
Nozzles for new RS-25 engines are in production at Aerojet Rocketdyne to power NASA’s later Space Launch System flights.
As Aerojet Rocketdyne continues production of its traditional large engines for NASA and United Launch Alliance vehicles, the manufacturer sees the emerging cislunar economy as the potential catalyst for the launch of a new generation of low-cost, liquid-fueled rocket engines.
As far back as 2013, the company outlined development plans for an initial family of smaller additively manufactured Bantam engines covering the 5,000-30,000-lb.-thrust bracket, and it is now talking with launch vehicle developers about a much broader power range. “We’ve shifted toward a smaller set of engines, and it’s a thrust range that could go from 5,000 lb. to 150,000 lb. focused on kerosene—but could also be easily hydrogen or storable,” Jim Maser, senior vice president of Aerojet Rocketdyne, told Aviation Week on the sidelines of the Space Symposium in Colorado Springs on April 18.
- New RS-25 certification planned by year-end
- Low-cost engine is aimed at cislunar roles
Although test and development of the smaller Bantam engines has been underway for about a decade, Maser said the company’s well-honed additive production capabilities as well as the emergence of a new generation of small and medium launch-vehicle developers provides the company with a fresh set of potential market opportunities.
“There are all these guys announcing they’re moving to a medium launch vehicle, and they’re all vertically integrated,” he noted. “We have talked to all of them, and we think at some point they are going to realize that they’re in the business of putting things in orbit. They’re not in business to make rocket engines. I think as capital markets dry up people are going to recognize the value in that,” he added.
“We think the Bantam class is the way to go because that gets into a more affordable regime,” Maser continued. “You still need to have a business case, so it comes down to [the fact that] no one wants to pay for development. But they don’t want to commit to a large number of engines, and so it is hard to figure that out. I’m willing to place a bet—we just have to pick the right company, and they have to be motivated to work with us.”
Although Aerojet Rocketdyne does not identify specific potential applications, the market situation is “very dynamic right now, and things are changing fast,” Maser said. “‘We’re positioning for opportunity’ is how I’d characterize it.”
Another factor adding to more favorable conditions for a potential new application is the rapidly expanding in-space propulsion market to support the emerging cislunar economy.
“What we’re really focused on is the in-space market, where I see a lot of opportunity,” Maser said. “People want to go all the way out to the Moon and back—and it involves a lot of maneuvering—that’s where the real opportunity is.”
The smaller engine option could enable a mix-and-match approach, Maser said. “You could have a booster with five engines and an upper stage with one or two, or a booster with three engines and an upper stage with one, depending on the class or rocket you want,” he said. “We’ve been talking to people about that concept, but I think in terms of liquid rocket engines, that’s probably the future for us.”
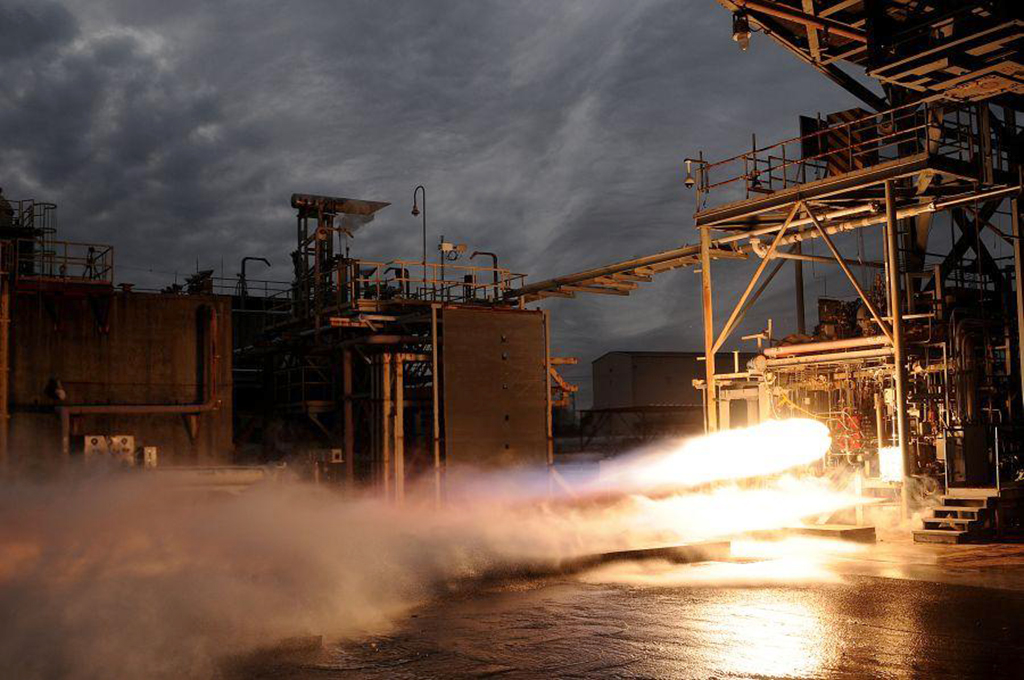
Work on the Bantam, originally based on the injector of the Atlas Sustainer engine, has continued since hot-fire tests of the smallest variant, dubbed the Baby Bantam, were conducted in 2014. Three years later, under a DARPA-supported program, Aerojet Rocketdyne also completed a series of hot-fire tests on a 30,000-lb.-thrust-class version. “We’re investing internal research and development in this family of engines, so I think it has the best potential for us,” Maser said.
Aerojet Rocketdyne is meanwhile midway through certification tests of the first new-build RS-25 engine version that will power the core stage for later missions of NASA’s super-heavy-lift Space Launch System (SLS) rocket.
The first all-new RS-25 built in more than 15 years incorporates improvements introduced into the refurbished former space shuttle RS-25s that Aerojet Rocketdyne also is providing for the initial SLS flights for NASA’s Artemis program, the debut mission of which launched on Nov 16. The company recently completed the four RS-25 engines for the planned Artemis III lunar-landing mission, scheduled for launch around the middle of the decade.
Since only 16 engines remained from the shuttle program—enough for the first four Artemis missions—Aerojet Rocketdyne is building 24 new RS-25 production engines for missions Artemis V and following.
The certification engine and a development engine are undergoing hot-fire testing this year to verify the design for production. The effort includes 12 tests culminating in a design certification review at the end of the year. Tests of a retrofit engine incorporating a combination of heritage and new components will help assess “additional life on some of those parts,” Maser said.
The certification engine is “running amazingly well,” he noted. “Part of the advantage of this when you go to an engine that has this kind of flight history, with reusability, is that you really understand the engine. And it’s the highest-performance hydrogen engine from an efficiency perspective.”
The tests underway at NASA Stennis Space Center in Mississippi will evaluate the engine performance through a series of design conditions and excursions. The work will validate improved components, such as the nozzle, main combustion chamber and pogo accumulator assembly—an additively manufactured part that is designed to dampen oscillations caused by propellants as they flow between the vehicle and engine.
The 12 runs will amount to a total of 6,150 sec. of hot-fire time; the test engine will burn at an average of 111% capacity for more than 500 sec. on individual tests. The higher thrust rating is an increase from the shuttle program at 104.5% and the Artemis I-IV missions at 109%. On the fourth test, conducted on Stennis’ Fred Haise Test Stand in late March, operators fired the certification engine for 10 min. (600 sec.), longer than the 500 sec. engines must fire during an actual mission.
“We’re certifying it at 113%, and it’ll run up to 111%,” Maser said. “The unique thing about the RS-25 is, because you have the big solid boosters on SLS, the core stage is halfway between the first stage and the second stage. So the RS-25 basically takes the core stage to orbit. That’s why that engine runs 500 sec., compared to most first-stage engines in a traditional rocket design in which they will typically run 250 sec.”
As work proceeds toward the design certification review, Aerojet Rocketdyne also is ramping up production. “Our big focus now is coming down a learning curve and just cranking out a stable design, reliably with high quality and as cost-effectively as possible,” Maser said.
New production processes and manufacturing technology have aided the company’s bid to cut costs by 30% on an engine design that dates back to the 1970s. “We’ve implemented additive where it makes sense, and that’s going to save us a lot of money, increase producibility and reduce the part count,” Maser explained. “There are a lot of piece parts that had some intricate hand welding, and we simplified it by going to far fewer parts with automated robotic welding in a number of cases. Now it’s just a learning curve and efficiency.”
Between the first and fourth nozzles, the company says it reduced tube-stacking touch-labor hours by 50% and on the fourth nozzle beat an affordability target by 17% and reduced scrapped tubes by 90% compared with the previous three.
In other areas, the RS-25 engine design was simplified by using solutions from the J-2X and RS-68 programs. By modifying the ducts that carry propellants from the SLS rocket to the turbopumps, Aerojet Rocketdyne says it saw a 62% reduction in cost for the ducts on the RS-25. “On the powerhead, which serves as the structural backbone to the RS-25, the team was able to eliminate 1,200 parts and reduce fabrication time of the first unit by 15%,” the company says. “The main combustion chamber is produced 22 months quicker with 71% fewer welds.”
Certification testing of the new RS-25 engine is due to be completed in the fourth quarter of 2023; new production engines are planned to begin in 2024. Aerojet Rocketdyne is scheduled to deliver the first shipset of four new-build RS-25s to NASA in 2025. Although the actual launch schedule for this and follow-on Artemis missions may be extended, Maser said: “We’ll be ready whenever they are needed.”