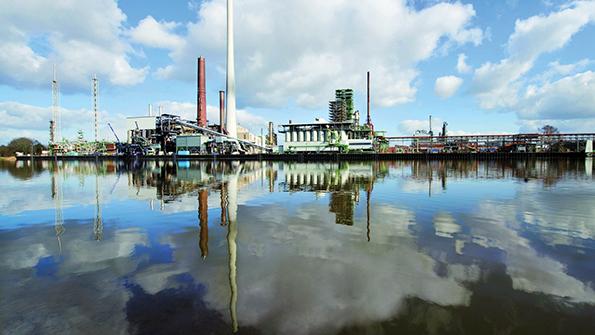
BP’s refinery in Lingen, Germany, is producing SAF through coprocessing.
Enthusiasm over using sustainable aviation fuel as aviation’s main path to reach net-zero carbon emissions by 2050 has matured into a realization that the supply and distribution of SAF must be increased dramatically to achieve its environmental promise.
SAF producers and suppliers say the fuel industry will meet the future consumption demands of aviation only by ramping up coprocessing of sustainable fuel at existing refineries, building standalone facilities to produce 100% SAF and changing the mix of sustainable feedstocks used to extract carbon from fats, oils and greases to biomass, municipal waste and other sources.
- U.S. sets goal of supplying 3 billion gal. by 2030
- Producers cite need for co-processing with crude
- Competition looms for sourcing sustainable feedstocks
Aviation in the U.S. consumed 23 billion gal. of jet fuel in 2019 before the COVID-19 pandemic curbed demand; in 2021, approximately 5 million gal. of SAF were produced domestically, according to the U.S. government. In September 2022, federal agencies released a SAF Grand Challenge Roadmap that lays out a strategy for supplying at least 3 billion gal. of SAF per year by 2030 and enough SAF to meet 100% of aviation fuel demand—pegged at 35 billion gal.—by 2050.
The U.S. Energy Department estimates that the amount of biomass that can be grown or collected annually could be converted into 50-60 billion gal. of advanced biofuels “without impacting agriculture, trade or current uses of biomass,” according to the road map. “[C]ombined, there is sufficient feedstock to meet the projected needs of the U.S. aviation industry if cost, sustainability and production barriers can be addressed,” the department states.
Finland-based Neste, the leading supplier of SAF, says its refinery in Porvoo, Finland, has annual production capacity of about 34 million gal.; with ongoing expansion of its Singapore refinery and modification of its Rotterdam, Netherlands, facility, the company says it will be able to produce 515 million gal. of SAF annually by the end of 2023. In the U.S., Neste says it works with a refiner in Texas to process undistilled renewable diesel from Porvoo into SAF.
Boston-based World Energy has announced plans to produce 250 million gal. of SAF annually by 2024 at its Paramount, California, site and another 250 million gal. annually by 2025 at its biofuel facilities in the Houston Ship Channel. The company has committed to producing 1 billion gal. of SAF by 2030.
Meeting the U.S. government’s 2030 target of producing 3 billion gal. of SAF domestically requires an immediate focus on commercially ready conversion technologies and feedstocks, the SAF Grand Challenge Roadmap advises. It estimates that lipid-based feedstocks using fats, oils and greases, when converted to SAF through a pathway called hydroprocessed esters and fatty acids (HEFA), will represent 90% of the feedstock required to reach the target.
“Going from 5 million to 3 billion gal. per year by 2030 is a 600-fold increase that requires a 122% year-over-year growth in production to 2030,” the road map states. “It is critical this growth starts immediately. . . . At the same time and in parallel, the foundation must be set to achieve the longer-term 2050 goal. More than 400 biorefineries and 1 billion tons of biomass and/or gaseous carbon oxide feedstock will be needed to produce 35 billion gal. per year by 2050.”
Meeting the U.S. government’s 2050 target will require other renewable feedstocks beyond HEFA-based sources to make SAF, including herbaceous and woody biomass crops, agricultural residuals, invasive species from landscape restoration, algae, wet food and municipal waste, animal manures, renewable gases and direct air capture, the road map says. Standards organization ASTM as of 2021 had approved nine conversion pathways.
Despite multiple pathways, competition looms from other industries for renewable feedstocks used in making SAF. Associations representing fuel retailers and trucking interests opposed passage of a SAF blender’s tax credit contained in the 2022 Inflation Reduction Act; they argued that incentivizing SAF production will undercut production of renewable diesel and biodiesel.
British energy giant BP says producing SAF through coprocessing at existing refineries will help meet environmental targets until standalone facilities producing 100% SAF to the ASTM D7566 specification for turbine fuel containing synthesized hydrocarbons pick up the slack.
Existing refineries now can be used to coprocess 5% of approved renewable feedstocks alongside crude oil streams to meet ASTM’s D1655 standard for conventional Jet A fuel, a ratio BP hopes to increase to 30%. BP’s refinery in Lingen, Germany, is already producing SAF through coprocessing.
“The advantage of coprocessing is that it doesn’t require the significant financial investment and time that come with building a new standalone facility,” says Andreea Moyes, Air BP global head of sustainability. “There are currently around 600 refineries in the world. That’s a huge manufacturing resource in terms of the opportunity to help production today.”