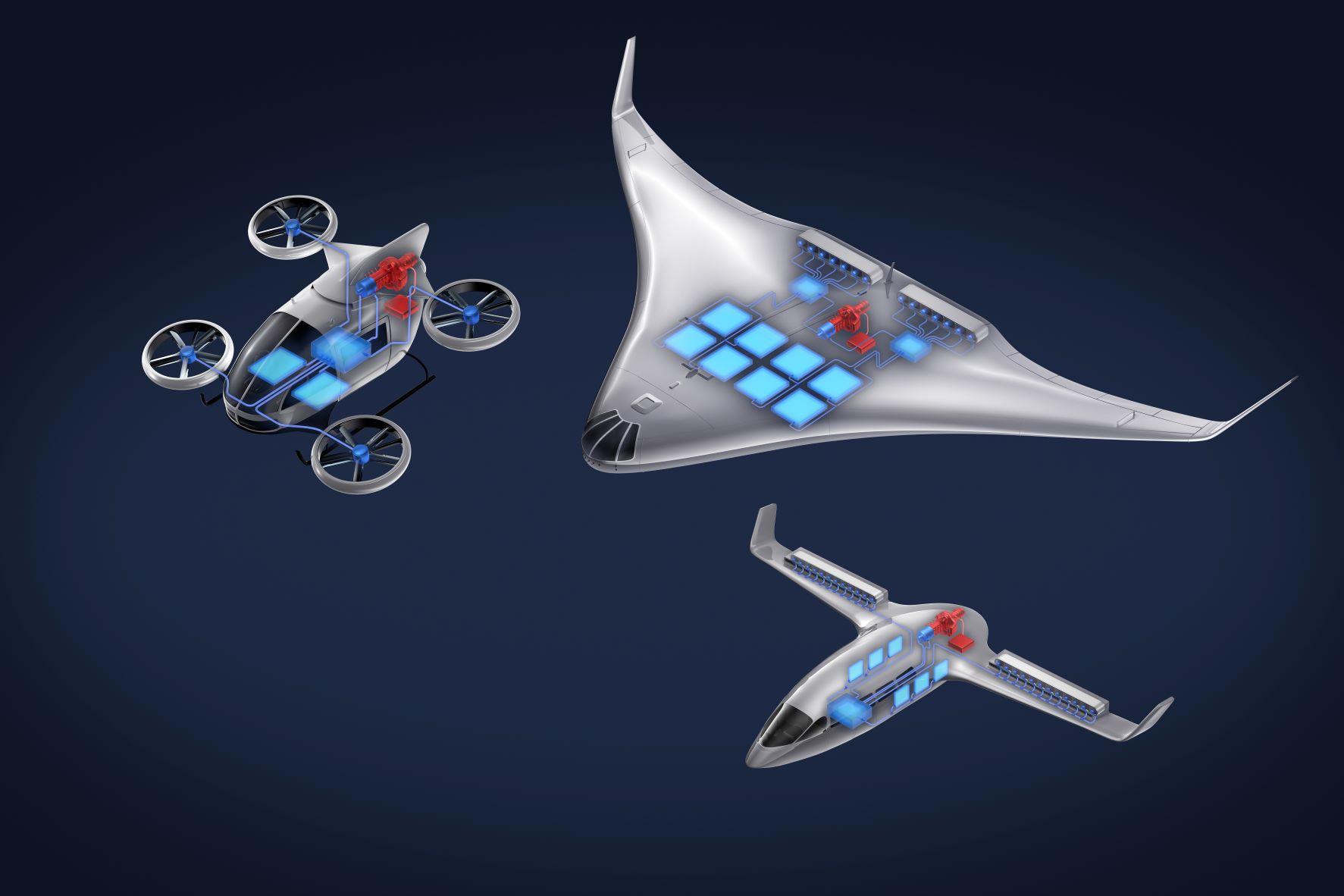
FARNBOROUGH—As part of a growing push toward sustainable aviation, Raytheon companies Collins Aerospace and Pratt & Whitney are developing a hybrid-electric technology demonstrator program.
Together they are targeting propulsion systems for future advanced air mobility vehicles and—potentially—small and medium-sized regional aircraft.
The emergence of the scalable turboelectric powertrain technology (STEP-Tech) ground demonstrator comes as Collins reaches a milestone in tests of a 1-megawatt electric motor and controller unit for another key alternative propulsion project: Pratt & Whitney Canada’s (P&WC) regional hybrid-electric flight Dash 8-100 demonstrator. Both motor and controller have successfully run at full current, voltage and speed, clearing the way for ground tests in Canada later this year.
STEP-Tech is under construction at the Raytheon Technologies Research Center (RTRC) in East Hartford, Connecticut. Ground tests are expected to begin later this year. Focused on high voltage distributed turboelectric hybrid-electric propulsion concepts in the 100-500 kW class, and with potential to grow to 1 megawatt and beyond, the demonstrator is modular and scalable to enable rapid prototyping of a range of configurations.
“In this space you’ll have a series and a distributed hydroelectric propulsion system,” says Frank Preli, vice president of propulsion and materials technology at Pratt. Preli continues: “We'll have a turbo generator generating electricity and that will be managed across one or more propulsors. So, in certain applications, you may have a dozen of these, and this facility gives us the ability to look at each aspect of that system and optimize each one individually or as a system. Having it over at RTRC also gives us the ability to move very quickly.”
The turbogenerator in the STEP-Tech demonstrator will be based on a version of the thermal engine under development by P&WC for the Dash 8-100-based hybrid-electric propulsion demonstrator. The C$163 million ($125 million) project, which includes De Havilland Canada, is due to start flight tests beginning in 2024. The demonstrator is a successor to Project 804, an earlier hybrid-demonstrator plan which was subsequently sidelined, and targets a 30% reduction in fuel burn and CO2 emissions on a 250-mi. sector compared to a current state-of-the-art regional.
The RTRC demonstrator will also include energy storage, power electronics and modular electrically driven propulsors, and adds to a growing suite of extensive test facilities and electric-propulsion-related development work across the company. In addition to the converted Dash 8-100 testbed, Collins continue to develop the Grid—a $50 million aircraft electrification and electric propulsion laboratory in Rockford, Illinois.
Initially expected to begin tests in 2021, the 25,000-ft.² lab is now set to begin operations in 2023 following delays and revisions to some programs—including the focus on a re-baselined hybrid power successor to Project 804. “[The Grid] was slowed down,” to align with user demand, says Bill Dolan, Collins’ vice president of engineering and technology for power and controls. “We wanted to get an airframer and we have that with De Havilland, and so essentially the Grid right now is on pace for what we think that demand is. We're [also] testing right now at the University of Nottingham, UK, and that was also a part of the plan as we slowed a little bit on the Grid to make sure that you know we were headed down the right path.”
Incorporating lessons learned from the Airplane Power Systems Integration Facility (APSIF), where the Boeing 787’s 1.5-megawatt electric system was tested, and the Common Automated System Integration Lab which tested Airbus A220 and Comac C919 systems, the Grid is designed for an initial capability of 8 megawatts with expansion to 13 megawatts. The facility will be used shortly to test the 1 megawatt motor and motor controller for the Dash 8-100 demonstrator—developed at Collins’ site in Solihull, England—before initial testing at the University of Nottingham’s Institute for Aerospace Technology.
By late June, Collins had tested the motor drive system up to 400 kW. “So we're almost halfway there,” says Dolan. “We are going to continue testing to make sure the machines are working just as we planned. We're sort of stretching the limits right now on the test and so we're working with the University to improve that, and we'll continue that testing later this year. Our plan includes integrating this with the engine at Pratt & Whitney and do engine-integrated engine testing.”
The motor will have four times the power density of “our prior best in class,” says Dolan. “As we look at the motor controller, this is going to be upwards of 10 times the power density as our current motor controller on the common motor starter controller on the 787.”