
Flying Colours Corp. has introduced a new digital training program that it says has become a valuable asset during the pandemic, connecting employees across its locations in Canada, the U.S. and Singapore to continued training opportunities despite travel restrictions and social distancing requirements.
The MRO implemented the in-house eLearning platform pre-pandemic as a long-term solution for sharing knowledge and skills across the company in light of its expansion plans, which include a new paint facility opened earlier this year at its Peterborough, Ontario headquarters and its accompanying hangar extension, as well as plans to triple its capacity at the Bombardier Service Centre at Seletar Airport in Singapore.
Since the eLearning platform’s rollout, more than 100 global employees have accessed courses in areas such as maintenance, avionics, paint, upholstery and cabinetmaking. The digital training efforts are being led by Flying Colours aircraft technical trainer Spencer Hoggarth, who is being supported by training leads from each department to guide course content, including providing materials such as document reviews, assessments, subject matter expert videos and necessary exams.
“In a dynamic industry, and with current travel and social distancing restrictions, it’s challenging to stay current with the latest techniques,” says Hoggarth. “Continual training is vital for the industry and for our workforce, which is why we’re investing in the new tech. The customizable digital platform gives us the ability to create content relevant directly to Flying Colours Corp., the industry and our customers.”
According to Flying Colours executive vice president Eric Gillespie, each course varies from 3 to 25 mins. and Hoggarth’s team is working to keep courses engaging through smart use of imagery, videos and interactive components. Time spent in each course is tracked and counts towards students’ total training for the year and Flying Colours says the reduction in travel has helped it save time and money.
“The training is already demonstrating benefits in terms of the skills development and professional improvement for technicians,” says Hoggarth. “This is helping with company productivity, which enables us to keep meeting and exceeding our customer expectations.”
Gillespie adds that the platform’s intuitive interface is helping Flying Colours track progress and ensure that each department is current. “Simply logging on to view the status of each department is much more convenient than having to trawl records to establish who needs what. That’s a huge time-saver,” he notes. “A major benefit of running the online training is that a new recruit starting in six months will receive the same training as people that are already working. By synchronizing the training, repeat mistakes are mitigated and efficiencies improved.”
In addition to this digital learning initiative, Flying Colours has begun using tablets or smartphones to perform virtual tours for customers of aircraft that are undergoing work. Normally customers would visit in-person at various points during the project to see updates on the progress, but Flying Colours says it is optimizing digital technology to keep in regular contact and provide updates. It anticipates that some of these processes will remain in place post-pandemic due to their successful application so far.
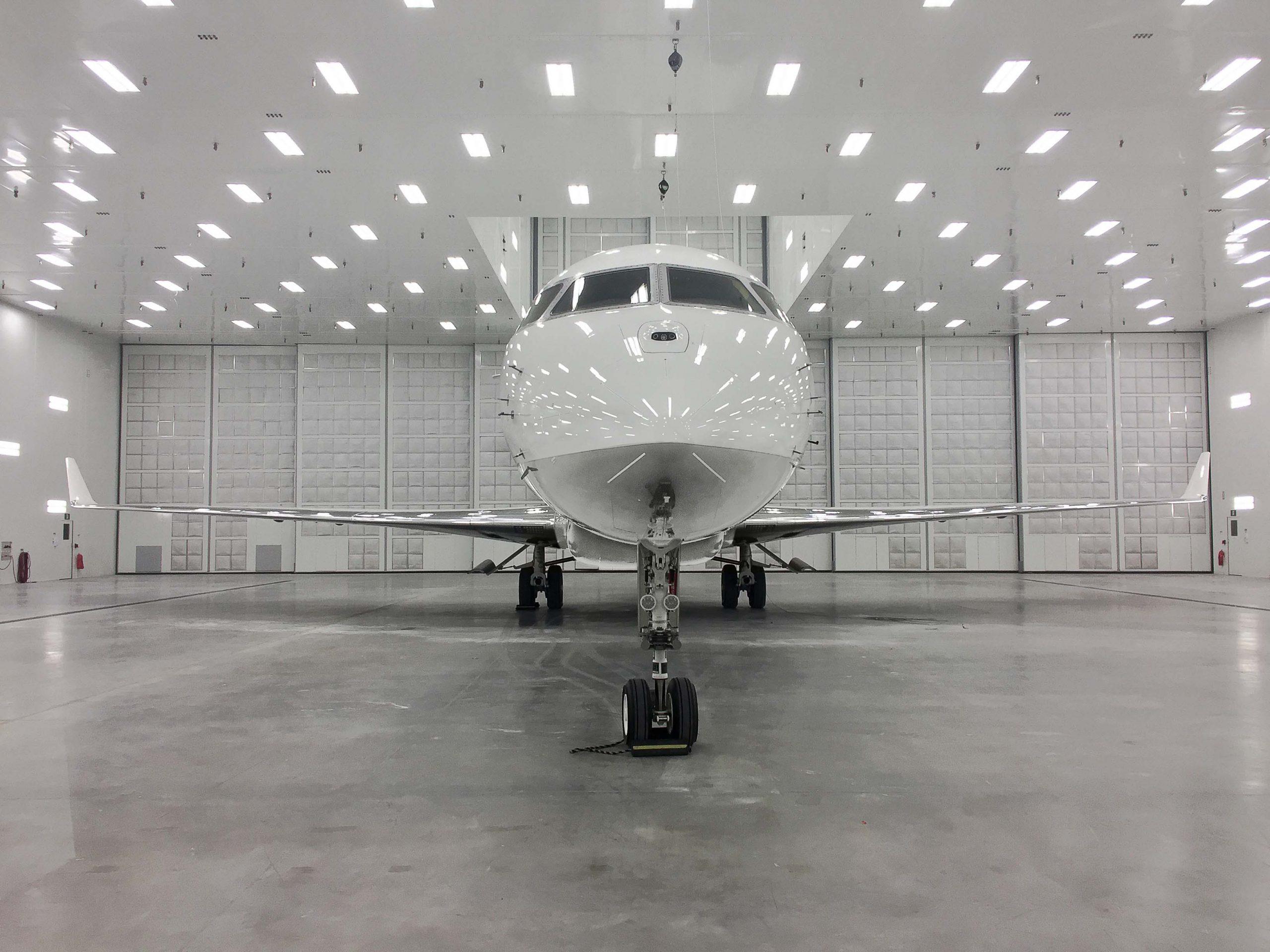
Although COVID-19 circumstances have delayed its expansion projects in Peterborough and Singapore, both are still going ahead as planned. The Peterborough paint facility, opened in January, is the first part of its CAD$25 million (approximately $19 million) hangar extension project. It says that when phase two is completed, the 100,000 ft.2 extension will enable it to run projects in parallel to reduce downtime, maximize budget and ensure projects finish on time.
In Singapore, it plans to recruit new team members, acquire new equipment and adjust workflow layout to accommodate the added capacity. It will add three large spray booths, a second sanding booth and an additional polishing room, which will feature high efficiency ventilation and filtration systems. It says the polishing room will support repairs of the increasingly popular granite countertop surfaces used in aircraft galleys and lavatories.
As a result of the COVID-19 pandemic, Flying Colours says it has started receiving inquiries about medevac operations and from companies exploring the option of buying a regional jet and converting it to corporate shuttle format. It has received more requests for work related to stowage areas for masks, hand sanitizer, foot coverings and gloves. It also signed a distributor agreement with Aviation Clean Air (ACA) in July to act as an installation facility for its aircraft purification components. So far it has installed ACA units on three Bombardier Challenger 300s and Gillespie says the unit is “featuring in pretty much every conversation we have about interior refurbishment,” so it anticipates demand will continue for the foreseeable future.