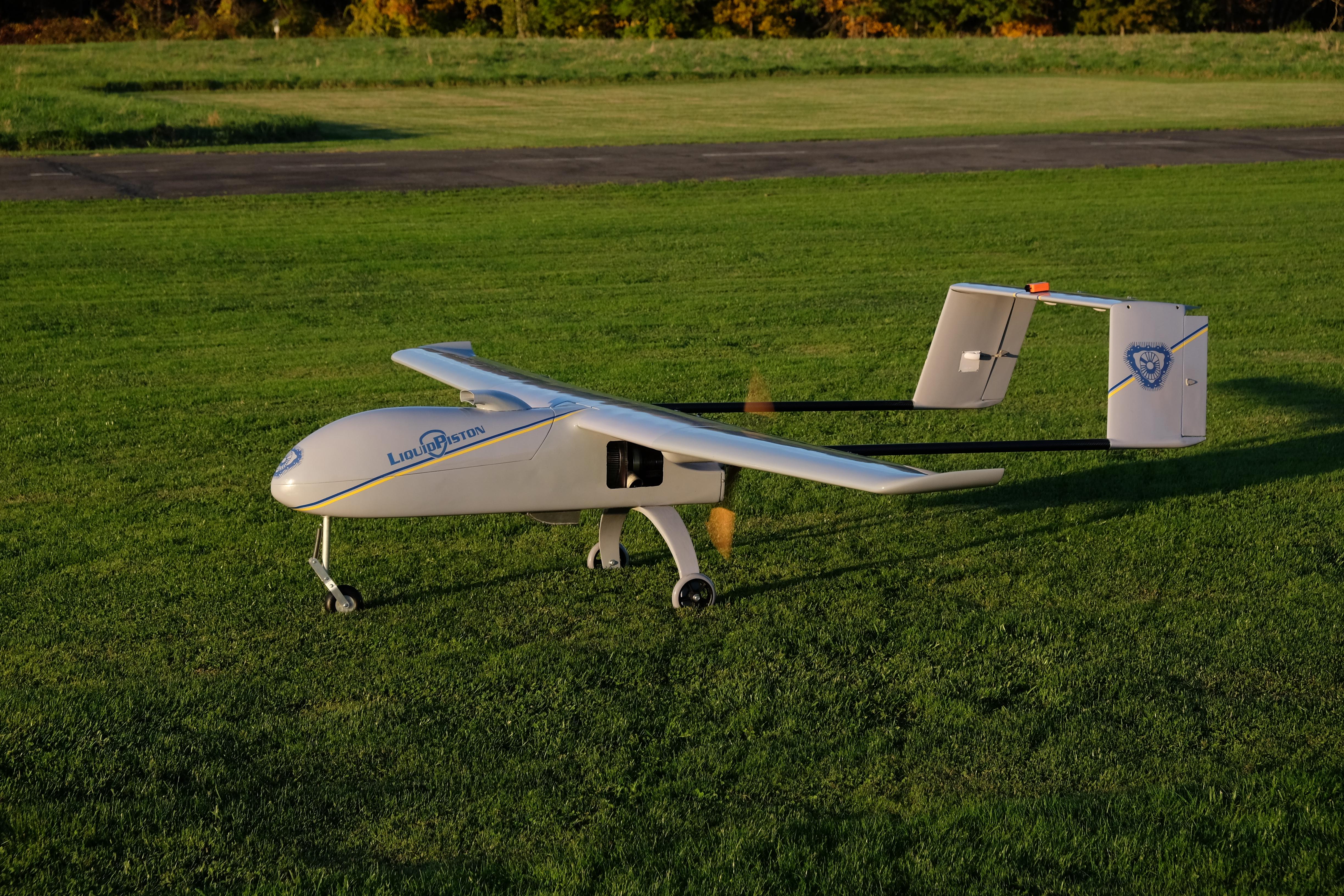
Development of compact, efficient rotary internal-combustion engines able to run on jet fuel has been boosted by U.S. Army contracts to advance the technology for unmanned-aircraft propulsion and rotorcraft auxiliary-power applications.
Startup LiquidPiston has received a small business innovation research contract to develop its X-Engine as a hybrid-electric propulsion system for unmanned aircraft. The company has also won a prize competition to develop a version of the X-Engine as an auxiliary power unit (APU). Both contracts are aimed at supporting the Army’s Future Vertical Lift (FVL) initiative.
The X-Engine resembles a Wankel rotary turned inside out. Instead of a triangular rotor inside an oval housing, it has an oval rotor in a triangular housing. In a Wankel, apex seals on the rotor move in and out at high speed during rotation and are difficult to lubricate. In the X-Engine, both apex and face seals are mounted on the stationary housing and are lubricated directly, improving durability and reliability.
“When we reimagined the rotary engine with the X-Engine, we knew it could be used to improve power generation in a number of different ways, given its high power-to-weight, efficiency and ability to run on heavy fuel including Jet-a/JP8 fuel,” CEO Alec Shkolnik said in a statement.
Bloomfield, Connecticut-based LiquidPiston is aiming the X-Engine at powering the vertical-takeoff-and-landing Future Tactical Unmanned Aircraft System being developed under FVL, as well as providing auxiliary and supplementary power in manned fixed- and rotary-wing aircraft.
Scalable from 1-1,000 hp, the X-Engine has a high power density of up to 1/5 hp/lb. The design is 30% smaller and lighter and 50% more fuel efficient than spark-ignition gasoline engines, with reductions of up to 80% and 30%, respectively, over compression-ignition diesel engines, according to LiquidPiston.
The company built its first working diesel X-Engine in 2012, demonstrating the new architecture and thermodynamic cycle, called the high-efficiency hybrid cycle. In January 2019, the company demonstrated a 40-hp diesel X-Engine core under a $6 million DARPA contract.
In July 2019, LiquidPiston delivered a hybrid JP8 generator to the Army under a Rapid Innovation Fund award and, in October last year, the company flew an unmanned aircraft fitted with a parallel hybrid-electric propulsion system powered by the X-Engine running on jet fuel.
The X-Engine is suited to hybrid propulsion because of its compact size and fuel efficiency, the company said. Configured as a parallel hybrid—where both engine and battery drive the propeller—the X-Engine can be shut down, allowing the UAV to operate in electric-only quiet mode, and then restarted in flight.
“The ability to do this on jet fuel has not previously been demonstrated in other vehicles currently fielded,” LiquidPiston said in a statement.
In auxiliary power applications, the X-Engine approaches the power density and packaging of a gas-turbine APU, but with the greater efficiency of a diesel engine, according to LiquidPiston. The X-Engine APU is designed for use on the ground and in flight to offload the main engines and provide supplementary power for systems, avionics, cooling and weapons.