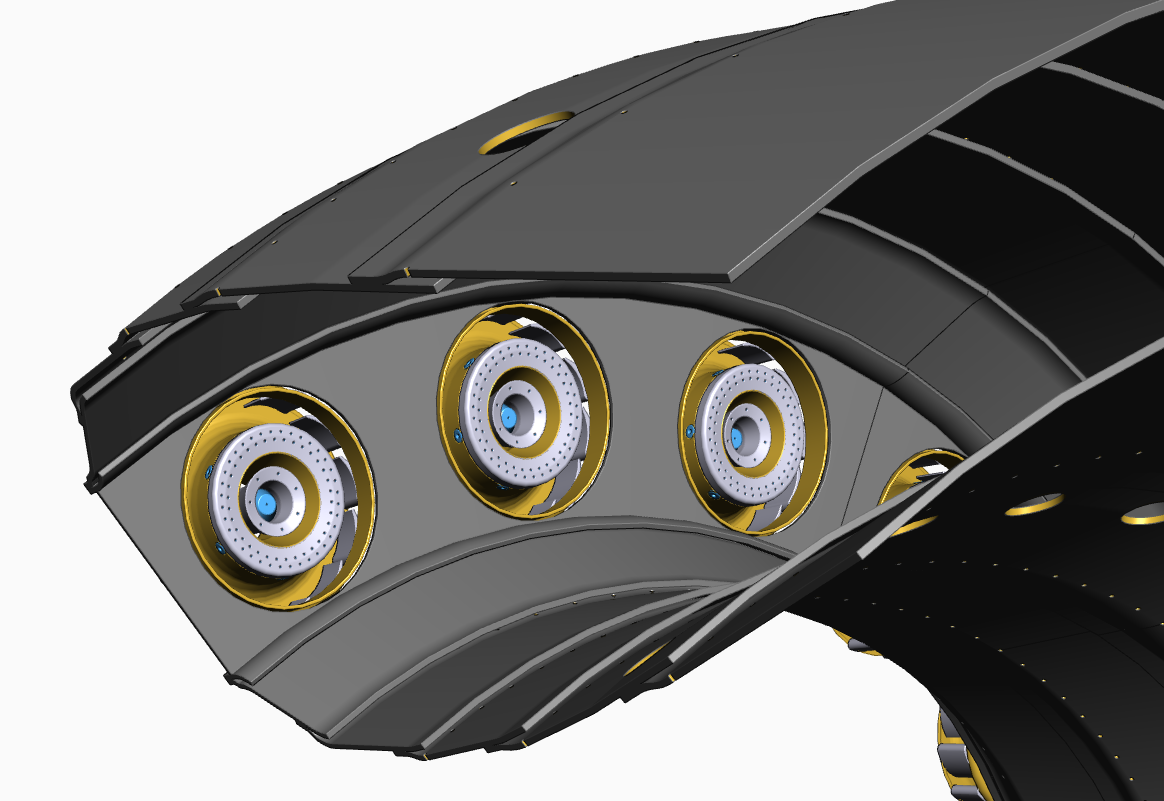
A dual-fuel combustor designed to enable current-generation single-aisle airliners to operate on both sustainable aviation fuel (SAF) and hydrogen is being proposed by UK-based aerospace technology developer Derwent Technologies.
Developed with Burntastic, the UK-based combustion specialist, and aircraft performance firm RAW Aviation Consulting, the Derwent concept builds on existing engine-combustion technology but aims to minimize changes to current aircraft design. By adding wing-mounted tanks for hydrogen and retaining the standard fuel system, Derwent says a modified Airbus A320 configuration could see a cut of more than 50% in CO2 emissions over typical 800-1000-nm missions.
Derwent says the key to the dual-fuel combustor (DFC) concept is that it does not attempt to use both fuels over the full-thrust range. “It provides a hydrogen feed to a burner pilot zone to provide stable combustion for low-power operation by exploiting the wide burning limits of hydrogen. Independently controlled kerosene and hydrogen feeds are provided to the main burner,” the company says states.
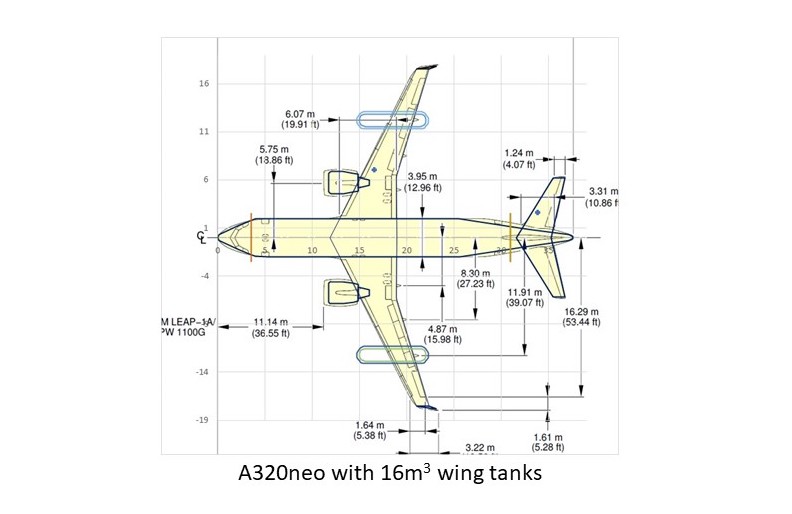
The hydrogen feed to the main combustion burner is intended for cruise only, while the kerosene supply is delivered to the main burner for takeoff and climb and all other conditions, Derwent says. However, while the hydrogen flow rate at cruise can be varied, Derwent says some quantity of hydrogen must be carried to supply the burner pilot jet throughout the flight. “This gives flexibility in the choice of hydrogen tank size to optimize the CO2 saving for the majority of flights while limiting the size of the liquid hydrogen (LH2) tank,” the company says.
By restricting the use of hydrogen in the main burner for cruise only, Derwent says the DFC concept avoids the fuel/air ratio mismatch for the zero-carbon fuel if used for takeoff. The higher flame temperature of hydrogen requires more air to be supplied to the primary combustion zone, which would be unacceptable for meeting the cooling air and flame stability requirements when operating on kerosene, the company says.
Among other benefits claimed for using hydrogen mainly for cruise is that the flow-delivery requirement is cut by a third. This means the size of the fuel and heat-management systems can be reduced. Another positive, Derwent says, is that the absolute pressure and temperature conditions in the combustor are also reduced, which lowers the risk of NOx formation—a key concern along with excess contrail formation for hydrogen skeptics—and allows for the retention of a conventional twin annular fuel delivery and distribution concept.
Although Derwent says retaining the kerosene/SAF fuel system for thrust setting and transient control should reduce the functional testing required, the company acknowledges that extra study will be required for low-power operation on the ground using hydrogen and the transition to hydrogen at the start of cruise and back to kerosene for descent. The LH2 would be pumped as a liquid, converted to gas in a heat exchanger external to the engine and stored in a small tank at the pressure required to inject it into the engine.
Working with RAW, Derwent studied various external wing tanks to close in on the optimum balance between the extra weight and drag of the tanks and the reduced CO2. The resulting tank size was 7.8 m (26 ft.) in length with a diameter of 1.8 m, which included an allowance for insulation. Together with the fuel system changes and tank installation, the company estimates the overall operating empty weight would increase by around 1,710 kg (3,770 lb.).
“All the estimates need to be worked in detail with the airframer but do give confidence to the overall result that can be achieved by this approach,” Derwent CEO Charles Cuddington says. The retrofit would likely involve the “complete replacement of the pre-mixers to incorporate the hydrogen pilot, the extra feed to the mains and possible change to the air swirlers,” Cuddington adds.
To progress its idea to the next stage, Derwent hopes to become involved in one of the major hydrogen propulsion research efforts currently underway under the European Clean Aviation initiative. Specifically, Derwent is interested in Clean Aviation’s Cavendish program, a €29.2 million ($32 million) project to integrate lean-burn hydrogen combustion into a Rolls-Royce Pearl 15 donor engine for ground testing on LH2 starting in late 2024.
“The program depends on our discussions with Clean Aviation participants and funding agency; the latter is supportive. The program would be part of the Cavendish project and it is envisaged that the dual fuel element would follow some of the initial work on all hydrogen powered engines,” Cuddington says.