All COMAC C919 Prototypes Now Flying With Nexcelle Nacelles
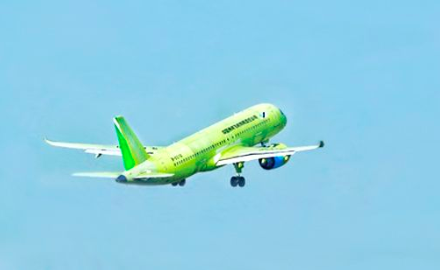
Nexcelle’s state-of-the-art nacelles on the COMAC C919 are being put through their paces as all six prototypes of the twin-engine commercial jetliner have joined the aircraft manufacturer’s flight test program.
The No. 6 C919 performed its maiden takeoff in late December from Pudong International Airport, located adjacent to COMAC’s Shanghai final assembly line facility. The initial flights of two other prototypes (No. 4 and No. 5) also were conductedin 2019. The first three C919s took to the skies in 2017 and 2018.
With the test program in full swing, C919s are now flying from four locations in China: Pudong in the Shanghai region; the flight test center of Yanliang, situated in Shaanxi province; Dongying in Shandong province; and Nanchang in Jiangxi Province.
The C919 has one of the world’s first truly integrated propulsion systems, resulting from the close cooperation of Nexcelle as the nacelle supplier and CFM International, manufacturer of the LEAP-1C powerplants.
Nexcelle is supporting the accelerated flight test pace with the resources of its two parent companies: Safran Nacelles in France and U.S.-based Middle River Aerostructure Systems (MRAS). The Nexcelle joint venture has established a presence in China, with its primary team located at COMAC’s Shanghai Aircraft Design and Research Institute (SADRI) in the Xuhui District of Shanghai. For the build-up of nacelles and engines into complete integrated propulsion systems, Nexcelle and CFM International have an integration area located adjacent to the C919 final assembly line at COMAC’s Shanghai Aircraft Manufacturing Co. location near Pudong International Airport.
Based on Nexcelle’s work-sharing arrangement with its parent companies, Safran Nacelles has the C919 nacelle system’s lead industrial role, supplying the O-Duct thrust reverser that was developed through Safran Nacelles’ innovation program. The O-Duct reduces weight, increases thrust reverser efficiency and facilitates engine maintenance. Its “clean” configuration (when compared to traditional D-duct thrust reversers) eliminates drag links in the engine’s secondary flow-path, enhancing the airflow path and improving fuel consumption – while also increasing thrust reverser efficiency. Improved engine maintenance is another advantage of the O-Duct design, resulting from easier access to the LEAP-1C’s engine core and the thrust reverser components.